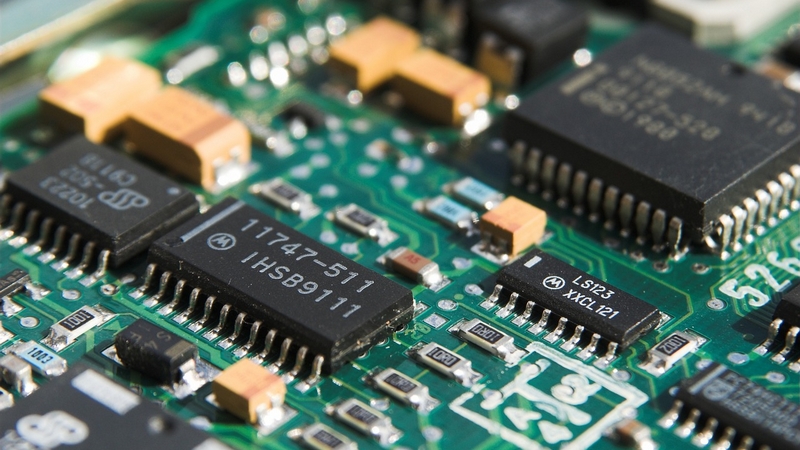
What is a PCB?
The development of Printed Circuit Boards, also known as PCBs, has revolutionized the world of electronics. These boards, which consist of copper traces on a non-conductive substrate, provide a compact and efficient way of connecting electronic components together. The use of PCBs instead of breadboards and stripboards enables for more complex designs as well as improved reliability, and this is why PCBs have become the standard in the electronics industry.
The manufacturing process of PCBs is remarkable in its own right. A photoresist is applied to a copper-coated board which is then exposed to a mask that shows the desired circuit pattern. This application of a mask enables for mass production with great precision and accuracy. Furthermore, the use of masks enables for high-speed production with consistent results between different batches. Such precision is essential in industries such as medical and aerospace where reliability is paramount.
The soldering stage of PCB assembly also requires great precision and skill as components need to be soldered to a PCB using a hot iron. However, the use of solder allows for a PCB to have its components mechanically secured to the PCB as well as electrically connecting all components together. Thus, a PCB with all components soldered in place is both reliable and dependable.
The use of pick-and-place machines in PCB assembly has greatly accelerated the production process. Such machines can quickly pick up components and place them on a PCB with great accuracy, and this saves time as well as reducing the skill required to assemble a PCB. This is especially advantageous in mass production where speed and efficiency are essential.
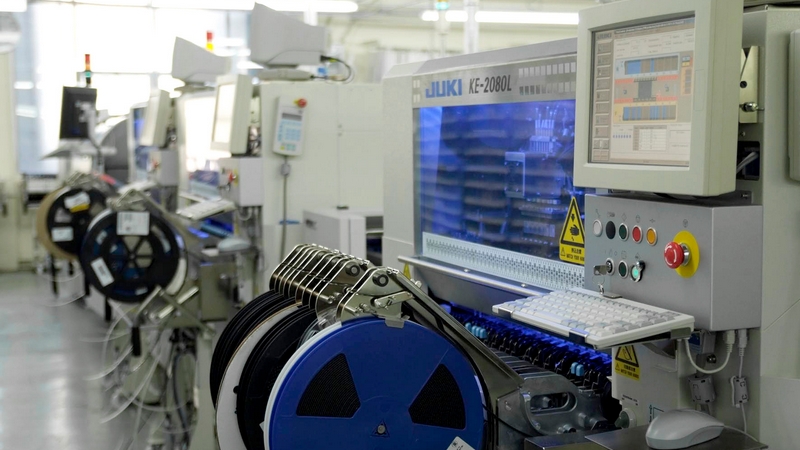
The importance of PCBs cannot be understated as they are found in almost all electronic devices. From everyday household appliances to large-scale industrial machinery, PCBs play a critical role in modern electronic devices and are responsible for the rapid expansion and evolution of technology. The ability to produce high-quality PCBs economically has enabled for advanced technologies to become accessible to the masses, and this has led to numerous technological advancements.
