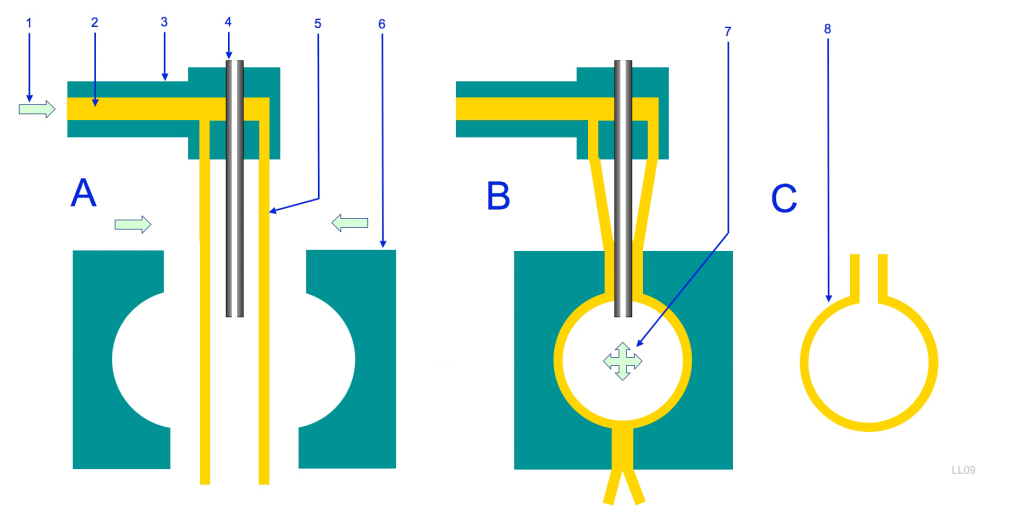
Overview of Blow Molding
Blow molding is a manufacturing technique that plays a pivotal role in the plastics industry for producing hollow plastic parts. Simply put, a heated plastic tube, referred to as a parison, is inflated within a mold cavity to give the tube the shape of the mold. This process is crucial for the production of objects such as containers that need to have uniform wall thickness for strength and durability. The efficiency of blow molding also makes it ideal for mass production as it can maintain high production rates while ensuring consistency in the final product.
Blow molding comes in three main types depending on the specific requirements of the final product with extrusion blow molding being the most common type. This type involves extruding a hot tube of plastic which is then clamped into a mold and inflated with air. The other two types, injection blow molding and stretch blow molding, differ in their method of forming the plastic part with stretch blow molding requiring mechanical stretching before inflation.
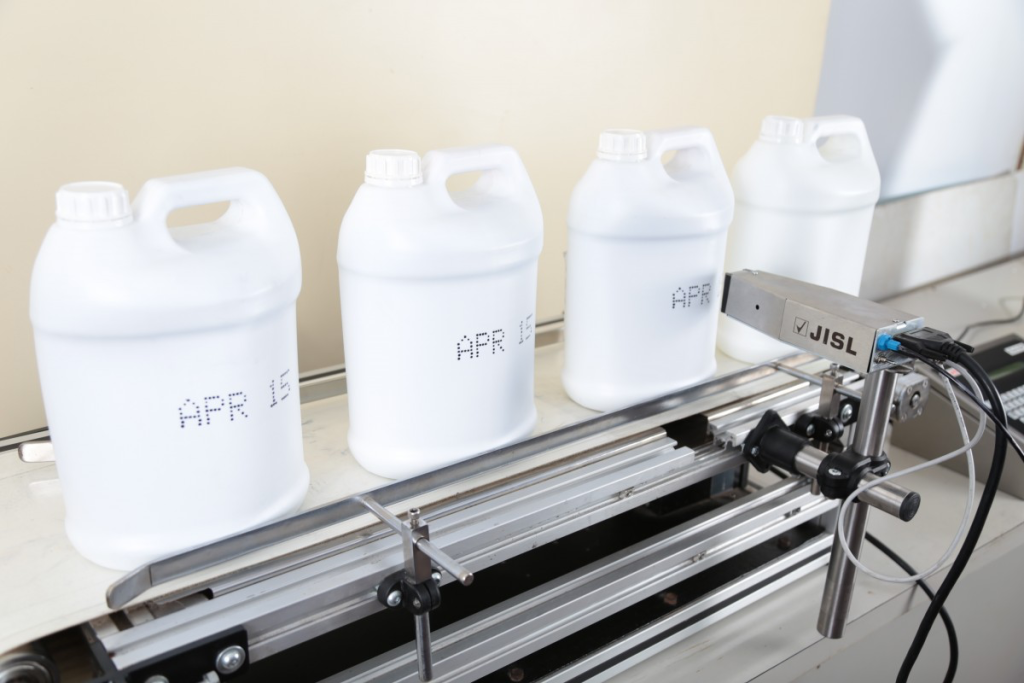
The versatility of blow molding makes it an ideal process for a wide range of applications. The ability to change the mold allows for the production of various shapes and sizes, and this adaptability is essential for manufacturing different types of products including consumer goods, industrial components, and packaging solutions.
