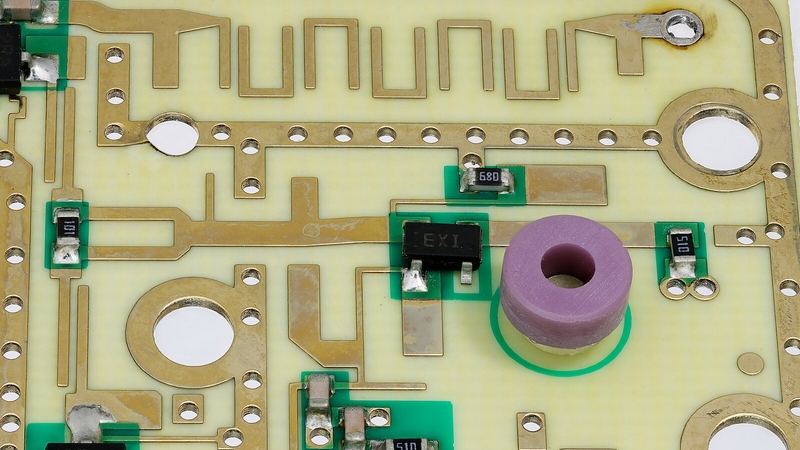
What is a PCB?
The printed circuit board is the backbone of modern electronics, expertly connecting various components together through a complex network. Unlike traditional wiring using wires, PCBs enable components to be connected in a highly organized and compact manner, allowing for complex circuits to be reduced in size. The design of a PCB is no small feat, involving a pattern of copper pathways etched onto a non-conductive substrate that guides electricity through the board to and from components in a controlled manner.
While PCBs can be as simple as a two-layered board with all components on one side, they can also be as complex as 40+ layers, with most advanced devices falling in the 4-10 layer range. The use of multiple layers allows for highly interconnected circuits while preventing electromagnetic interference (EMI) between different circuits.
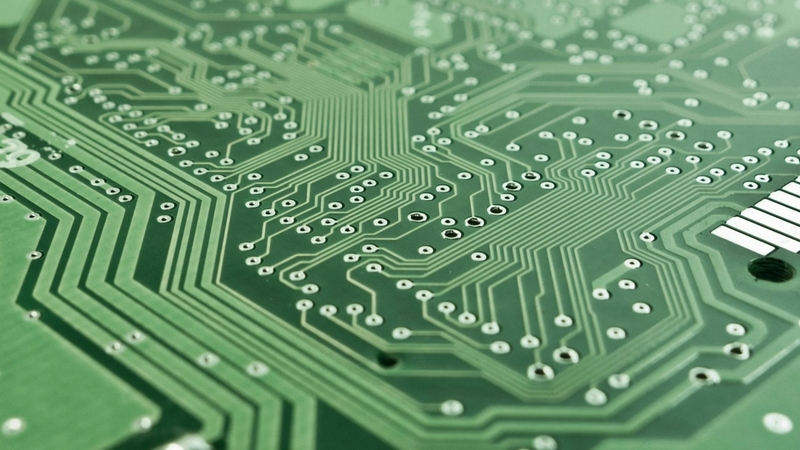
The precision and accuracy of PCBs is achieved through the use of computer-aided design (CAD) software that allows engineers to test and refine their designs before they are manufactured. Once a design is ready, PCB manufacturing involves copper etching to create traces, soldering to connect components to the board, and applying solder masks to prevent accidental shorting of traces. Additional surface treatments can also be applied to improve solderability and protect the board from environmental factors.
Recent advancements in PCB technology have also seen the development of flexible PCBs, which pave the way for flexible and foldable electronics. As such, these advancements have opened up new possibilities for product design, enabling the creation of wearable technology and smart devices that can be folded and carried with ease.
Differences Between Standard & Advanced PCB
The complexity of a PCB cannot be determined by a basic inspection, as PCBs can range from simple prototypes to advanced technologies needed for high-performance applications. Basic PCBs with a few common components are often sufficient for standard electronic devices and consumer products where technical demands are modest, but PCBs with multiple layers and sophisticated components are essential for aerospace, military, and high-speed computing devices. The complexity of a PCB depends on the perspective of the observer, and what may seem complex to one individual may be considered basic by another with similar expertise.