The role of PCBs in the field of electronics will only continue to grow as technology becomes more complex. The rapid pace of technological advancement will require the use of high-speed manufacturing techniques to keep up with demand, and the precision and accuracy offered by PCBs make them ideal for this role. Thus, PCBs are not only essential in the manufacture of electronic devices, but also in the use of advanced technologies that drive innovation and progress.
Types of Printed Circuit Boards
Printed circuit boards are fundamental components in modern electronic devices and each one is uniquely designed to fit a specific application while sharing common design elements with other PCBs. These boards are crafted to mechanically support and electrically connect electronic components using conductive pathways etched from copper sheets laminated onto a non-conductive substrate.
Single-sided PCBs represent the simplest type of circuit board and consist of only one layer of conductive material, typically copper. Their simplicity makes them inexpensive and quick to produce and as such are ideal for low-density designs such as power supplies and sensors. However, their inability to have more than one layer of copper restricts their ability to connect components together and as such are unable to handle complex designs.
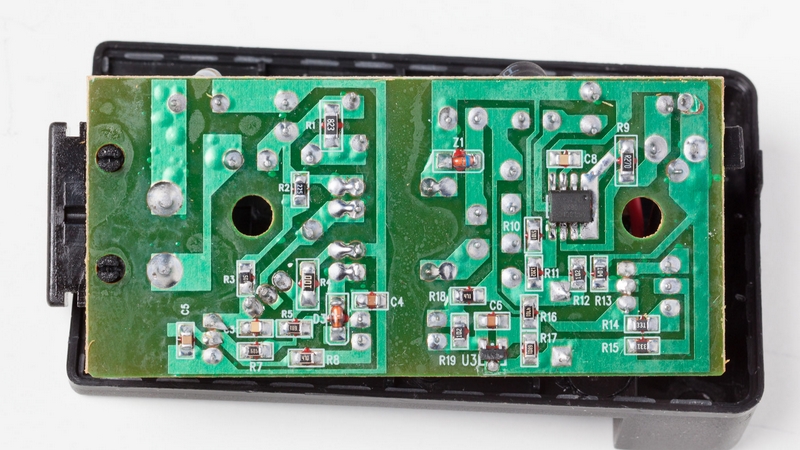
In contrast, double-sided PCBs offer greater flexibility in design with the use of vias that connect two different sides of the board. Components can be mounted on both sides of the board, and this setup allows for more complex circuits. However, double-sided PCBs can struggle with high-speed signals and as such are not ideal for advanced electronics.
For applications that require dense routing and high connectivity, multi-layer PCBs are preferred. These boards consist of three or more layers of conductive material, and this allows for highly complex and dense designs. Multi-layer PCBs are essential in high-end electronics such as computer motherboards, sophisticated industrial sensors, and smartphones, but their high layer count and complex manufacturing process make them expensive to produce.
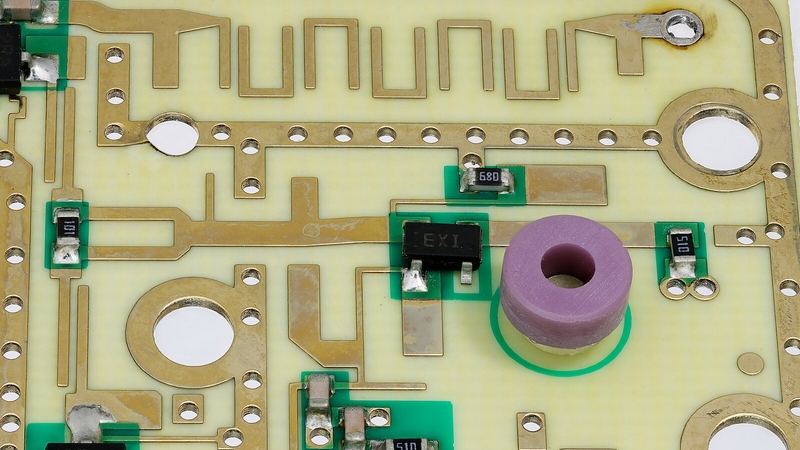
Another type of PCB is the flexible PCB that uses a flexible substrate that can conform to various shapes and flex during use. This is advantageous in portable electronics, such as foldable smartphones, and medical devices, but the use of special materials and manufacturing processes make them expensive and limited in their use.