From a cost perspective, blow molding is a cost-effective manufacturing process especially when producing high volumes of parts. While the initial setup costs can be high due to the cost of molds, the rapid production cycle and minimal waste help to reduce the cost per unit. This is one of the reasons why blow molding is widely used in the packaging industry.
What is Injection Molding?
Injection molding is a prevalent manufacturing technique used to create solid plastic parts by injecting molten plastic into a mold that has been precisely machined to the desired shape of the final product. This process is renowned for its efficiency and ability to produce parts that are complex and detailed with tight tolerances and excellent surface finishes. Such characteristics are crucial in applications where the precision and appearance of parts are critical such as automotive and electronics industries.
The versatility of injection molding makes it suitable for both low and high-volume production runs. The relatively quick setup of molds and ability to run the process continuously make it a cost-effective solution for large-scale manufacturing.

The process starts with plastic pellets which are fed into a heating chamber and then injected into a mold under high pressure. The high pressure ensures that the plastic fills every part of the mold cavity capturing all details and complexities of the mold design. Once injected, the molten plastic begins to cool and solidify within the mold and cooling systems help to speed up this process. After the plastic has fully solidified the mold is opened and the finished part is ejected. This part can then be used directly or go through additional processes such as painting and plating.
One of the significant advantages of injection molding is its repeatability. The process is highly controlled with advanced machines capable of maintaining precise conditions throughout the production cycle. This repeatability is essential for industries that require consistent quality and precision across large quantities of parts such as automotive and medical industries.
In conclusion injection molding is a critical process in the manufacturing world known for its efficiency, versatility and high quality parts. Its ability to produce complex detailed parts with excellent finishes and tight tolerances makes it a preferred choice across a wide range of industries. Furthermore its suitability for both low and high-volume production runs makes it a cost-effective solution for businesses looking to scale their production.
Blow Molding vs. Injection Molding
Blow molding and injection molding are two cornerstone techniques in the plastic manufacturing field, each suited to different production needs and outcomes. Blow molding is most commonly employed for the creation of hollow objects and involves inflating a hot tube of molten plastic, known as a parison, inside a mold. As air pushes the parison outward, it takes the shape of the mold, resulting in hollow parts like plastic bottles, fuel tanks, and various containers. This method is particularly effective for products that need to contain fluids or air, such as detergent bottles or air ducts in vehicles.
