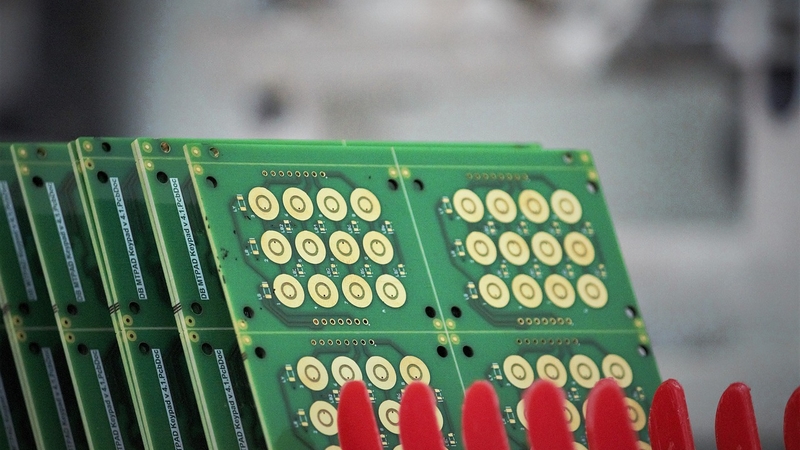
Benefits of a Quick Turnaround Manufacturer
The ability to quickly manufacture PCBs is a valuable asset for any engineer, allowing designers to rapidly test concepts, identify issues, and then utilize the results of prototype designs in future revisions.
Being able to rapidly manufacture PCBs also enables engineers to accelerate their time to market, thereby gaining a competitive edge over others. In highly competitive industries such as technology, being even a few weeks ahead with a product can result in significant revenue gains, and such a lead can be secured with the use of rapid prototyping services. Additionally, the increased speed of innovation enabled by rapid prototyping allows for more design iterations per unit time, thereby increasing the opportunities for integrating new technologies.
However, the ability to rapidly manufacture PCBs can also be essential for securing key component supplies that may otherwise be in short supply. For example, parts crucial to a project that are in short supply are vulnerable to market forces, such as competitors buying up as many components as possible. Thus, being able to rapidly manufacture PCBs means that these components can be acquired and used before anyone else gets a chance to do so.
Finally, the reduced project time enables engineers to reduce their costs significantly, freeing up resources to focus on other important aspects of a project, and potentially opening up new lines of investigation.
Factors to Consider When Looking For A PCB Manufacturer
Choosing the right PCB manufacturer can be a daunting task, and trying to find one that can provide excellent prototypes in a short time frame is even harder. Numerous factors come into play, and it is rare for a PCB manufacturer to have all the answers needed upfront. For example, not all manufacturers are able to handle both PCB fabrication and assembly, meaning that a project requiring both needs to be sent to two separate manufacturers, incurring additional costs and delay times. Thus, it is essential that a manufacturer is able to handle both stages of a project, at the very least for prototypes.
Additionally, manufacturers also need to have access to the full range of components needed for a project, including both commonly used SMD components and bulk wire components. Some manufacturers may only be able to use internally sourced parts, while others may have access to large distributors such as DigiKey and Farnorth. This is particularly a concern for technologies such as FPGAs and SoCs, which often require specialist parts.
Manufacturers also vary in their capabilities, which is essential to consider when designing a PCB. For example, trace width and thickness will be affected by the chosen manufacturer, and these factors will directly impact the design. Therefore, it is important to check the capabilities of a manufacturer before starting a project. Some manufacturers may also be limited on the number of layers and copper densities used, while others may have access to advanced technologies such as buried vias.
If a design requires a prototype in a short timeframe, it is also essential that the chosen manufacturer has the capacity to handle sudden changes in order volume. As such, it is not uncommon to see large semiconductor companies such as Intel and TSMC struggle to produce parts in small volumes, meaning that they are not ideal for prototyping. A manufacturer’s ability to scale their production may also be affected by their use of advanced technologies, meaning that a prototype may take longer to produce than expected.
Finally, some designs integrate intellectual property such as encryption cores and processor modules, meaning that the manufacturer needs to be able to protect designs and parts. Not all manufacturers will have such capabilities, so it is essential that a manufacturer is reputable and trustworthy. The speed at which prototypes are being produced also means that designs are being shared with manufacturers more readily than ever. As such, it is essential that a manufacturer can be trusted with a design.