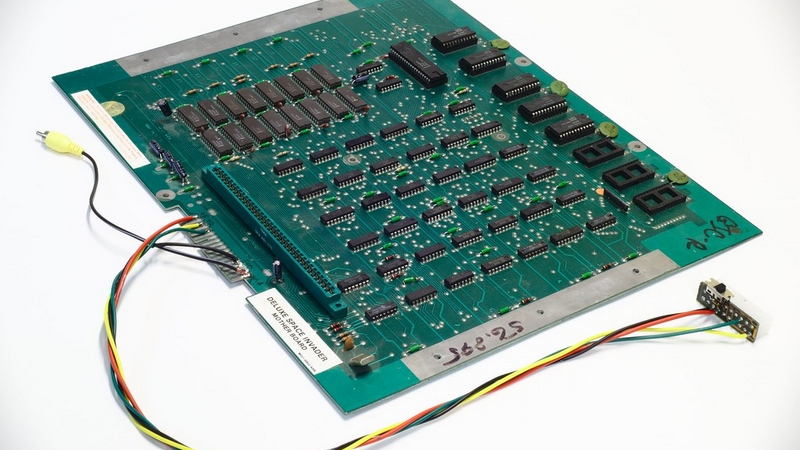
PCBs with more than four layers are generally considered advanced as they provide more routing space for electrical signals and are essential for high-speed circuits. The use of components such as Ball Grid Arrays (BGAs) and flip chips also indicates complexity as these components are typically used in high-density applications where space is limited. The precise placement and soldering of such components adds to the manufacturing complexity, and the high-precision engineering required means that such PCBs are not suitable for prototyping.
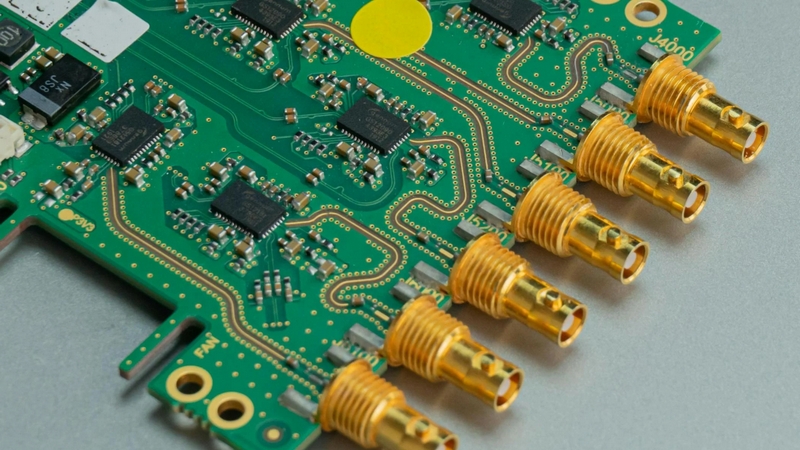
The material used in a PCB can also indicate its level of sophistication with ceramic PCBs being used for their high thermal conductivity and low expansion rates, and heavy copper PCBs for their ability to handle significant power loads. The high-performance capabilities of advanced PCBs make them essential for technologies such as data centers and high-speed computing, and the precision engineering involved in their manufacture means that they are not suitable for basic prototyping stages.
Breaking Down Advanced Circuits
Advanced circuits represent the pinnacle of electronics, warranting their use in applications where precision, efficiency, and reliability are paramount. The complexity of these circuits stems from the need to manage high-speed operations, maintain signal integrity, and distribute power effectively, rendering standard components and manufacturing processes unsuitable for their construction.
A prime example of advanced circuits is a computer’s motherboard, which connects all the system’s critical components, including the CPU, memory, and input/output devices. Although the motherboard itself is constructed from common materials such as flame-retardant fiberglass laminate, the components it supports, such as DDR memory and chipsets, necessitate meticulous control over timing, impedances, and power distribution networks. The importance of such control is evident from the fact that even minor discrepancies can lead to performance degradation or system failures.
