
Overview of Injection Molding
Injection molding stands out as a precise and efficient manufacturing technique, predominantly utilized for shaping plastics. Its ability to rapidly produce complex shapes with high precision makes it a preferred choice in various sectors, including automotive, electronics, consumer goods, and medical industries. The ability to produce high-volume quantities of parts also makes it an economical choice for mass production, with the cost per unit decreasing significantly as the production volume increases. However, the high initial cost of molds can make injection molding less cost-effective for small production runs.
The process of injection molding involves injecting molten plastic into a pre-designed mold cavity under high pressure. This ensures that the plastic takes the shape of the mold, and the high pressure also helps to remove any air bubbles that may be trapped in the molten plastic. As the plastic cools and solidifies, it becomes impossible to remove the mold from the plastic part without using extreme force, which itself can be difficult to do due to the high strength of plastic.
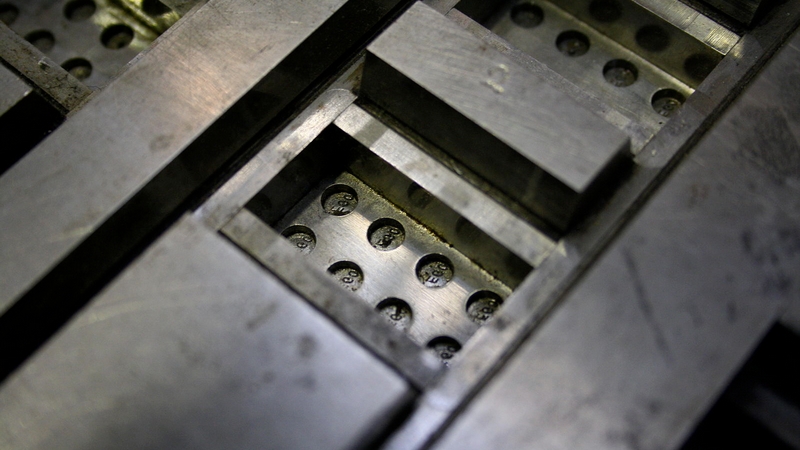
The tight tolerances and precise control offered by injection molding make it ideal for creating parts that require great precision, such as automotive components. The high strength and durability of plastic parts also make injection molded parts ideal for use in consumer goods that are subject to frequent use and/or stress, such as luggage and containers.
The ability to create complex shapes and designs also makes injection molding ideal for use in industries such as medical, where the high degree of precision and accuracy is essential for components used in medical equipment and implants. The ability to create low-cost prototypes also enables engineers to test and refine designs before committing to large-scale production runs, thereby reducing the financial risks associated with design errors.
Parts And Components Of An Injection Mold
The injection mold is an intricate assembly that plays a pivotal role in the manufacturing process of parts via molten material injection into a shaped cavity. Each component of the mold, including the mold base, core, cavity, ejector pins, plates, runner system, and cooling channels, is engineered to perfection to ensure the quality and precision of the final product.
The mold base, typically made from steel or aluminum, provides a robust foundation that supports all other parts and maintains alignment and spacing during the injection process. Its robustness is also essential to handle the high pressures of injection molding without warping or bending.
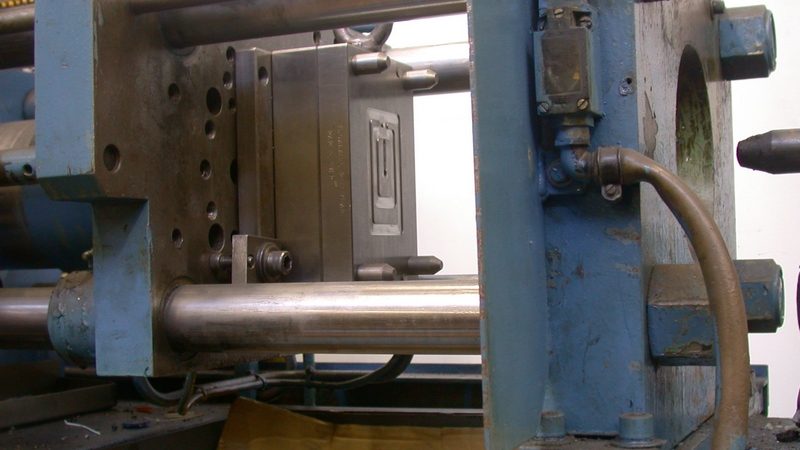
However, it is the core and cavity that are the mold’s most crucial components, defining the shape of the final product. The core shapes the inner surfaces of the part, while the cavity shapes the outer surfaces. For example, in the production of a plastic bottle, the cavity would form the external shape of the bottle, and the core would shape the inside. These components are precision-engineered from hardened steel to withstand repeated thermal cycles and ensure the accuracy of each part produced.