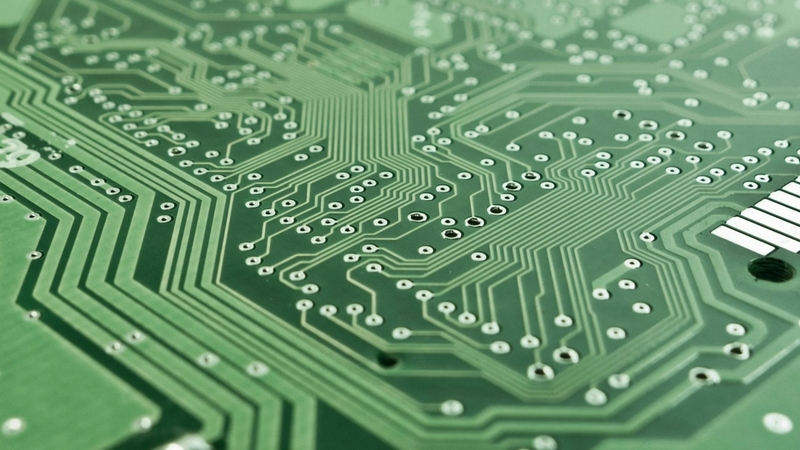
How to Find a High-Quality PCB Manufacturer with Fast Turnaround Times
When it comes to manufacturing a PCB, it is essential that engineers carefully curate a list of potential suppliers that can meet the project’s requirements. One method that can greatly help engineers is to create a chart that compares each manufacturer’s capabilities, such as the types of PCB substrates they work with, the minimum feature size, and the maximum number of layers.
However, before even delving into the finer details of a manufacturer’s capabilities, it is important to research the manufacturer’s reputation. A PCB manufacturer’s reputation can often be indicative of the quality of their services, with reputable companies being more likely to have industry recognition and respect. However, checking a manufacturer’s reputation can also provide engineers with an indication of their reliability and ability to handle projects efficiently, which is also critical in avoiding delays.
In addition to a manufacturer’s capabilities and reputation, it is also important for engineers to check the certifications that they hold. For example, ISO 9001 is a widely recognized quality management standard that ensures processes and systems are carefully controlled to produce consistent high-quality results. Other certifications, such as UL-796, IPC-6012, and ITAR, can also provide engineers with assurances on the quality and safety of their circuits.
Another essential consideration when selecting a PCB manufacturer is the components that they can use. Engineers often have specific components in mind for their projects, and these may not be available from all manufacturers. As such, it is important to check which distributors a manufacturer works with, and whether those distributors offer the components needed for a project. Additionally, engineers should also check if the manufacturer charges extra for non-standard components, as this can have a significant impact on project costs.
Finally, the location of the manufacturer should also be taken into consideration. While the vast majority of PCBs are manufactured in the far east, it is becoming increasingly common for governments around the world to introduce trade restrictions that prevent products containing certain components from being shipped across borders. As such, the location of a manufacturer can have significant impacts on a project’s ability to be manufactured and distributed.
In summary, selecting the right PCB manufacturer is no small feat, requiring engineers to carefully consider a multitude of factors. By taking the time to research a manufacturer’s capabilities, reputation, certifications, components, pricing, and location, engineers can ensure the success of their projects, and the manufacture of high-quality circuits.
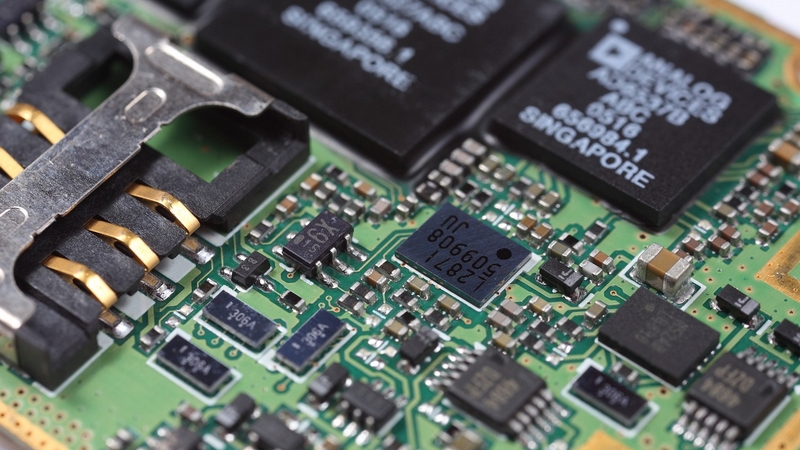
Our Process for Rapid PCB Manufacturing
Getting a project manufactured couldn’t be any easier and faster thanks to our software-powered services. The first step in the process is submitting a design file that is uploaded to our cloud-based platform, which immediately identifies potential issues that may prevent our service from manufacturing the part or parts needed. If such issues are found, our engineers can step in and assist with the project, ensuring a successful outcome.
