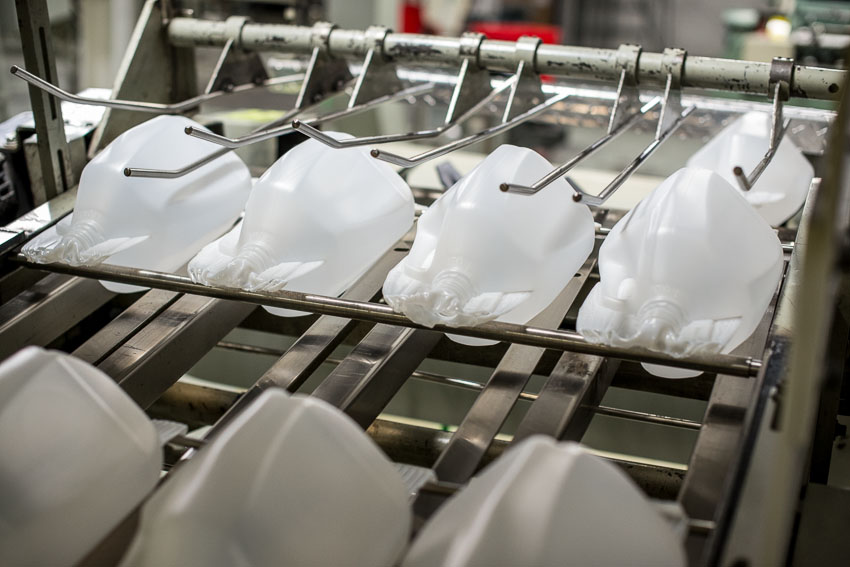
Thermoforming process
Thermoforming is a manufacturing process that has significantly altered the production landscape on a global scale as it is used in various industries. To start, thermoforming begins by heating a plastic sheet to a malleable state where it can be manipulated over a mold. This mold is carefully designed to match the desired shape of the final product and ensures that the plastic sheet conforms to the mold as it cools down. The cooling process causes the plastic to harden and take on the shape of the mold.
The thermoforming process is advantageous when manufacturing large, thin-walled plastic parts in large quantities. However, thermoforming is also ideal for prototyping as it allows for rapid production and testing of prototypes. Furthermore, the ability to produce both low and high volumes makes thermoforming an attractive manufacturing option.
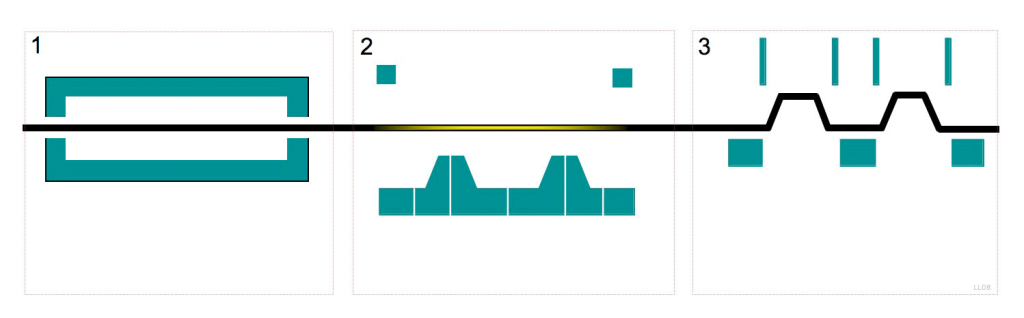
There are two main methods of thermoforming; vacuum forming and pressure forming. Vacuum forming is the simpler of the two methods and involves a mold that is surrounded by a vacuum seal. As the plastic is heated, it expands and tries to get to the outside of the mold. Since there is no air pressure around the mold, the plastic quickly cools and hardens in the shape of the mold.
Pressure forming, however, uses an air source that is connected to the mold so that when the plastic is heated and expanded, the air pressure forces the plastic into the mold. This method is advantageous as it can be used to create more intricate designs with better surface finishes.
The ability to choose from a wide range of plastics also makes thermoforming ideal for various applications. The clarity, rigidity, and impact resistance of plastics can be tailored to meet specific needs, and the ability to incorporate varying levels of detail and texture allows for the creation of customized parts.
The cost-effectiveness of thermoforming also plays a crucial role as molds used in thermoforming are less expensive compared to those used in other plastic forming processes such as injection molding. The ability to produce both low and high volumes of parts makes thermoforming an attractive manufacturing option that is cost-effective.