Ejector pins and plates are vital for part ejection after solidification. Once the material has cooled and solidified, these pins and plates activate to remove the part from the mold without causing damage. This mechanism facilitates rapid and safe part removal, enabling the mold to be quickly reused, which is essential for mass production.
The runner system guides molten material from the injection machine into the various cavities of the mold, ensuring even flow and minimizing waste. A well-designed runner system reduces the risk of defects such as air pockets and ensures complete and uniform material distribution.
Cooling channels are integrated throughout the mold to regulate temperature during injection and cooling. These channels allow coolant to circulate around the mold, removing heat and solidifying the material faster. Effective cooling is essential as it directly impacts cycle time and product quality; uneven cooling can lead to warping or residual stresses in the molded part.
All these components must be manufactured with precision to ensure the success of the injection mold. The harsh conditions of the injection molding process require materials and parts that can withstand high pressures and temperatures.
How to Maintain the Parts of an Injection Molding Machine
Maintenance of injection molding machines is essential for ensuring the overall efficiency and quality of production as these machines are complex and expensive. The upkeep of such machines is necessary for both the quality of the products being produced and the longevity of the machines themselves. Proper maintenance helps prevent unexpected downtime and costly repairs, ensuring that the production line runs smoothly and efficiently.
One of the key aspects of maintaining an injection molding machine is regularly cleaning the mold and its components. Over time, material residues from plastic can accumulate on mold surfaces, leading to defects in the molded parts including poor surface finish and inaccurate dimensions. Such parts will not meet the required specifications, and this can result in rework as well as revenue loss. Thus, regular cleaning helps remove these residues and maintain the precision of the mold, thereby ensuring each part produced meets the needed standards.
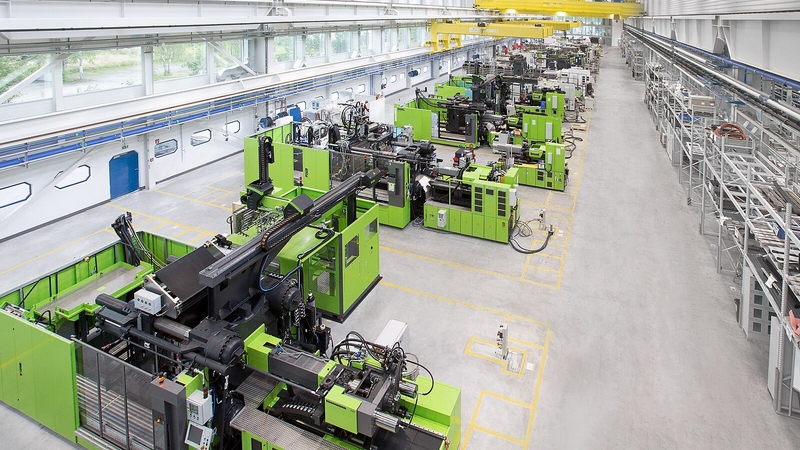
Another critical maintenance step is lubricating moving parts including ejector pins and plates. These moving components subject to constant motion experience friction and wear which can reduce the lifespan of these parts. Proper lubrication reduces this friction, minimizes wear, and ensures the smooth operation of these parts, thereby enhancing the machine’s efficiency and extending the life of these parts.
Regular inspections of the mold are also vital as the mold is subjected to extreme conditions including high pressure and temperature. These conditions can lead to wear and tear such as cracks, erosion, or deformation, and such signs of wear need to be identified before significant damage is done. Timely repairs prevent the deterioration of part quality and avoid the high costs associated with replacing a severely damaged mold.
The hydraulic and electrical systems of the machine are equally important and require regular checks and calibration. These systems control the machine’s operations including clamping force and injection pressure, and these need to be precisely controlled to maintain consistent cycle times and part quality. Checking these systems ensures that they are functioning within the set parameters, and calibration may be needed to adjust the machine back to its optimal performance levels.