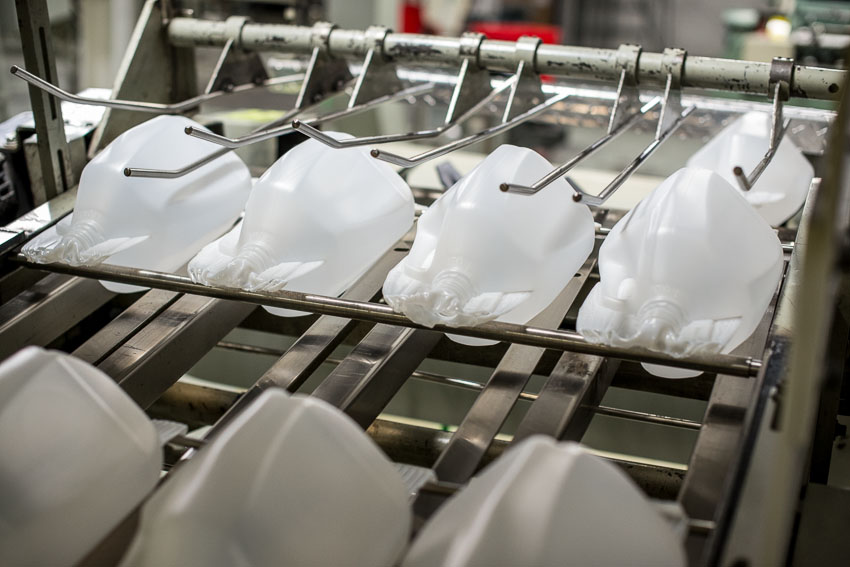
On the other hand, injection molding is tailored for producing solid parts that often require intricate designs and high precision. In this process, molten plastic is injected into a mold under high pressure, which is then cooled to form the desired shape. This technique is ideal for creating items with complex geometries and tight tolerances, such as gears, automotive components, and electronic housings. The ability to incorporate fine details and achieve dimensional accuracy makes injection molding a go-to method for parts that must meet strict specifications.
When it comes to production speed and volume, blow molding generally has an edge in the rapid manufacturing of large quantities of hollow parts. Since the primary operation is the expansion of the parison within the mold, cycles can be completed quickly, allowing for high-volume production runs that are cost-effective and efficient. In contrast, injection molding, while capable of high production rates, excels in scenarios where the complexity and precision of parts are paramount rather than sheer output volume.
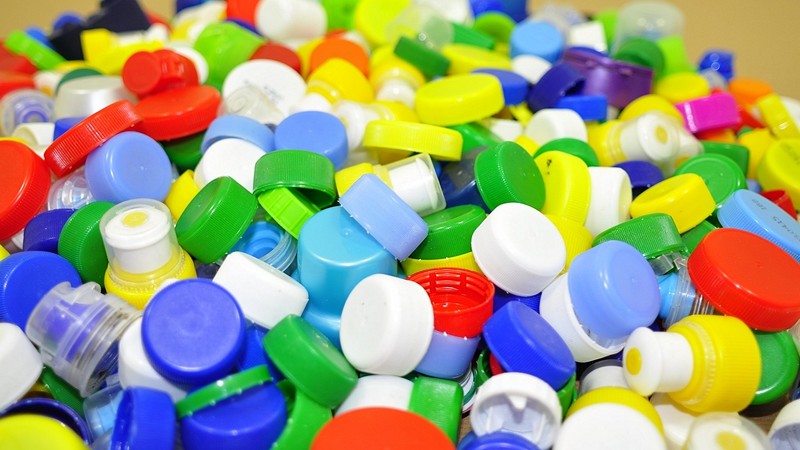
Material versatility is another distinguishing factor between these two processes. Injection molding offers a broader selection of materials, accommodating various types of plastics and additives. This flexibility allows manufacturers to tailor the physical properties of the final product, such as impact resistance, flexibility, or thermal stability, according to specific requirements. Blow molding, while effective, typically utilizes a more limited range of materials, including polyethylene terephthalate (PET), high-density polyethylene (HDPE), and polyvinyl chloride (PVC), which are well-suited for containers and other hollow products but less adaptable to a wider range of applications.
The cost implications of each method also play a crucial role in determining the appropriate technology for a project. Blow molding tends to involve simpler molds and lower tooling costs, which can be advantageous for projects with limited budgets or simpler part geometries. Conversely, injection molding often requires more complex and expensive molds due to the intricate designs and fine details typical of such parts, making it a more cost-effective solution for precision parts.
Pros & Cons of Blow Molding
Blow molding is a highly efficient manufacturing process that is widely used for producing hollow plastic parts such as bottles and containers. Its ability to produce large quantities of parts with consistent quality at high speeds makes it an ideal process for mass production. Everyday items such as water bottles and detergent containers are often manufactured using this technique, showcasing its utility in mass production settings.