What is Injection Molding?
Injection molding is a prevalent manufacturing technique that has revolutionized the production of solid plastic parts and is equally adept at handling both low and high-volume production runs which makes it an indispensable technique in various industries. The process begins by injecting molten plastic into a mold that has been precisely machined to meet the specific requirements of the desired part and the molds used in injection molding are designed to ensure that the finished products adhere to tight tolerances and possess superior surface finishes.
The versatility of injection molding is one of its most significant advantages and the technical process of injection molding involves several critical steps including plastic pellets being heated to a molten state and then injected into a mold under high pressure ensuring that the plastic fills all cavities and intricate details. Once injected, the mold is cooled using water or air jets and this cooling stage is also crucial as it allows the plastic to solidify into the final shape of the part.

After the mold has cooled and the part has solidified, the mold is opened and the part is ejected. This marks the completion of the production cycle and the part is now ready for use or further processing such as painting or assembly. The efficiency of this process means that products can be turned from raw materials into finished goods rapidly, significantly reducing production times and increasing productivity.
One of the standout features of injection molding is its repeatability. This characteristic is crucial for industries that require uniformity across large volumes of products and injection molding ensures that each part is produced to the same specifications minimizing variability and defects. This level of consistency is difficult to achieve with other manufacturing processes making injection molding a preferred choice for many manufacturers seeking reliability and precision at scale.
Thermoforming vs. Injection Molding
Thermoforming and injection molding are two widely used manufacturing processes that cater to different applications and industries. Thermoforming is ideal for producing large, thin-walled parts and is commonly used for packaging, food trays, and large automotive panels. Its ability to efficiently manufacture large parts makes it a cost-effective solution for mass production, and the lack of intricate details or complex geometries also makes it suitable for volume production. However, thermoforming is limited in terms of part thickness and material control, meaning it is not suitable for parts requiring precision and accuracy.
Injection molding, on the other hand, is renowned for its ability to produce high-precision parts with intricate details and complex geometries. This makes it the preferred choice for industries such as healthcare and automotive where precision is crucial. The precision and accuracy of injection-molded parts come at the cost of higher tooling and production costs, but the ability to produce high-quality parts makes it a cost-effective solution for precision parts.
Another advantage of injection molding is the wide range of materials it can use, including plastics like polyethylene and polypropylene as well as advanced engineering plastics like polycarbonate and polyamide. The versatility of material selection enables manufacturers to tailor the properties of the molded part to specific requirements such as impact resistance, flexibility, and thermal stability.
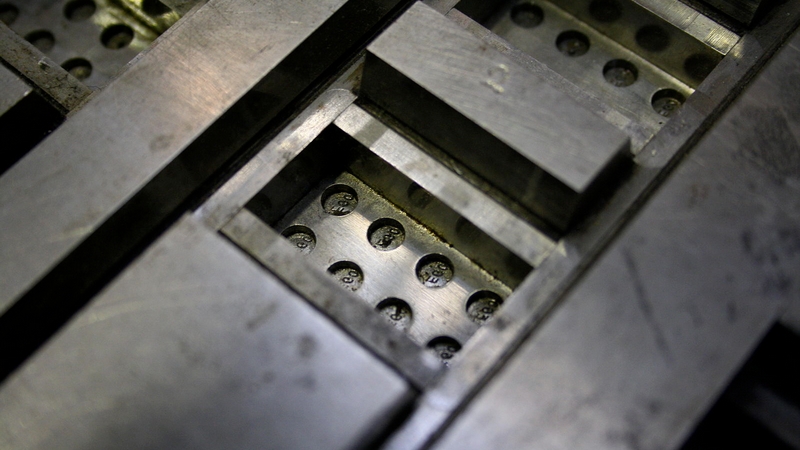
While injection molding offers greater precision and accuracy, thermoforming offers faster lead times and lower tooling costs. This makes thermoforming an ideal choice for prototyping and small-scale production runs, especially for those with budget constraints. The quick turnaround time and cost-effectiveness of thermoforming enable companies to rapidly prototype new products without investing in tooling and setup.
Thus, the choice between thermoforming and injection molding depends on the part design, production volume, material requirements, and cost considerations. Engineers should evaluate these factors to determine which process is best suited for their application.