Finally, creating a routine maintenance schedule is crucial as this schedule should include all tasks needed to keep the machine in top working condition from daily cleaning to complex checks and calibrations. A well-planned maintenance schedule helps identify potential issues before they escalate into major problems, thereby reducing downtime and costs associated with repairs. Early detection of issues also helps ensure that parts do not require rework, thereby reducing revenue loss.
Key Takeaways
The efficiency of injection molding makes it a highly preferred manufacturing technique for large-scale production of intricate parts. The ability to produce complex shapes with high repeatability makes injection molding essential in various industries, including automotive and consumer electronics, where components need to fit together precisely and be produced in millions with minimal variation.
Understanding the different components of an injection mold is vital to achieve such high standards as any flaw in the mold can result in variations in the final product. Each part of the mold requires precise design and craftsmanship to ensure that the final product meets the required specifications, including material type, strength, flexibility, and intricacies such as ribs, bosses, and undercuts.
The machine used to inject molten material into molds also requires regular maintenance to ensure that it operates efficiently and produces high-quality parts. Maintenance tasks include cleaning to remove residual material, lubrication to ensure smooth operation of moving parts, and thorough inspections to identify potential issues before they lead to machine failure. Such maintenance practices are crucial for preserving machine life, preventing costly downtime, and ensuring the machine continues to yield high-quality parts over its lifespan.
The injection molding process also requires careful material selection and consideration of design elements to optimize its performance. The choice of material affects the properties of the final part, including its durability, flexibility, and resistance to heat and chemicals. For instance, thermoplastics like polyethylene and polypropylene are popular for their versatility and recyclability, making them suitable for a wide range of applications. Design elements such as wall thickness also need to be carefully considered as it can affect the strength and durability of the final part.
Why Choose Ponoko
Ponoko offers customers a unique experience, differentiating itself from other manufacturing companies by offering a wide range of services that cater to both startups and large enterprises. One of our key services is precision injection molding which is essential for producing complex and detailed parts with high repeatability and is particularly beneficial for companies looking to scale up their production without compromising on the intricacies of their designs.
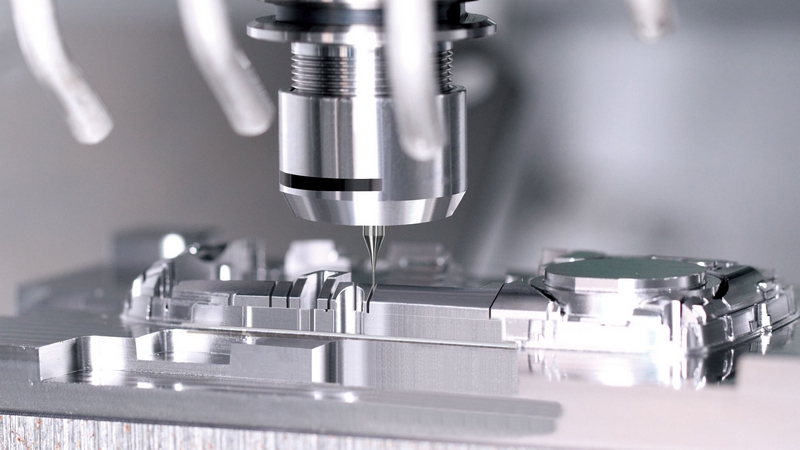
The integration of a cloud-based manufacturing platform revolutionizes how businesses approach production by simplifying the process from initial design to final delivery and enables engineers and product developers to bring their projects to fruition. The platform also enhances collaboration among team members by allowing for real-time updates and adjustments, ensuring that every stage of production is aligned with the client’s specifications and timelines.
Our expertise in design for manufacturing (DFM) and quality assurance further enhances our services by ensuring that products are designed with manufacturability in mind, reducing the need for prototypes and revisions. By focusing on quality assurance, we guarantee that each product meets stringent standards before it reaches the client, thereby minimizing the risk of errors and ensuring client satisfaction.
Our commitment to maintaining high-quality standards and ensuring customer satisfaction has given us a reputation as a reliable partner in the manufacturing sector, with clients trusting us to deliver superior products that adhere to the highest industry standards. Whether a company needs a small batch of products for testing and validation or large-scale production to meet market demand, we have the capabilities to handle it with precision and efficiency, making them an ideal partner for businesses at various stages of growth.