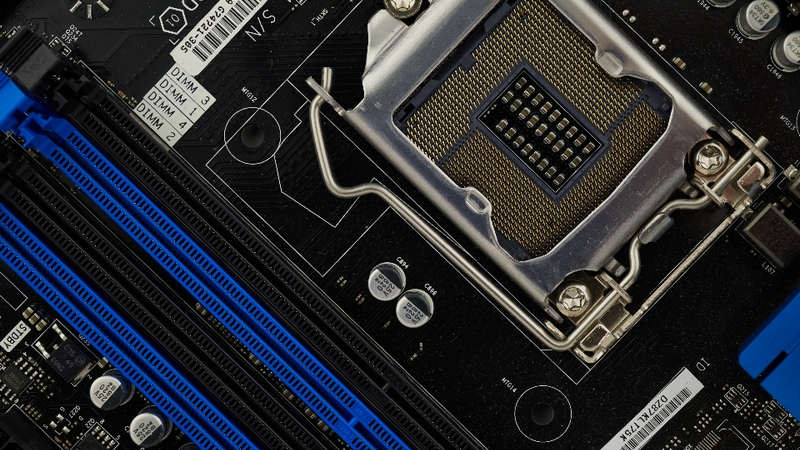
However, advanced circuits are not exclusive to computing applications; they are also essential in radio frequency (RF) applications and high-speed signal environments. These applications often require materials beyond those typically found in PCBs, including ceramic, which is critical for RF circuits to control impedance. Impedance control is essential to ensure signal integrity, as poor impedance can result in signal reflection and loss, which is crucial for maintaining the strength of the signal.
The performance of an antenna, which is paramount for effective communication in wireless devices, relies on the properties of transmission lines. These lines must have a controlled dielectric constant and a carefully engineered metal layer to ensure optimal antenna performance. Standard PCB materials are often insufficient to meet these stringent requirements, leading to the use of advanced materials and techniques in the design and manufacture of antennas.
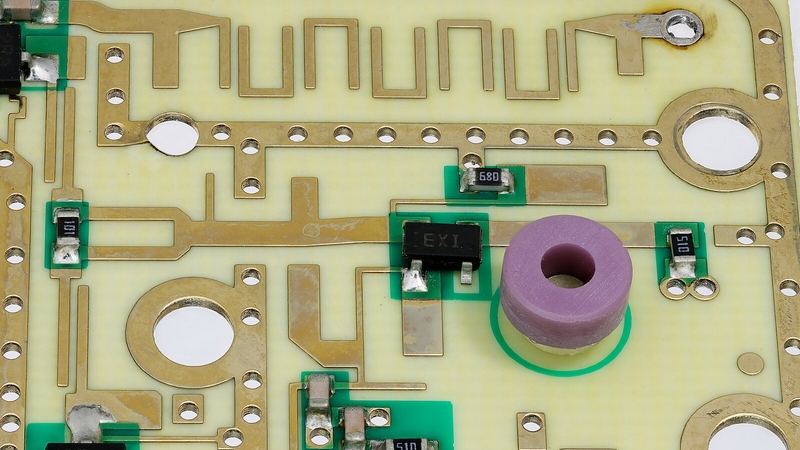
The reliance on advanced circuits in various applications underscores the need for a deep understanding of the underlying principles and technologies that support their design and manufacture. The challenges involved in creating advanced circuits highlight the importance of expertise in materials science, signal integrity, and manufacturing processes to ensure the success of these complex electronic systems. As the demand for high-performance electronics continues to grow, the need for advanced circuits will also increase, driving innovation in the field of electronics engineering.
Advanced Circuit Materials
When designing electronic circuits, the focus often leans toward the active and passive components, such as resistors, capacitors, and integrated circuits, as well as the conductors that link these components. However, the substrate material, or dielectric, on which these components and conductors are mounted plays a critical role in the overall functionality and reliability of the circuit. The dielectric material separates conductive elements like copper traces, helping to prevent electrical shorts and providing mechanical support for the components mounted on it.
A high-quality dielectric is essential not just for insulation but also for controlling impedance levels between the copper traces and the ground planes. Impedance control is crucial in maintaining signal integrity, particularly in high-frequency applications. This control ensures that signals are transmitted with minimal loss and distortion, which is particularly important in sensitive circuits such as those used in communication devices and precision measuring instruments. Materials that offer precise control over impedance are particularly valuable in constructing circuits that need to operate reliably under stringent conditions.
