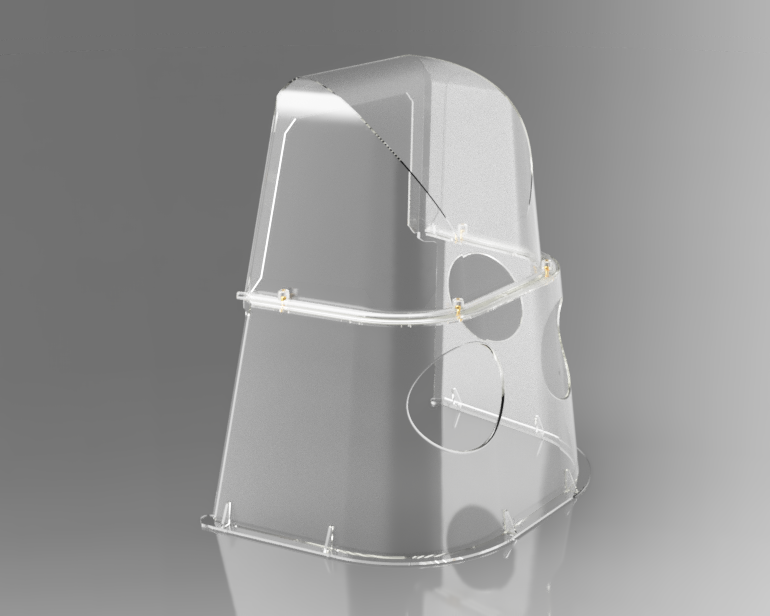
How Guidance Airway Solutions Finds Low-Complexity Solutions To Major Problems In Medicine
Since the coronavirus outbreak began in the spring of 2020, there’s been massive efforts taken to protect first responders and medical staff when caring for infected patients. In addition to N95 masks and face shields, intubation boxes are another form of PPE that has emerged in hopes of increasing safety for medical professionals.
Typically made from clear acrylic, these large cubes are placed over patients’ facial region to reduce exposure to airborne contaminants. There are two round arm holes in the box that allow medical professionals to access the patient for procedures.
While Dr. Joshua Herskovic, an anesthesiologist and co-founder of Guidance Airway Solutions, liked the idea of intubation boxes, he didn’t like what was currently available in the marketplace. “I look for low-complexity solutions to major problems in medicine,” he says. As such, he began searching for ways to improve upon the intubation box concept.
Intubating Infected Patients
Intubation, the placement of a breathing tube, is a common procedure conducted when patients are undergoing surgery or having trouble breathing on their own. A tube is put down the throat and into the windpipe to not only deliver oxygen to the lungs when breathing in but also to remove carbon dioxide as patients breathe out.
While intubation is generally considered low-risk, there can be dangers when intubating patients who have infectious conditions, such as COVID-19. This results in a number of issues:
Issue 1: Availability Of Negative Pressure Rooms
When dealing with infectious diseases, intubation is best done in a negative pressure room to protect not only the medical providers touching for the patient but also nearby staff. However, negative pressure rooms are of limited availability and do not exist in many care areas.
The complexity of the situation is compounded when infectious patients need surgery. Since operating rooms are positive pressure environments, the current practice is to intubate in a remote negative pressure room (if available) then transport patients to the OR. Negative pressure rooms are not always located near the OR, so this leads to increased exposure risk during transport.
The process is repeated for extubation (the removal of the breathing tube), so there is another opportunity for exposure risk during transport and potential issues again with the availability of negative pressure rooms.
Issue 2: Cleaning Of Negative Pressure Rooms
Cleaning operating rooms and negative pressure rooms can take up to three hours after infectious cases, making these facilities unavailable during this time. If the demand for intubation increases, there will be continued strain on keeping negative pressure rooms sanitized and ready for more patients.
Issue 3: Current Design Of Intubation Boxes
The common intubation box design uses flat sheets of acrylic, which are glued together at right angles to form a rectangle-shaped box. Glued joints can be fragile, so there is potential for the boxes to break apart at the joints if too much pressure is applied. Additionally, these designs tend to be bulky and heavy, oftentimes weighting 10 pounds or more depending on the thickness of acrylic used. Furthermore, because of their size and inability to be stacked, there can be storage issues when the boxes are not in use.