Breaking Down The Basic Components
In electronics, components often come down to one of two specific categories; passive and active.
Passive devices, as the name suggests, lack the ability to amplify an electrical signal and solely consume or store energy. Common examples of passive components include resistors, capacitors, and inductors. While these components are not able to increase signal strength, they are vital for circuit functionality. Resistors regulate current flow and signal levels, capacitors filter and store energy, and inductors, along with capacitors, shape AC signals. Other passive elements, such as wires, connectors, and switches, facilitate connectivity and control within circuits.
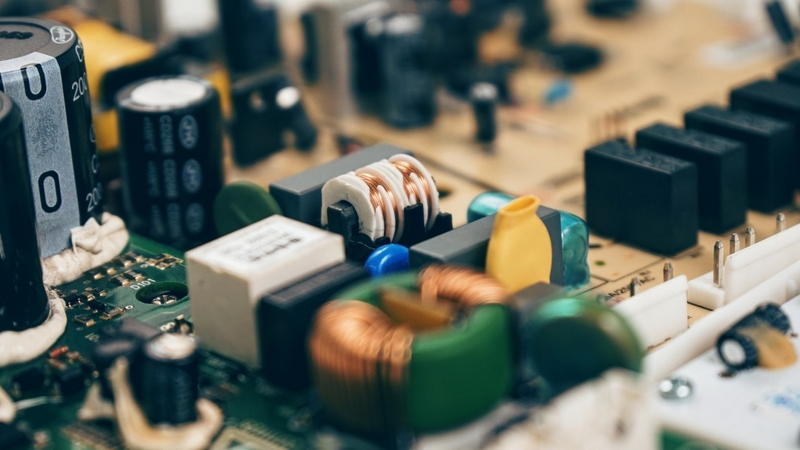
On the other hand, active components possess the capability to amplify and control electronic signals. Transistors, the cornerstone of modern electronics, act as switches for electrical signals, controlling current flow and enabling amplification. Power amplifiers, reliant on transistors, boost signal amplitudes to drive loads like speakers and motors, while integrated circuits, the backbone of electronic logic, process and convert signals.
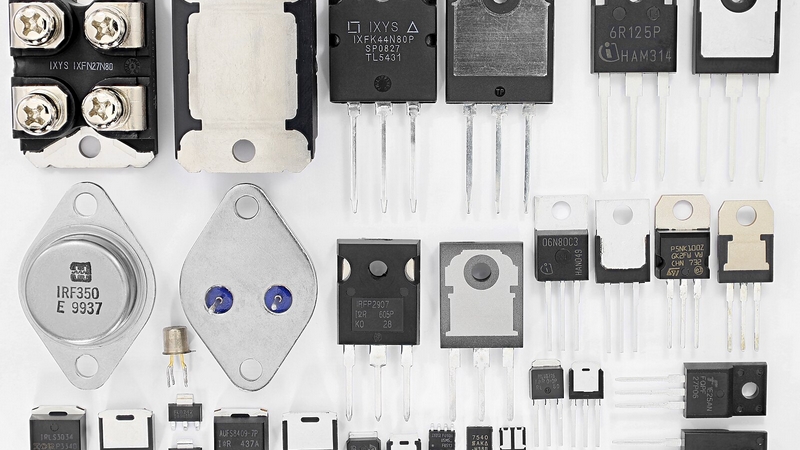
While connectors are classified as passive components, their significance in electronic devices warrants special attention. Connectors facilitate communication and connection between system components, essential for data transfer and system operation. For instance, USB connectors enable data exchange and power supply between devices, while barrel jacks are commonly used for power input. The proper selection and application of connectors are paramount; poor choices can lead to system malfunction or inoperability. Thus, understanding the requirements and compatibility of connectors in electronic designs is vital.