The cost-effectiveness of blow molding makes it an attractive option for businesses looking to minimize upfront investments while maintaining high production outputs. The fast production cycles also make it ideal for industries requiring high-volume manufacturing such as the beverage and household products sectors. However, the high-speed nature of the process means that precision is sacrificed, resulting in parts that may not be as accurate or precise as those made using other manufacturing techniques.
Blow molding is also able to create parts with uniform wall thickness, which is essential for ensuring the strength and durability of the final product. The ability to create lightweight parts with uniform wall thickness also makes blow molding ideal for applications where weight is a critical factor. However, the inability to create solid objects or parts with complex geometries restricts the scope of products that can be manufactured using blow molding.
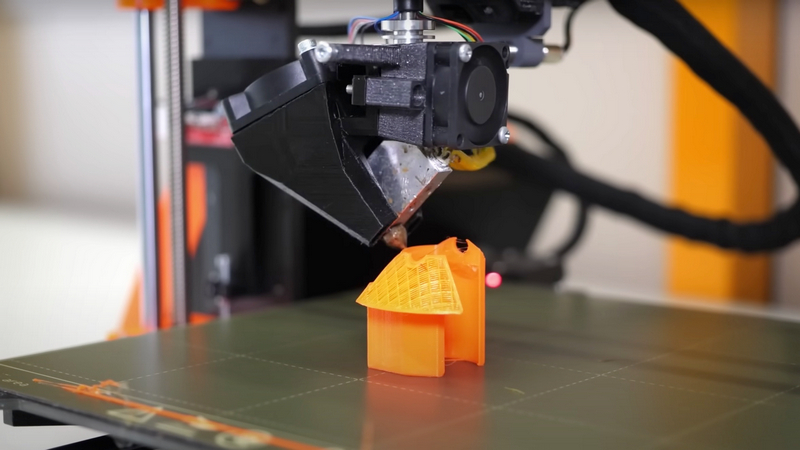
The wide compatibility of blow molding with various plastic materials makes it versatile in manufacturing applications. Common plastics used in blow molding include PET, HDPE, and PVC, each offering distinct properties that make them suitable for various applications. However, the inability to combine different materials in a single product limits the material flexibility of blow molding compared to injection molding.
The design constraints of blow molding also restrict the opportunities for incorporating intricate details into part designs. Features such as undercuts, sharp corners, and complex textures are challenging to achieve, and the resulting surface finish and dimensional accuracy may not be as precise as those achieved with injection molding. Secondary processing steps may be needed to enhance the quality of blow-molded parts.
Pros & Cons of Injection Molding
Injection molding is a manufacturing process widely recognized for its ability to produce complex and highly detailed parts with exceptional precision and surface finishes. It is particularly beneficial in industries such as automotive, healthcare, and consumer electronics, where intricate designs and high-quality standards are paramount. For example, in the automotive industry, injection molding is used to create components like dashboard panels, light covers, and interior switches that require both aesthetic appeal and precise functionality.
The versatility of injection molding is further enhanced by its compatibility with a diverse range of materials. Manufacturers can choose from various plastics, elastomers, and thermosets, depending on the specific requirements of their projects. This flexibility allows for the customization of properties such as strength, flexibility, and resistance to temperature and chemicals, making it possible to tailor parts for specific applications. For instance, thermoset plastics are often used in high-heat environments, such as under-the-hood automotive applications, due to their ability to withstand extreme temperatures.
Another significant advantage of injection molding is its high repeatability, which ensures consistent quality across large production runs. This consistency is crucial for maintaining standardization in products, particularly in sectors like medical devices, where even minor discrepancies can lead to significant issues. The process’s ability to efficiently produce both small and large parts adds another layer of flexibility, catering to a wide range of part sizes and design complexities without compromising quality.