Once the design has been checked and confirmed, a custom quote for the project is generated, and this can then be paid to initiate manufacturing. At the same time, component sourcing is also initiated, as some components may be sourced from additional distributors. For example, components such as SMD capacitors may be sourced from Mouser Electronics, while through-hole resistors may be sourced from DigiKey.
After the manufacturing stage, all the boards undergo a strict quality assurance process that examines every single solder joint, trace, and component used on the board. This ensures that each and every part leaving our facility is of the highest quality.
Finally, the boards are shipped using our fastest courier service, with same-day delivery available for those in the Oakland Bay Area who place orders before 11 AM, and next day delivery for those in the rest of the US Mainland. Thus, engineers can have their PCBs fabricated, assembled, and delivered in the shortest possible time.
Why Choose Ponoko
When starting a new project, engineers can waste valuable time trying to find the right manufacturers for each stage of their project, and this process can be especially challenging when trying to coordinate different manufacturing techniques. Thankfully, Ponoko has recognised the many challenges faced by engineers and has developed an entire suite of manufacturing services under one roof, including injection molding, laser cutting, and 3D printing. This means that engineers can rely on a single manufacturer for their entire project, including enclosures, fittings, circuit boards, and packaging.
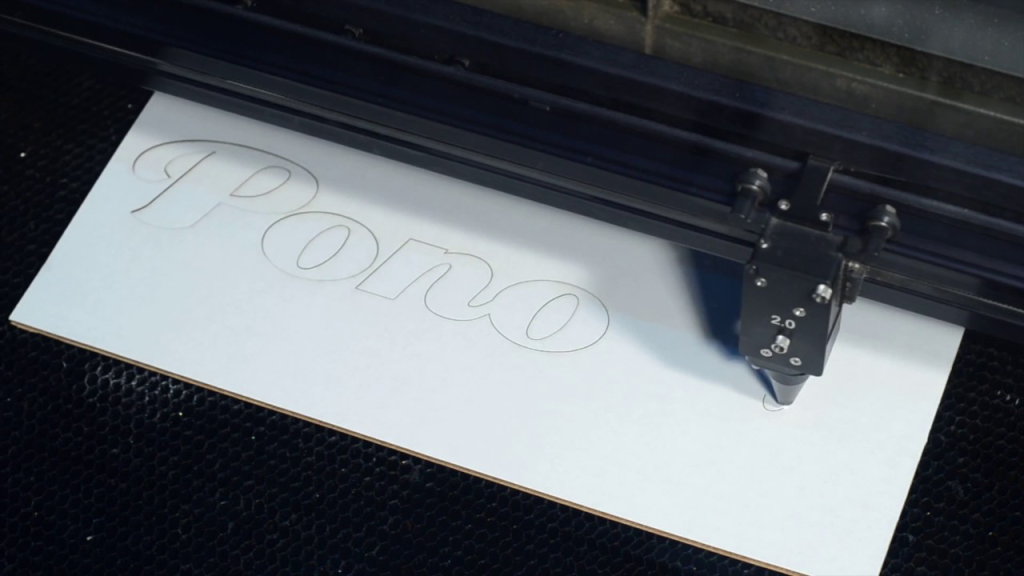
The use of a single manufacturer also significantly helps with project logistics and organization, as all the various departments involved can work together effectively. In particular, projects that require multiple manufacturing techniques can greatly benefit from Ponoko’s ability to coordinate complex projects, even when faced with potential issues. Additionally, Ponoko’s years of experience in the manufacturing field means that engineers can leverage the knowledge and expertise of Ponoko to help solve challenges that typically arise during the production process. As such, Ponoko is able to help engineers from start to finish, transforming their concepts into real, production-level products.