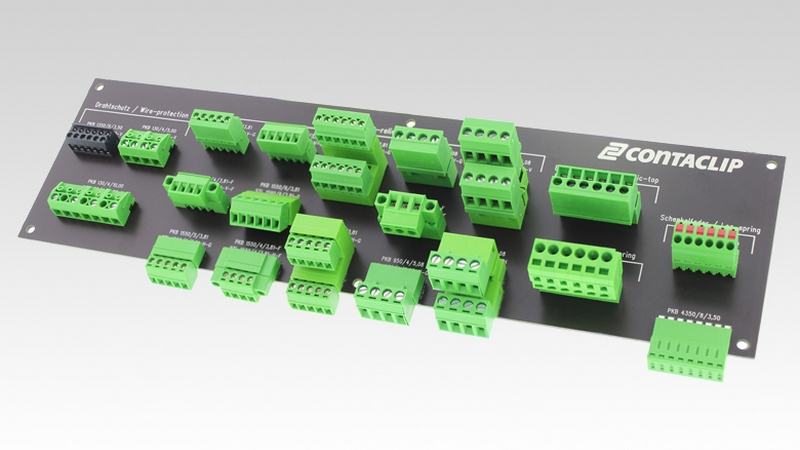
In essence, the distinction between passive and active components forms the foundation of electronics, guiding circuit design and assembly. Passive components manage energy flow and signal integrity without amplifying power, while active components play dynamic roles in signal processing and amplification, making them indispensable in digital and analog circuits.
Basic Electronic Component Part Numbers & Data Sheets
In the area of electronics design and manufacturing, choosing the right component is a daunting task due to the vast number of options available in the market. These options vary not only in their value, but also in aspects such as packaging, material composition, and operating temperature range, with some being suitable for high-temperature automotive applications while others are only suitable for standard room temperature office devices. Thus, correctly selecting components based on factors such as thermal stability, size, and tolerance is essential to ensure the performance and reliability of electronic devices.
Once the appropriate component is identified, obtaining its part number is also crucial as this number acts as a unique identifier for manufacturers and suppliers. This part number should then be meticulously recorded in both schematic diagrams and the Bill of Materials (BOM), which provides a comprehensive list of all components used in a project, including quantities, specifications, and part numbers essential for manufacturing and maintenance purposes.
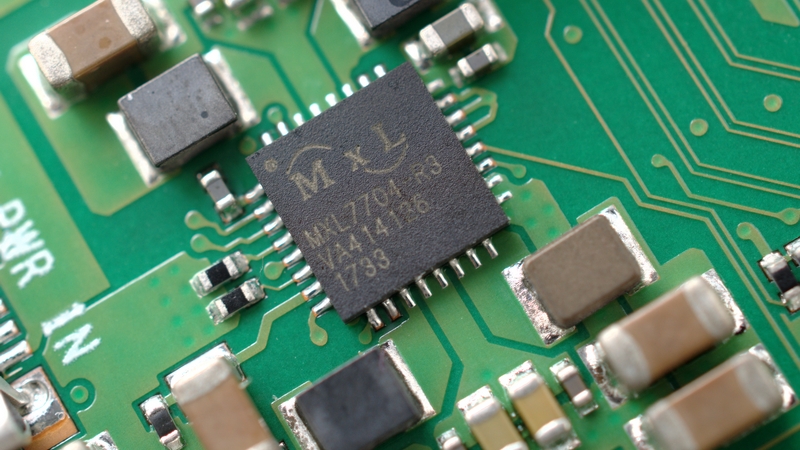
Each component is accompanied by a datasheet that provides engineers with in-depth information on the component, including its electrical, mechanical, and environmental characteristics. These datasheets are essential resources that reveal how a component behaves under various conditions and how it interacts with other components, such as whether a resistor may change its value with temperature fluctuations.
Some components have exceptionally stringent specifications due to their critical applications, such as aerospace and medical devices, which require components that meet strict reliability and safety standards. In these cases, datasheets are not only beneficial but essential for ensuring compliance with industry regulations and ensuring safety, as they detail every aspect of a component’s capabilities and limitations, including its capabilities and limitations.
As such, it is imperative for engineers to not only collect datasheets but also to spend time thoroughly reviewing them to prevent potential design flaws and operational failures by understanding every parameter and condition listed. This ensures that electronic devices operate as expected and meet their intended application requirements.
Key Takeaways
The printed circuit board, or PCB, is a marvel of engineering that has revolutionized the world of electronics. Its ability to replace bulky wires with thin copper layers that are etched to perfection allows for the creation of compact and efficient designs, while the use of non-conductive substrates provides a secure and durable base for components to mount on.