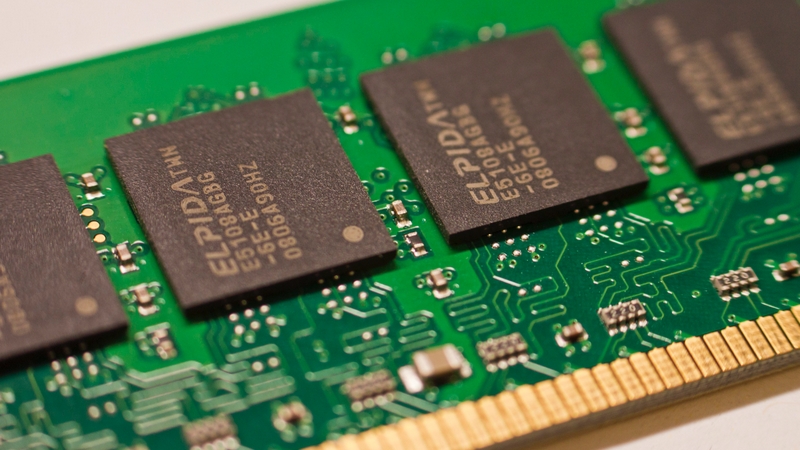
For example, in radio frequency (RF) circuits and high-speed digital systems, consistent dielectric properties ensure that performance remains stable across different units and operating conditions. FR4, a common material used in printed circuit boards (PCBs), is inexpensive and widely available. However, its dielectric properties can vary significantly from batch to batch, which can be problematic for applications requiring high precision and repeatability. This variability can make it challenging, if not impossible, to replicate performance in sensitive radio circuits or high-speed digital signal processing systems where consistency is key.
In contrast, ceramic-based materials, with their crystalline structure, offer much more consistent dielectric properties. This precision makes them ideal for use in high-frequency radio systems, where even minor deviations in dielectric constant can lead to significant performance issues. The uniformity of ceramic materials helps in achieving the desired impedance levels consistently across multiple PCBs, thereby ensuring reliable operation of the circuits.
Another interesting option in PCB materials is Teflon and other polymer-based substrates. These materials are not only flexible but also maintain good dielectric properties, making them suitable for applications where the circuit may need to bend or flex during use. This flexibility opens up new design possibilities for wearable electronics and other innovative applications where traditional rigid PCBs would not be feasible.
Beyond the dielectric material itself, the surface plating of the PCB also significantly impacts its performance. Different types of plating can affect everything from solderability to corrosion resistance. Gold plating, for example, while expensive, offers excellent solderability and is highly malleable, making it easy to plate over and create high-density point contacts. The high melting point of gold also makes it suitable for use in high-temperature environments. On the other hand, nickel plating provides excellent corrosion resistance and is cost-effective, making it ideal for PCBs destined for commercial products.
The ability to customize the plating also allows engineers to tailor their PCBs to specific requirements, whether it’s to improve reliability, enhance performance, or reduce costs. The plating of PCBs also plays a critical role in the manufacturing process. Engineers must ensure that the plating process does not damage the dielectric material, as this can lead to electrical shorts or other performance issues. The plating process itself can also impact the final characteristics of the PCB, such as the uniformity of the dielectric properties. Engineers must carefully select plating services that not only provide high-quality results but also offer reliable manufacturing practices.
Industries Covered by Advanced Circuits
The need for advanced circuits in modern electronics is evident across various industries, including consumer electronics, industrial, aerospace, military, and medical. In the area of consumer electronics, advanced circuits are essential for processing large amounts of data quickly and efficiently, enabling users to run complex applications smoothly on computers and other high-speed digital equipment. In radio systems, advanced circuits are crucial for managing signals and frequencies accurately, resulting in clear communication and high-quality audio.
