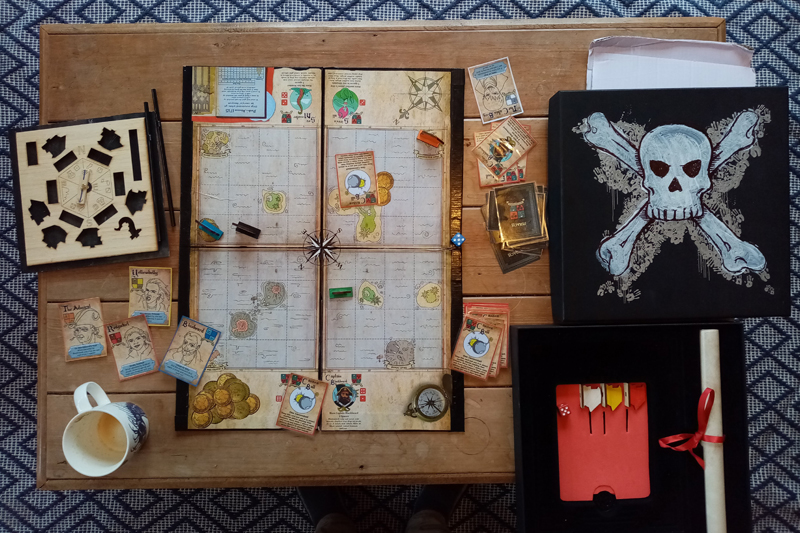
How Nick Ackroyd Uses Laser Cutting To Add The Finishing Touches To Board Games
ICYMI: Board games are trendy again. They’re nostalgic, social and offer a break from oh-so-prevalent screens. While buying Boardwalk and Park Place remains a fun way to spend an evening, board games have evolved with “Settlers Of Catan” leading the way.
For gamers wanting to get in on the action, albeit with a different experience than can be found off-the-shelf at the local Target, Kickstarter has been the place to find what’s new, exclusive and exciting. In fact, more than $165 million was spent on tabletop games via Kickstarter in 2018, an all-time high for the platform.
Clearly, the market is hungry for new board games. While some enthusiasts are designing for profit, others such as Nick Ackroyd are building open-source options to share their love of the game.
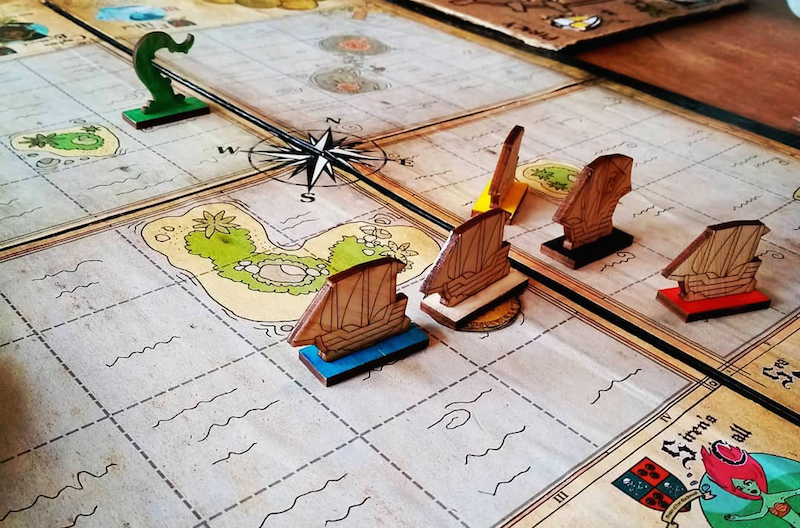
Incorporating Laser Cut Pieces Into The Game Experience
While the board itself along with any cards and packaging are traditionally printed on cardboard, game pieces such as tokens and spinners require materials that are more robust to withstand lots of handling.
You could look for game pieces using off-the-shelf tokens. But you’re more likely to win the lottery than find pieces that exactly match your game theme, are the right size and color, can be purchased at an affordable price—and are distinctive enough to give players a unique gaming experience. Next!
3D printing could be an option as you have complete freedom when creating shapes, but there are several drawbacks: You’re limited to the plastic used in 3D printing, somewhat advanced computer modeling skills are required and the price may bust your budget.
But don’t despair; there is a third option. Laser cutting.
Affordable pricing, quick turnaround and a HUGE materials selection make laser cutting the trifecta of manufacturing. Whether you choose plastic, metal or wood, you can laser cut parts in any configuration you can imagine, ensuring that you have tokens that are true to the game theme and 100% integrated into the overall experience.
Ultimately, these are the reasons Nick used laser cutting to manufacture pieces for “Piracy, Pirates of Port Blackwood,” a family game of burglary, gold and sea monsters. “I chose laser cutting because the steps from drawing to final product are so simple,” he says. “3D design is more difficult and time consuming, and the effect is not as ‘hand drawn.’”
That hand-drawn feel was the aesthetic vibe Nick wanted so the game pieces would align graphically with the treasure map design of the game board.