However, the success of a PCB depends on a multitude of factors, including the components used, the way those components are connected, and the environment in which the PCB will be used. For example, some components may require special mounting or alignment, while others may have specific voltage or current restrictions. Failure to take these considerations into account can result in the component failing catastrophically, either causing damage to the PCB or worse, posing a serious safety risk to those involved with the PCB.
The same applies to connectors, which are often overlooked in the design stage but play a critical role in the functionality of a PCB. Their ability to connect a PCB to external devices and power sources is essential for the PCB to be usable, and their durability and reliability are critical to ensure that they can withstand repeated use. A faulty connection can result in poor performance or even damage to expensive equipment, making it essential to choose connectors that are suitable for the application.
When it comes to components, it is also essential to choose parts that are suitable for the application, especially when it comes to critical systems such as safety and control. The use of generic parts that are available from many sources may seem like a cost-effective solution, but the inability to source a part can ground a production line, causing costly delays. In addition, using high-reliability parts can be critical in applications where reliability is paramount, such as in automotive systems.
The introduction of new technologies and the development of more advanced PCBs also presents engineers with a wide range of new opportunities and challenges. The increased complexity of PCBs, with their increased number of layers and smaller features, requires advanced manufacturing techniques to ensure high yields and good quality circuits. At the same time, the wider range of materials available to engineers also introduces new considerations in the design and manufacturing stages, such as environmental concerns and compatibility with future upgrades.
Why Choose Ponoko
At Ponoko, we understand the challenges engineers face when bringing their designs to life. The manufacturing process can quickly become overwhelming, especially when it comes to critical factors like the precise placement of components on a PCB. Misalignment or using low-quality components can lead to circuit malfunctions, poor performance, and reduced reliability of the final product.
Sourcing high-quality, legitimate components is another hurdle engineers often encounter. Using unauthorized parts can lead to intellectual property issues and further complicate the manufacturing process. While engineers have an intimate understanding of their designs, manufacturers may not always share the same level of insight, which can lead to miscommunications and even unintended alterations to the project.
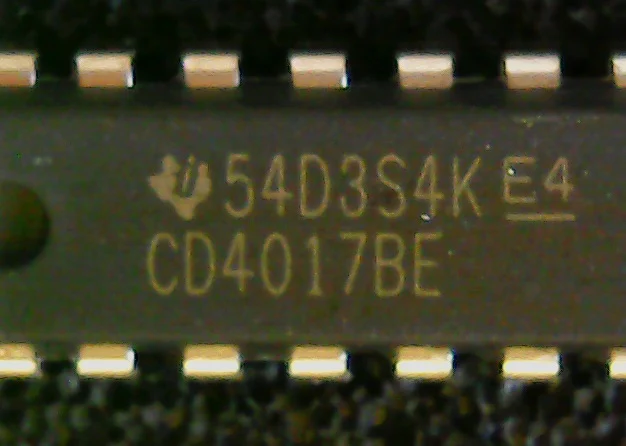
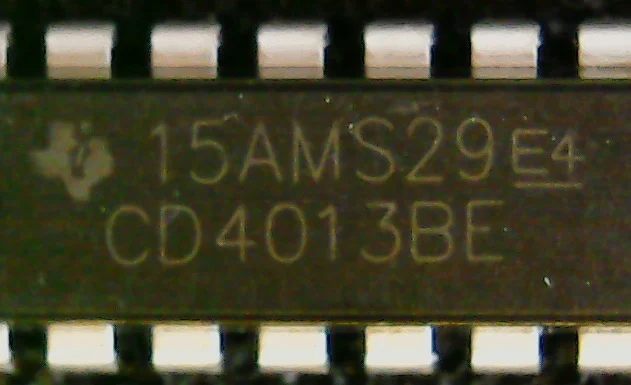
Recognizing these challenges, Ponoko has dedicated itself to simplifying the manufacturing process for engineers. We handle the technical aspects of production, allowing engineers to focus on their core expertise. By partnering with Ponoko, engineers gain access to our cutting-edge manufacturing techniques, ensuring that their designs are realized accurately and efficiently, accelerating project timelines.
Our rapid prototyping capabilities enable faster testing of designs, and with decades of experience, our team of skilled engineers can identify and address potential issues early in the process. This level of expertise not only guarantees that your designs are in capable hands but also eliminates the risk of intellectual property concerns.