Pros & Cons of Thermoforming
Thermoforming presents a cost-effective and fast manufacturing option compared to injection molding, making it a suitable choice for producing large, thin-walled parts. The simplicity of the thermoforming process also enables quicker setup and production start times, ideal for products that lack intricate details such as refrigerator liners and automotive door panels. The ability to produce low to medium volumes with minimal tooling costs makes thermoforming an economical option for small businesses and custom products, and the wide range of plastic materials and textures available can enhance the functionality and appearance of the final product. Furthermore, the molds used in thermoforming can be adjusted easily, allowing for last-minute design changes and customization.
However, thermoforming is less suitable for parts requiring precision and detail due to the inherent limitations of the process. The inability to create complex geometries and thin walls also reduces the strength and durability of thermoformed parts, limiting their application. Additionally, the need for secondary processes such as trimming and machining increases the production time and cost, reducing the cost-effectiveness of thermoforming.
Thermoforming also suffers from a lack of uniformity and control over part thickness, leading to inconsistencies in the finished parts. While this may be acceptable for some applications, it can be a drawback for products requiring precision and consistency. Overall, thermoforming is an economical option for mass production of large parts with basic features, but its limitations make it unsuitable for precision-crafted parts requiring complex designs, small tolerances, and high-precision manufacturing.
Pros & Cons of Injection Molding
One of the significant disadvantages of injection molding is its high initial cost, primarily due to the need for molds, which can cost tens of thousands of dollars. However, once a mold has been produced, the cost per part is relatively low, making it economical for large production runs.
Another disadvantage of injection molding is the long lead time associated with designing and producing molds. This can be a critical factor for industries where time-to-market is essential, as any delays can result in missed opportunities or revenue losses.
Injection molding is also not ideal for producing very large, thin-walled parts without special considerations. The cooling process can lead to warping or defects, requiring additional tooling adjustments or design alterations to mitigate these effects. Material waste is another concern in injection molding, primarily due to runners, sprues, and flash that occur during the process. While some of this waste can be recycled, it still represents an added cost and environmental impact.
A major challenge with molds is that they are extremely expensive to produce and can take a long time to design and fabricate. This means engineering teams need to carefully plan and consider all aspects of a part before committing to a mold. The high cost of molds also means that design iterations can be expensive. This is particularly problematic in industries where design cycles are already challenging, such as medical devices. As a result, it is essential that prototypes are as close to the final product as possible to minimize the number of iterations in the design process.
The high cost of injection molding also makes it challenging for startups and small businesses to scale their production. The initial investment required in molds and machine time means that parts can only be ordered in large quantities, leading to substantial upfront costs.
However, it is possible to use injection molding with smaller initial orders by utilizing shared molds with other companies. This approach reduces the initial cost of the mold, and the use of a shared mold decreases machine time, thereby making the process more economical.
Real World Applications for Both
Thermoforming and injection molding are two dominant manufacturing processes utilized across various industries due to their versatility and efficiency. Thermoforming heats a plastic sheet until it becomes pliable, then molds it to a specific shape using a mold and trimming the formed parts to create a finished product. This method is advantageous for producing large parts with relatively simpler designs and is widely used for packaging materials. Blister packs protect products from moisture and contamination while providing a clear view of the product, and clamshells offer a secure yet easily accessible packaging solution. Trays are also tailored for various uses, including food serving and electronic component handling during manufacturing processes.