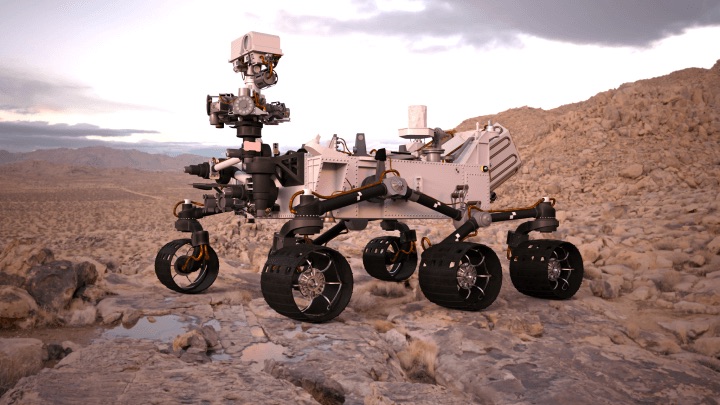
The industrial sector has also adopted advanced circuits to improve operations and enhance reliability in factories and plants. These circuits are designed to withstand harsh environments and ensure seamless performance under extreme conditions, leading to efficient and continuous industrial processes. However, the aerospace industry places additional stringent requirements on circuits due to the unique conditions encountered during flight, including variations in pressure, temperature, and vibration. Advanced PCBs in aerospace applications must be able to operate flawlessly in these conditions while providing reliable communication and navigation systems.
The military sector has extremely high standards for electronic components, demanding the highest level of reliability and precision. Military systems operate in unpredictable environments and require electronics that are durable and consistent in their performance. Advanced circuits used in military applications must be designed to be predictable and repeatable, ensuring reliable operation without failure. This is particularly crucial for equipment such as communication devices and weaponry systems, where malfunctions can have serious consequences.
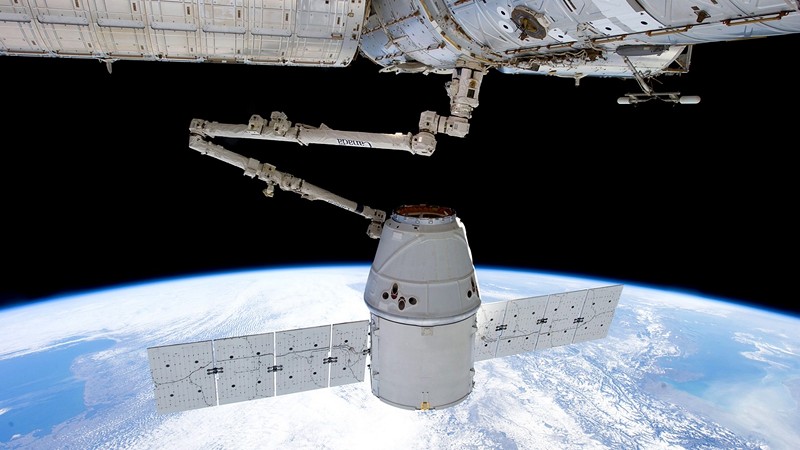
The medical field relies on the dependability of electronic devices, especially in life-supporting equipment such as pacemakers. Advanced circuits in medical devices ensure high precision and reliability, adhering to strict safety standards. The continuous operation of such devices without failure is essential, as any malfunction could have fatal consequences. Thus, the role of advanced circuits in modern industries is crucial, ensuring that devices and systems meet high performance and reliability standards across various sectors, including consumer electronics, industrial automation, aerospace, military, and medical.
Key Takeaways
The field of advanced circuits represents the pinnacle of electronic engineering, characterized by the incorporation of cutting-edge components and features that enable the creation of miniaturized devices capable of high-speed operations. The precision and versatility of these circuits make them essential for various industries, including medical implants, smartphones, and computing systems, where they enhance data processing efficiency and support for high-frequency applications. The integration of flexibility, transparency, and biodegradability in some advanced circuits expands the possibilities for wearable technology and environmentally friendly electronics, paving the way for innovative solutions that improve device performance and reduce environmental impact.
The selection of materials for PCBs is crucial for achieving the high electrical and mechanical performance required for advanced circuits. Traditional materials like FR4, a fiberglass-reinforced epoxy laminate, are unsuitable for complex designs, particularly in high-frequency applications such as radio systems due to limitations in dielectric constant and loss. To overcome these challenges, engineers turn to advanced materials with improved electrical properties and stability, such as high-frequency laminates and ceramic-filled composites. These materials enhance signal integrity and ensure reliable operation in high-speed and RF environments, making them essential for cutting-edge electronics.
