What is Low-Volume Injection Molding?
Injection molding is undoubtedly one of the most cost-effective manufacturing techniques due to the rapid production cycle, high strength of the resulting parts, and wide range of supporting materials. However, this manufacturing technique is only economical when producing parts in the tens of thousands to hundreds of thousands as the initial cost of molds can be extremely high (as one million dollars).

As such, those looking to produce parts in smaller quantities should consider low-volume injection molding services which, as the name suggests, focus on low-volume production. Unlike standard injection molding molds, low-volume injection molds are much cheaper (in the region of a few thousand dollars), and are designed to be used up to 1,000 times. This makes them ideal for prototyping as well as initial production runs for new products, even allowing engineers to make early design changes.
The cost reduction from low-volume injection molding comes down to the use of aluminum molds instead of steel molds. While aluminum is typically more expensive than steel as a metal, it is the ease of machining, ease of recycling, and the lack of precision cutting tools that makes aluminum molds far more economical. While this results in a less accurate mold, this lack of accuracy doesn’t have a major impact during early production runs which helps to reduce the cost of entry.
Overall, low-volume injection molding provides engineers with an economical injection molding option for low-volume production runs, and can help to reduce the price difference between prototypes and initial mass production.
What Types of Projects is it Best For?
When it comes to the production of plastic parts in large volumes, injection molding is one of the most cost-effective solutions. The ability to rapidly produce parts, the high speed of the manufacturing process, and the ability to use reusable molds enables for injection molding machines to quickly scale production from a few parts all the way to tens of thousands. As such, injection molding is ideal for engineers looking to get high-quality plastic parts that will eventually be manufactured in the millions.
One area that heavily benefits from injection molding is the production of electronic enclosures. The high-precision capabilities of injection molding allow for the creation of enclosures that can provide engineers with a high degree of precision, including commercial products, industrial enclosures, and medical systems.
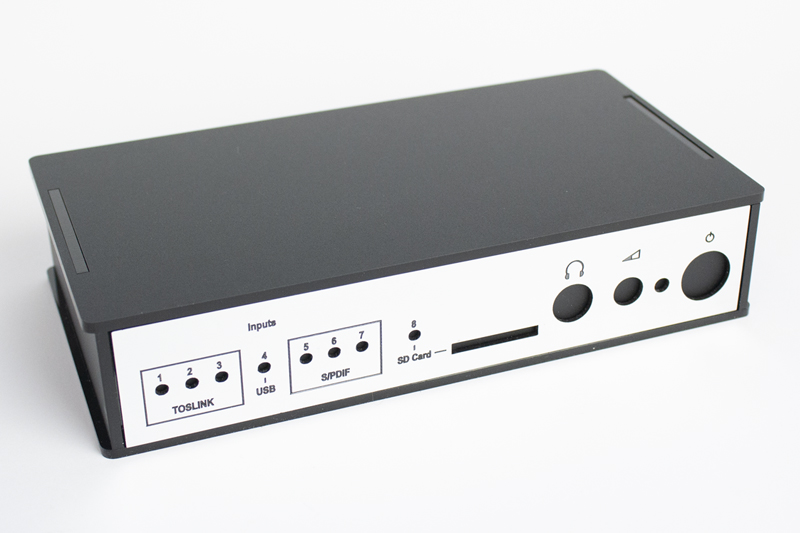
This precision also makes injection-molded parts ideal for wearable devices, which often require the use of custom enclosures that cannot use off-the-shelf solutions. The wide range of materials available to engineers also allows for enclosures to be designed with specific material properties in mind, whether it’s resistance to corrosion or compliance with IP standards.
For those looking to produce 3D plastic parts in small to large volumes, injection molding can also be a great alternative to 3D printing. While 3D printing has the advantage of not requiring molds, it also has the disadvantage of taking a long time to manufacture parts, and the parts themselves rarely have the same strength and consistency as parts produced using a mold. Injection-molded parts, however, exhibit highly consistent strength and material properties throughout the entire part, making it ideal for applications that require structural integrity. This is especially true for brackets, fittings, and enclosures, which often require a high degree of strength, and parts such as enclosures and electronic boards, which need to be able to withstand vibration and reliable operation.
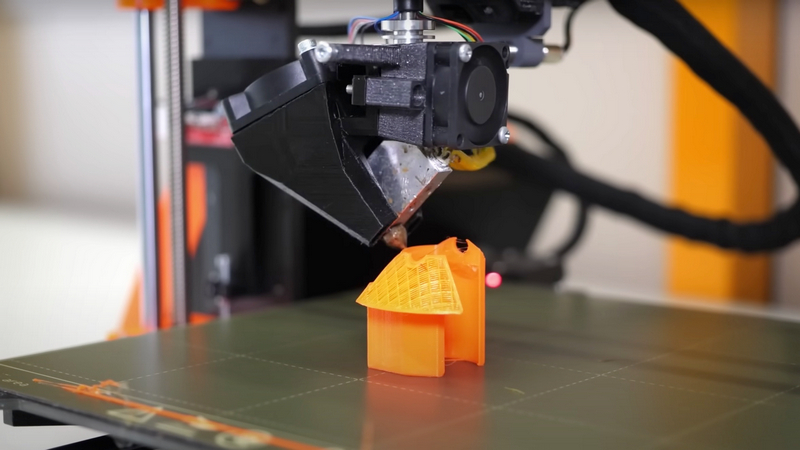
Finally, the high-precision capabilities of injection molding also make it ideal for prototyping parts that will eventually be mass-produced. As such, engineers can use injection molding to prototype parts that will eventually be used in consumer, industrial, and medical applications, thereby ensuring that prototypes truly reflect the final parts. This is especially important for electrical engineers when designing parts such as electrical connectors and fittings that require specific electrical characteristics, including dielectric strength and resistance to vibration.