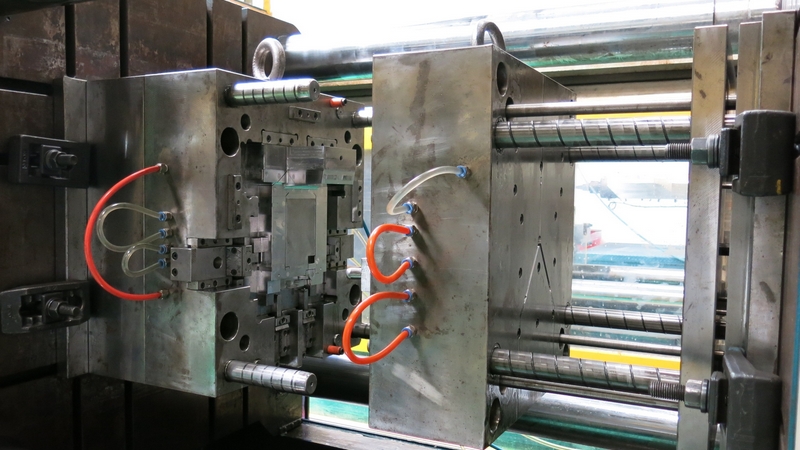
From a cost perspective, injection molding is particularly economical for high-volume production. While the initial investment in the mold might be substantial, the low cost per part achieved thereafter makes it a viable option for mass manufacturing. This cost-effectiveness is a result of the rapid production capabilities and minimal need for post-production finishing, which collectively reduce overall manufacturing costs.
However, the process does come with certain drawbacks. The high initial tooling costs can be a barrier for small businesses or startups. Complex molds with multiple cavities or intricate designs require significant investment, which might not be justifiable for limited production runs. Additionally, the lead times for designing and fabricating these molds are considerably longer, which can delay the overall project timeline. This aspect of injection molding requires careful planning and scheduling to align with product launch dates and market entry strategies.
Injection molding is also not suitable for producing hollow parts without incorporating additional processes or techniques, such as using soluble cores or gas-assist molding. This limitation can restrict design options and increase production complexity. Material selection is also critical, as poor choices can lead to defects such as warping, sink marks, and poor finishes.
Real World Applications for Both
Blow molding is a manufacturing process that involves inflating a warm plastic tube into a mold to create hollow structures, and this process is widely used to create a variety of plastic parts. One common application for blow molding is the creation of plastic bottles that can be used for a range of different liquids including beverages, detergents, and pharmaceuticals. The ability to create airtight containers makes blow-molded parts ideal for preserving the integrity of contents such as medications, while the durability of plastic makes it ideal for repeated use in products such as water and soda bottles.
The food and beverage industry also relies on blow molding for the creation of large parts such as fluid reservoirs and fuel tanks. The durability and resistance to corrosion offered by plastic make it ideal for holding fluids that may be under pressure, and the ability to manufacture large parts economically makes blow molding an ideal choice.
The automotive industry is another sector that heavily relies on blow molding for creating a range of different components including air ducts and storage containers. The precision and accuracy offered by blow molding make it ideal for creating parts that need to fit together precisely, and the durability of plastic can be beneficial when creating components that need to withstand the conditions inside vehicles including temperature swings and vibrations.
While blow molding can be used to create large parts, it can also be used to create small parts including toys and recreational equipment. The ability to create hollow shapes with thin walls makes blow-molded parts ideal for use in ping-pong balls and other similar equipment, and the durability of plastic can be beneficial when creating equipment that needs to withstand repeated use.
An alternative manufacturing process to blow molding is injection molding, which involves injecting molten plastic into a mold to create a solid part. This process is ideal for creating small, intricate parts with complex shapes and is commonly found in the electronics industry.
However, injection molding can also be used to create large parts and is ideal for doing so when creating parts that need to be solid instead of hollow. For example, the use of injection molding to create car parts such as dashboards and doors can take advantage of the high strength of plastic while blow molding would be ideal for creating hollow parts such as air ducts and fuel tanks.