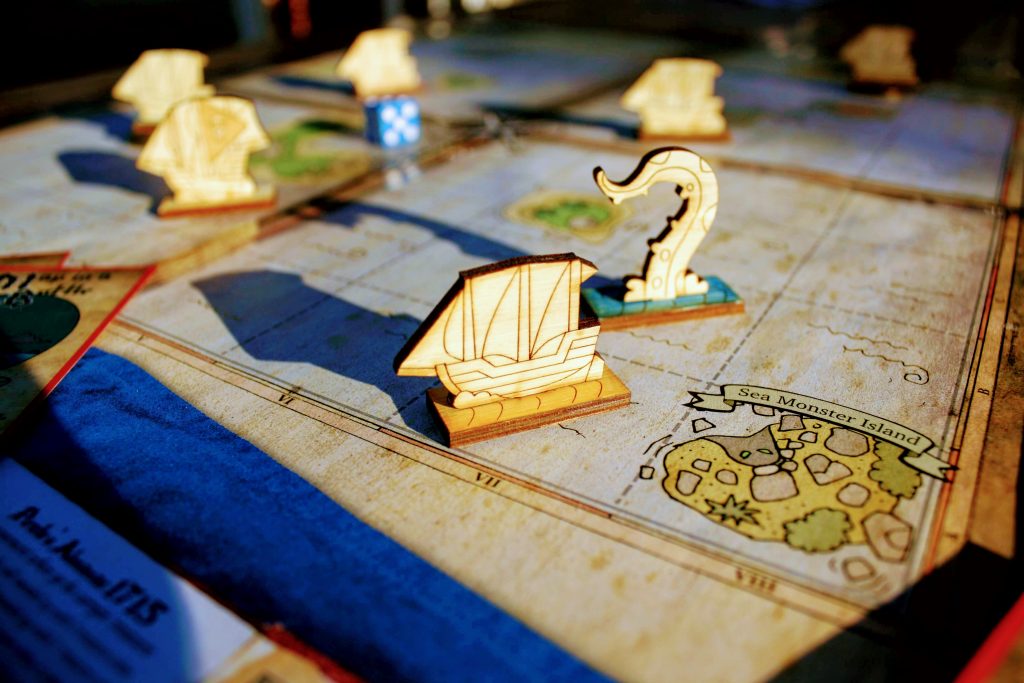
Material choice also played a big role, as the pieces needed an old-world feel. Since, Nick didn’t want to use plastic, he had to find a more sustainable option. “I used 3mm blonde bamboo ply since it is plastic-free and a nice, solid substitute for cardboard,” he says.
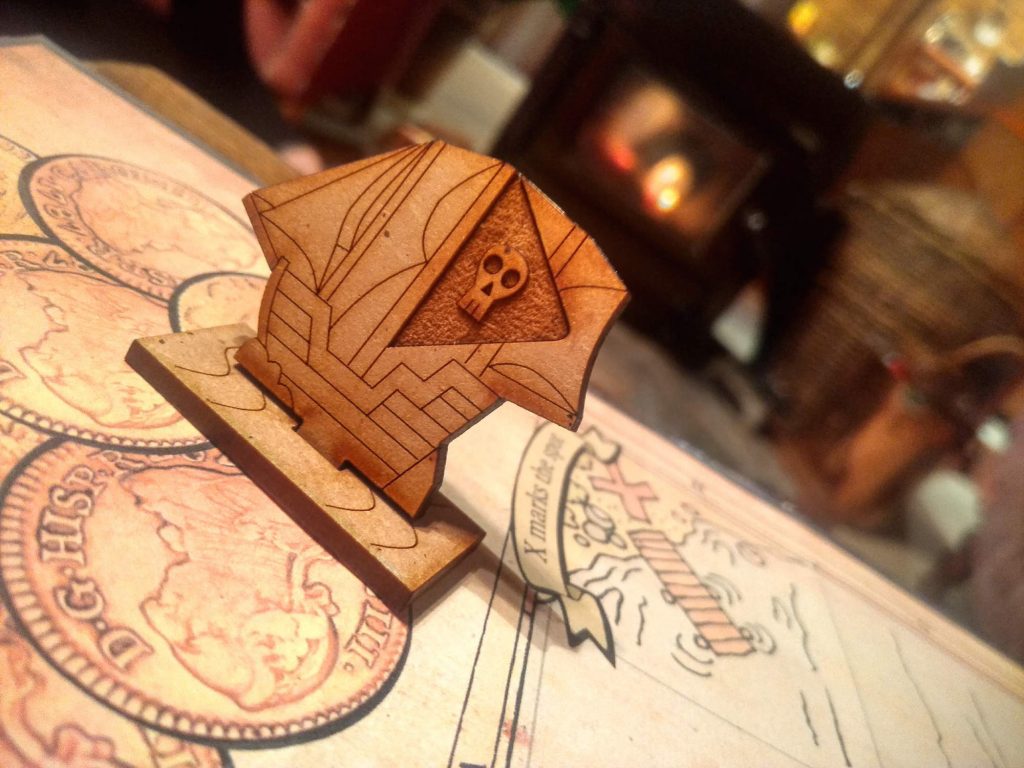
To stay with the plastic-free vision, Nick is moving away from using dice and is building a spinner to direct how pieces move around the board.
Adding The Finishing Touch
We talk a lot on the Ponoko blog about making complete products from laser cutting—anything from electronic enclosures and robots to jewelry and wedding decorations. But the truth is that laser cut parts are used just as often as components of larger designs. That’s the great thing about laser cutting—there’s so much flexibility.
So whether you need tokens for a board game, a faceplate for an electronics build or signage to brand your office, laser cutting has you covered. Sounds like we’ve uncovered a bit of (not so) buried treasure of our own. Savvy?
To learn more about “Piracy, Pirates of Port Blackwood,” checkout the website, Facebook and Instagram.
For another example of how to use laser cutting for game pieces, check out how the Sayre Brothers got all of the pieces to fit for their PentaHex Gaming Platform here.