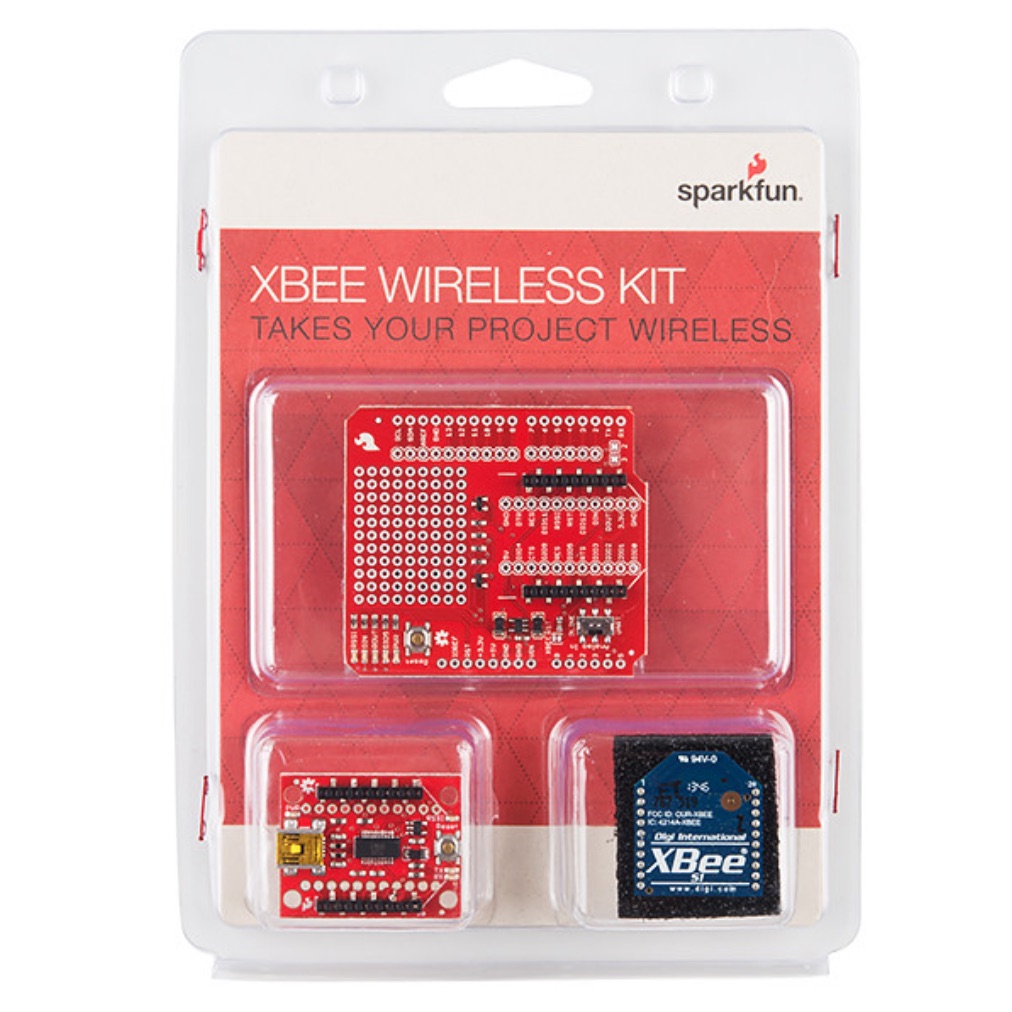
The automotive industry chooses thermoforming for manufacturing large, durable components such as door panels, dashboards, and interior trim. These parts require a robust material that can withstand wear and tear while providing aesthetic value to the vehicle’s interior. The medical field benefits from thermoforming for creating sturdy, lightweight enclosures for medical devices, instrument trays, and protective covers that are easy to sterilize and handle. Consumer products like food containers and appliance housings are also produced using thermoforming, allowing for quick customization and adaptation to market trends. Sporting goods and industrial components like machine guards, pallets, and large storage bins utilize thermoforming to achieve cost-effective production of sturdy and functional items.
Injection molding, on the other hand, involves injecting molten plastic into a mold cavity where it cools and solidifies into a precise shape. This process is ideal for producing high volumes of complex parts with tight tolerances and fine details. Electronic housings, such as those for smartphones, remote controls, and computers, are produced through injection molding due to the need for precision to accommodate specific technical and electronic requirements while providing protection and user-friendly interfaces. Automotive parts such as clips, fasteners, connectors, and intricate interior components are also frequently produced using injection molding, which enables complex shapes and high-strength materials. Medical devices, including syringes, inhalers, and diagnostic equipment housing, rely on injection molding for achieving high precision and consistency essential for medical applications. Consumer products like toys, kitchen utensils, and small household appliances benefit from injection molding’s ability to handle complex shapes and high-volume production.