The impact of advanced electronics is far-reaching, influencing industries globally. In healthcare, they improve diagnostic capabilities and patient outcomes with the use of wearable health monitors and advanced medical equipment. In the automotive sector, they enable the development of autonomous driving technologies and sophisticated in-vehicle infotainment systems, enhancing driver safety and convenience. Even in agriculture, advanced electronics support precision farming techniques, boosting crop yields and reducing waste through sensors and automated systems. The widespread adoption of these technologies underscores their vital role in driving progress across various industries.
The continuous advancement in electronic circuit design is the backbone of technological progress, enabling the creation of more powerful, efficient, and versatile electronic devices. As industries evolve and new challenges emerge, the importance of advanced electronics will expand, further integrating into the fabric of modern society. The integration of these technologies into everyday life will continue to improve the efficiency, performance, and sustainability of electronic devices, shaping the future of technology and driving innovation.
Why Choose Ponoko for PCBs
The process of manufacturing advanced printed circuit boards (PCBs) is a meticulous and complex one, influenced by numerous factors that can significantly impact the final product. Each step in the manufacturing process, from material selection to etching, must be carefully controlled to ensure the integrity and functionality of the board, and even minor variations in temperature or humidity can lead to defects.
In applications such as aerospace, medical devices, and automotive, it is essential that PCBs meet the highest standards of quality to ensure reliability and longevity. The failure of a single component in such applications can have serious repercussions, making it crucial to choose components and circuit boards that can be relied upon.
Our company has a proven track record of manufacturing precision parts, with a precision part rate of 99.7% across 2 million parts. This precision is achieved through rigorous quality control processes, state-of-the-art manufacturing technology, and the expertise of our skilled technicians, and this level of precision is also possible to extend to other products and services that we offer.
In addition to PCBs, we also offer a range of other services and products, including enclosures, labels, fittings, and packaging. By combining all these capabilities into a single manufacturing partner, engineers can simplify their supply chain and reduce logistical complexities.
The ability to rapidly prototype precision designs is also critical in today’s fast-paced market environments, allowing engineers to iterate and refine their designs quickly. This rapid prototyping enables engineers to accelerate product development and deployment, which is essential in industries where technology evolves rapidly, providing a competitive edge.
Thus, our unique combination of high-quality manufacturing capabilities, comprehensive services, and rapid prototyping enables engineers to push the boundaries of what is possible, leading to breakthroughs that can redefine industries and deliver superior value to end-users. By partnering with us, engineers can tap into our expertise and experience to drive innovation and advance technology.
FAQs
- What types of advanced PCBs does Ponoko manufacture?
- Ponoko is a company that offers custom manufacturing solutions and is equipped to produce advanced PCBs. Such PCBs are essential for modern electronics and are characterized by their multiple layers, finer lines, and higher connection density. The ability to produce advanced PCBs is crucial for designers and engineers looking to prototype or produce electronics with intricate circuitry and is something that Ponoko is capable of.
- Can Ponoko produce multi-layer PCBs with components on both sides?
- Ponoko is able to produce multi-layer PCBs that are commonly found in complex electronic devices such as smartphones and medical equipment. These PCBs improve functionality and enhance signal integrity, something which is essential for high-performance electronics. However, the use of multiple layers also allows for the possibility of components on both sides of the PCB, something which Ponoko also offers. This is advantageous for compact designs that require a high density of components and is commonly found in consumer electronics and other space-sensitive applications.
- What dielectric options does Ponoko offer for PCBs?
- The dielectric used in a PCB is also critical as it supports the electrical integrity of the circuit by reducing signal loss and crosstalk between layers. As such, Ponoko offers a range of dielectric options that allow designers to select the most appropriate material for their application based on factors such as high-frequency operation and thermal management.
- How does Ponoko ensure impedance control in high-speed circuits?
- Impedance control is also another advanced feature that Ponoko supports. This is essential for maintaining signal integrity in high-speed circuits and involves careful design and manufacturing practices to ensure consistent impedance throughout a PCB. This is also essential for RF and high-speed digital applications and demonstrates Ponoko’s ability to produce advanced PCBs.