Key Takeaways
The manufacturing industry heavily relies on two primary processes, blow molding and injection molding, each suited for specific applications. Blow molding is ideal for creating hollow, lightweight items and is commonly used to make water bottles, fuel tanks, and plastic containers. Its ability to produce durable parts efficiently makes it a cost-effective solution for manufacturing hollow shapes in large volumes. On the other hand, injection molding is renowned for its precision and repeatability, making it the preferred choice for producing solid, intricate parts with tight tolerances. Components manufactured using injection molding include automotive parts, electronic devices, and medical equipment, all of which require precision and accuracy.
When deciding between blow molding and injection molding, manufacturers must consider several factors, including the part design, material, and production volume. For example, blow molding is cost-effective for producing large quantities of hollow parts, while injection molding is economical for manufacturing complex, solid parts in high volumes. The versatility of these processes extends across various industries, with blow molding used in automotive and consumer goods, and injection molding in automotive, consumer goods, and medical industries.
The choice between blow molding and injection molding ultimately depends on the project’s requirements, with each method offering benefits in terms of production efficiency, cost-effectiveness, and part quality. Blow molding is efficient and economical for simpler, hollow parts, while injection molding is preferred for parts requiring intricate details and high structural integrity. Manufacturers must carefully evaluate which process best aligns with their project goals to achieve success.
Why Choose Ponoko
At Ponoko, versatility and precision are core to our manufacturing capabilities. To cater to the diverse needs of our clients, we offer a range of manufacturing solutions including blow molding and injection molding. While blow molding is ideal for producing hollow parts such as bottles and containers, injection molding is suited for creating high-precision components like gears and automotive parts. This flexibility enables us to support projects across various industries, ensuring that we can handle any client requirement.
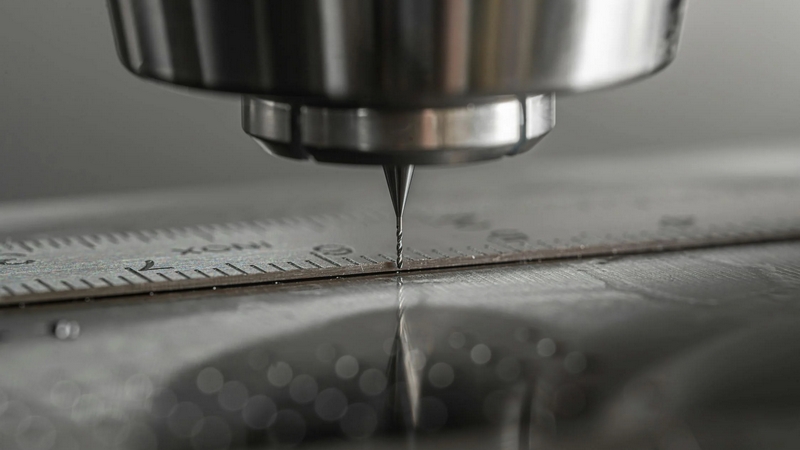
Our services are further enhanced by our innovative cloud-based platform that simplifies the entire manufacturing process. The platform allows clients to manage their projects from design through to production seamlessly, and the integration of the platform also reduces project costs and eliminates logistical challenges. The platform also enables fast time-to-market, allowing for designs to quickly move from concept to production.
In addition to our manufacturing capabilities and technology, we also pride ourselves on our expertise and guidance. Our team of specialists assists clients in selecting the most suitable materials, designing efficient and robust molds, and choosing the appropriate production techniques. This ensures that every part we manufacture meets the highest standards of quality and functionality, whether it’s durable plastics for outdoor equipment or high-grade metals for mechanical components.
At Ponoko, quality and customer satisfaction are paramount to everything we do. We implement rigorous quality control measures at every stage of the manufacturing process to ensure that all products meet our high standards. This commitment to quality helps in minimizing defects and ensuring the longevity of products, and our customer service team is dedicated to resolving any issues promptly, ensuring a positive experience for all clients.
By partnering with Ponoko, engineers gain access to a global network of top-tier manufacturing professionals and state-of-the-art facilities. Our extensive network ensures that we have the capabilities to handle projects of all sizes, from small custom jobs to large-scale production runs, and the advanced technology and skilled workforce in our facilities guarantee precision and care in every project, regardless of its complexity or location.