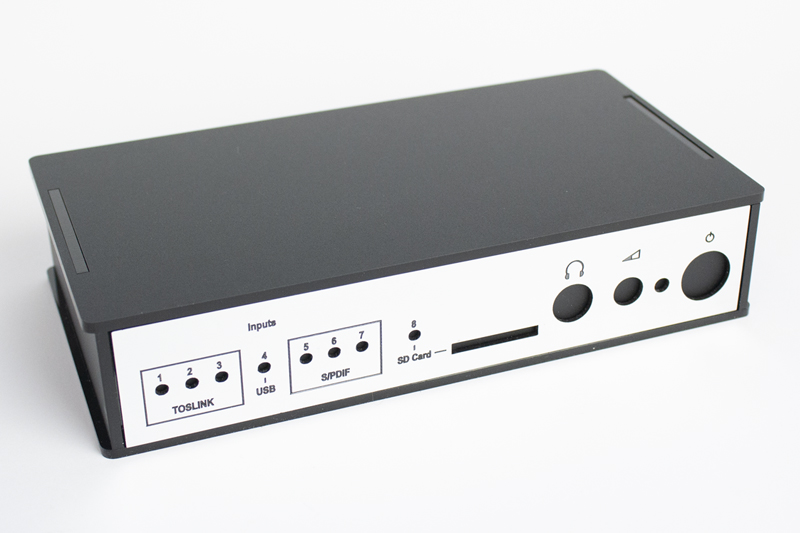
Key Takeaways
As the manufacturing industry continues to advance, two primary processes, thermoforming and injection molding, have emerged as essential components in the production of a wide range of items. Thermoforming is particularly advantageous when manufacturing large, thin-walled parts that are made from thermoplastics, such as petri dishes, lighting lenses, and storage containers. The ability of thermoforming to quickly and cost-effectively produce large parts makes it a suitable choice for low-volume production runs, including prototypes and small-scale production batches. However, thermoforming may not be as effective for manufacturing parts with intricate details or high-precision features, making it less suitable for parts requiring precision engineering.
On the other hand, injection molding is ideal for manufacturing small, complex parts that require extreme precision and accuracy, such as engine components, microfluidics, and medical devices. The high-speed and high-pressure nature of the injection molding process enables the production of high-quality parts at scale, making it a cost-effective solution for mass production. However, the high cost of injection molding equipment makes it less economical for small production volumes, and the need for molds limits design flexibility.
The choice between thermoforming and injection molding depends on a multitude of factors, including the material, the complexity of the part design, and the intended use of the finished product. For instance, parts that require precision engineering and high durability can benefit from injection molding, while parts that need to be produced at scale and are not heavily dependent on precision can take advantage of thermoforming.
The versatility of these two manufacturing processes extends beyond the scope of product complexity, with both processes capable of working with a wide range of materials. However, material selection is a critical factor to consider, as some materials may not be suitable for either process. For example, materials with high shrinkage rates can cause manufacturing errors during thermoforming, while materials with low melting points may not be suitable for injection molding due to the high temperatures involved.
In addition to the technical considerations, cost is also an essential factor in the selection of either thermoforming or injection molding. Thermoforming offers a cost-effective solution for low-volume production runs, making it an ideal choice for prototypes and initial production batches. However, the high cost of molds and machine equipment makes injection molding less economical for small production volumes, making it more suitable for large-scale manufacturing.
The future of these manufacturing processes will continue to shape the way products are designed and produced. As advancements in material science and technology improve, new materials with unique properties will emerge, opening up new opportunities for thermoforming and injection molding applications. The increasing focus on sustainability and environmental responsibility will also impact the way these processes are conducted, with a greater emphasis on recycling and waste reduction.
Why Choose Ponoko
At Ponoko, we stand out from other manufacturing companies by offering a broad range of services tailored to meet various project needs. We specialize in both thermoforming and injection molding—two essential techniques for creating parts and components used in numerous applications. For instance, thermoforming is perfect for producing large parts like panels and housings by heating a pliable plastic sheet over a mold. On the other hand, injection molding is ideal for high-volume production of parts with complex geometries. These manufacturing methods are crucial for clients who need versatile and robust solutions.
To ensure a smooth transition from design to production, we use a cloud-based platform that streamlines project management and communication. Our platform allows clients to upload their designs directly and track their projects from start to finish. This system helps us manage multiple projects efficiently while eliminating the logistical challenges associated with traditional manufacturing processes, thereby reducing project completion times.