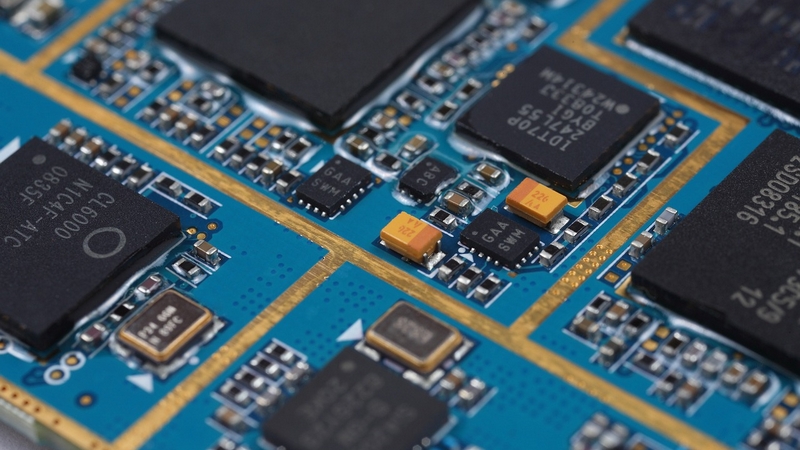
Ponoko’s commitment to quality and precision means that every design we manufacture is suitable for both prototyping and mass production. Engineers no longer need to source different manufacturers for various stages of a product’s life cycle. With Ponoko, you have a trusted partner from concept to reality, allowing you to focus on innovation and bringing groundbreaking products to market.
Learning more about PCBs
- What factors should be considered when choosing the type of PCB for a project?
- When deciding on the type of printed circuit board to use, several factors must be taken into consideration including the complexity of the circuit, its intended application, and cost constraints. For instance, a simple single-layer PCB might be suitable for basic electronic projects, whereas more advanced devices such as smartphones or computers require multi-layer PCBs to accommodate their intricate circuitry and higher functionality. The number of layers on a PCB depends on the number of interconnections needed between different parts of the circuit and the space available for the PCB.
- What is the difference between active and passive components on a PCB?
- Both active and passive components are essential for a PCB to function, and the difference between the two is that active components amplify electrical signals and control the operation of the circuit while passive components manage the flow of electricity, filter signals, and store energy. The choice between an active or passive component depends on the specific function and requirements of the circuit.
- How do surface mount technology (SMT) components differ from through-hole components?
- Surface mount technology components are directly mounted to the surface of the PCB and are favored for their compact size and suitability for automated assembly. Through-hole components have leads that are inserted into holes drilled into the PCB and then soldered, providing stronger mechanical bonds ideal for high-stress environments.
- What are the different soldering techniques used for SMT and through-hole components?
- SMT components can be soldered using reflow soldering where the entire board is heated to melt the solder, whereas through-hole components are often soldered using wave soldering or manual soldering techniques.
- Why is it important to understand the differences between SMT and through-hole technologies?
- Understanding the difference between SMT and through-hole technologies is essential as SMT components are smaller and allow for more compact, dense circuit designs compared to through-hole components which are larger and require additional manual labor to assemble. Each technology has its own advantages, and the choice between the two depends on the application and the required durability.
- How can engineers ensure the reliability and performance of components used in PCBs?
- Ensuring that components are from reputable sources is essential to ensure the reliability and performance of the PCB. Reputable suppliers guarantee component quality, adherence to industry standards, and often provide necessary support including ensuring components are not obsolete and compliant with regulations. Using substandard components can lead to circuit failures, affecting the overall product performance and safety.
- Why are unique identifiers necessary for components during the manufacturing process?
- Components require unique identifiers for identification during the manufacturing process and for future reference. Such identification can be achieved with the use of tags that are attached to the component packaging and then read by machinery during various production stages.
- What are the common PCB manufacturing processes and how do they differ?
- The most common process is the standard process which involves image photosensitivity coating on the PCB substrate, the application of a mask to expose areas where copper is needed, development of the mask to remove unexposed areas of the photosensitive layer, etching to remove unwanted copper, and then soldering the copper contacts. Alternative processes such as direct copper plating can be used for specific applications that require a more cost-effective solution.