Step-by-Step Workflow for Low-Volume Injection Molding
When it comes to designing a product for low-volume injection molding, the process is actually quite easier than one would think. The lack of large, expensive molds means that engineers can quickly prototype their parts and make changes as needed.
- To start, the first step that engineers need to take is to design their part in CAD. Once the CAD model is complete, the second step is to ensure that the part conforms to a list of specific requirements that injection molders need to know about. Such requirements include the thickness of walls, the type of material being used, and the tolerances on the part. Not only does checking these requirements help to ensure success with the final part, but it also helps to determine the price of the part which can aid in future design iterations.
- After these two initial steps, parts can then be uploaded to injection molders for further analysis and a quote. As low-volume parts are not using expensive molds, the quote process is generally quick and allows for engineers to make design changes on the fly.
- Finally, once a price has been obtained, payment can be made and the parts manufactured. In the case of low-volume parts, this entire cycle can take as little as 15 days, allowing for rapid prototyping and testing. By far, the biggest benefit to low-volume injection molding is the ability to test a part in a real-world application to get a better understanding of how it performs.
- Overall, low-volume injection molding presents engineers with an excellent rapid prototyping manufacturing service that can help reduce design iteration cycles while also helping to avoid commitment to large, expensive molds.
Part Design for Low-Volume Injection Molding
When approaching the design of a part for low-volume injection molding, it is essential to consider the complex factors that will ensure the success of the final product. Unlike typical part design, injection molded parts require careful planning from the very first sketch due to the intricate nature of the manufacturing process itself.
For instance, plastic flow rate into channels needs to be meticulously planned to ensure even plastic flow and pressure across the entire mold. If plastic doesn’t have a place to go once it has filled a mold cavity, air pockets can form, and this will negatively impact the strength of the final part. At the same time, it is crucial to ensure even pressure throughout the mold to prevent deformation and warping during the cooling stage.
However, gaining the expertise needed to optimize a design for low-volume injection molding can be a challenging task, especially for those without experience in the field. But fortunately, engineers looking to utilize injection molding for low-volume production can turn to specialist manufacturing services for guidance, such as Ponoko.
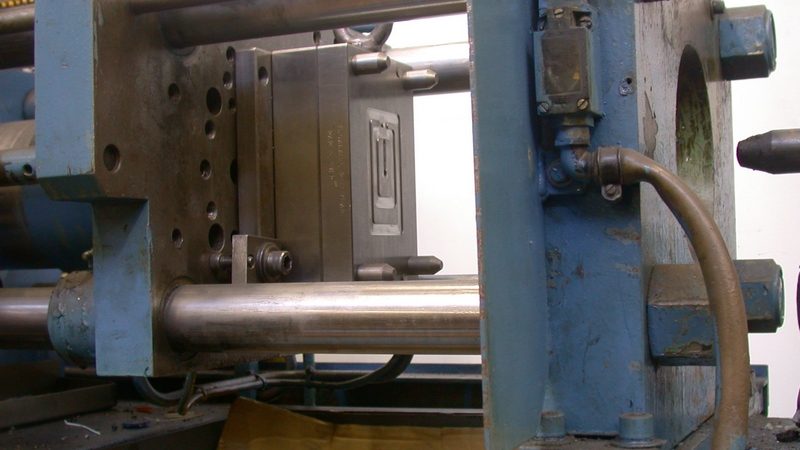
With the help of our engineers who specialize in low-volume injection molding, the complexities of the design and manufacturing process can be efficiently addressed, resulting in the rapid production of high-quality parts.
How to Get Started
When it comes to manufacturing, there is no doubt that injection molding is a superior service for those producing tens of thousands of parts. The ability to use a wide range of different materials, the high-speed manufacturing cycle, and the resulting high strength of the finished parts makes injection molding an ideal service for mass production.
So, for engineers who are looking to get started with low-volume injection molding, the best place to start is by speaking to one of our injection molding experts who can assess whether low-volume injection molded parts are needed. By speaking to our engineers, we not only provide you with valuable insight into the manufacturing process, but may even be able to offer alternative manufacturing techniques that could help extend the budget of your next project.
Why Choose Ponoko
When engineering a product, numerous risks arise at every single stage, and this is especially true for prototypes which can often incur high costs. The transition from a prototype to a full-scale production run can also be particularly perilous, especially if such parts require molds and/or significant initial investments. A single mistake in the mold or design can result in significant setbacks, affecting both the time and funds available for further development and manufacturing.
Due to these potential pitfalls, it is imperative that engineers select manufacturing partners who not only emphasize precision and quality but also reliability. Ponoko has successfully manufactured over 2 million parts for more than 33,000 customers while maintaining a 99.7% precision part quality record, demonstrating our ability to offer consistency and reliability. Our commitment to precision and quality ensures that the transition from prototyping to mass production runs smoothly, reducing the risks associated with design changes and initial production volumes.
At Ponoko, we take an active approach in working closely with our customers, seeking to identify potential issues before they escalate. Our dedication to customer success means that we invest time and resources into ensuring the success of each project, not only promoting our capabilities as a manufacturer but also those of the customer. By collaborating closely with engineers, we can help facilitate the prototyping and production stages, streamlining the entire process and reducing the risk associated with complex projects. Ultimately, our goal is to empower engineers with the confidence to move from prototypes to full-scale production runs with ease.