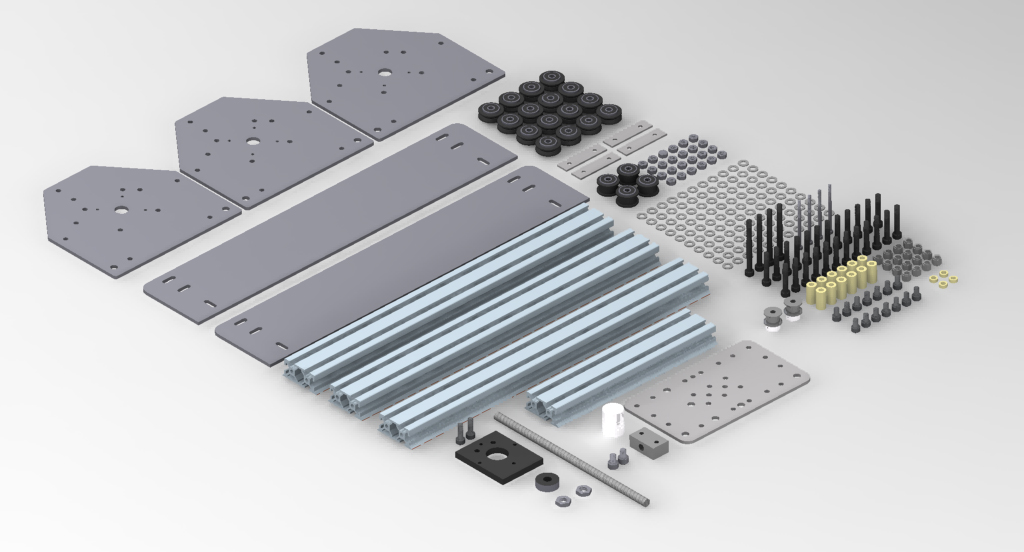
We also provide expert guidance throughout the entire manufacturing process, from material selection to mold design. Choosing the right material is vital as it greatly impacts the functionality and durability of the final product. Our expertise in material selection ensures that we select the best material for your project. Additionally, we assist with mold design, which is crucial for achieving precision and quality in parts produced through injection molding. Our production experts also advise on the most cost-effective manufacturing techniques to optimize the process and enhance the quality of the final product.
Quality, cost-effectiveness, and customer satisfaction are at the heart of what we do. We are committed to completing every project to the highest standards, regardless of size or industry. Our commitment to quality involves rigorous testing and quality control to guarantee the durability and performance of our manufactured parts. We achieve cost-effectiveness through efficient production practices and a well-optimized supply chain. Our dedication to customer satisfaction means we strive to meet the unique needs and expectations of each client, building strong, ongoing partnerships.
Working with us means gaining access to a global network of manufacturing professionals and state-of-the-art facilities. Our experts bring extensive experience to every project, and our facilities are equipped with the latest technologies and machinery necessary for high precision and quality. This combination of professional expertise and advanced facilities allows us to produce high-quality parts at scale, making us an ideal partner for both prototype and production runs.
Understanding thermoforming
- What is thermoforming, and what are its advantages?
- Thermoforming involves heating a plastic sheet until it’s pliable and then forming it over a mold using vacuum, pressure, or mechanical force. This method is particularly advantageous for producing large parts like vehicle door panels, refrigerator liners, and trays. It is also cost-effective for smaller production runs since molds can be made from less expensive materials like wood or epoxy.
- What is injection molding, and what are its benefits?
- Injection molding involves melting plastic pellets and injecting the molten plastic under pressure into a mold. This process is highly efficient for creating complex and intricate designs with great precision, making it ideal for products such as plastic gears, electronic housings, and bottle caps. It is preferred for high-volume production because the molds, typically made from hard metals like steel and aluminum, offer a longer lifespan and can withstand the pressures and temperatures involved.
- How do I determine which process is more suitable for my project?
- The suitability of thermoforming or injection molding depends on several factors including the complexity of the design, required material properties, production volume, and budget. Injection molding is often better for detailed features and high-strength requirements, while thermoforming may be more appropriate for larger, less complex items or when working with tighter budget constraints.
- What production capabilities does Ponoko offer?
- Ponoko is equipped to handle both large and small production runs, offering flexibility depending on your project’s scale. This adaptability allows clients to adjust their production based on demand without committing to large initial investments.
- What materials are supported by thermoforming and injection molding?
- Thermoforming commonly uses sheets of thermoplastic materials such as ABS, polycarbonate, and acrylic, known for their lightweight and impact resistance properties. Injection molding can utilize a broader range of plastics, including high-performance composites tailored for enhanced characteristics like heat resistance or rigidity.
- How does the lead time for creating molds differ between thermoforming and injection molding?
- Thermoforming molds are generally quicker and less costly to produce compared to injection molds. Injection molds require precision engineering and high-quality metal machining, which can take weeks to months to construct. This lead time can influence the decision between the two processes.
- How can Ponoko assist with thermoforming and injection molding projects?
- Ponoko provides design support and manufacturing expertise to help engineers create prototypes and manage production runs of any size. Our services ensure that projects meet specific requirements and are executed efficiently.