But the biggest issue with the current design is that the intubation box acts merely as a secondary shield and doesn’t mimic conditions of negative pressure rooms, which are essential to properly intubate infected patients.
Designing A Better Intubation Box
Prior to completing his medical degree from Wayne State University, Dr. Herskovic received his BS in Mechanical Engineering from Case Western Reserve University and worked in the medical device arena. His experience from the clinical side combined with an engineering mindset gives Dr. Herskovic a unique perspective: He knows what is needed medically and has the vision to see what can actually be achieved via manufacturing.
Working with his Guidance Airways Co-Founder Thomas Harter Sr., who is certified in multiple military aircraft, they came up with a simple, yet ingenious, solution to address the issues with current intubation boxes: A molded plastic shield combined with a laser-cut baffle that uses the hospital suction system to remove potentially infectious exhalation from near the patient’s head.
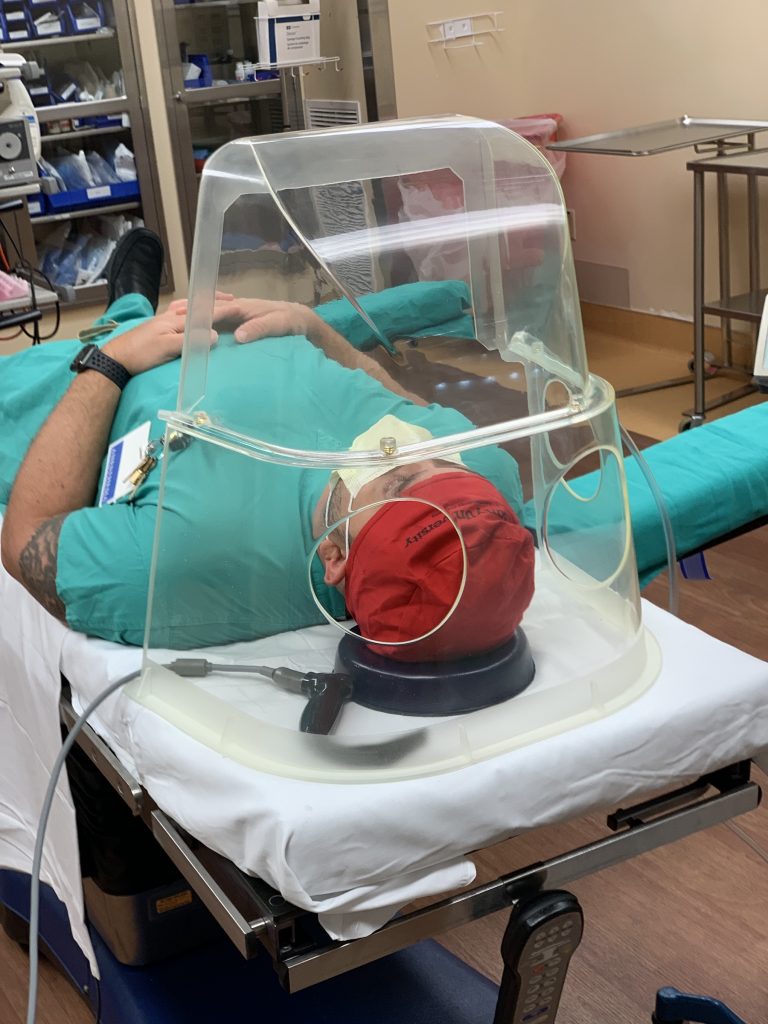
Solution 1: Portable Negative Pressure Air Curtain
The key to making the Guidance Negative Pressure Air Curtain work is the baffle, a “tube” that hooks to the suction system. “The baffle directs negative air flow around the patient’s head and was inspired by air curtains that direct air flow in military cockpits,” Dr. Herskovic explains. “The design creates a negative pressure air curtain around a patient’s head and runs off standard suction available in every room.”
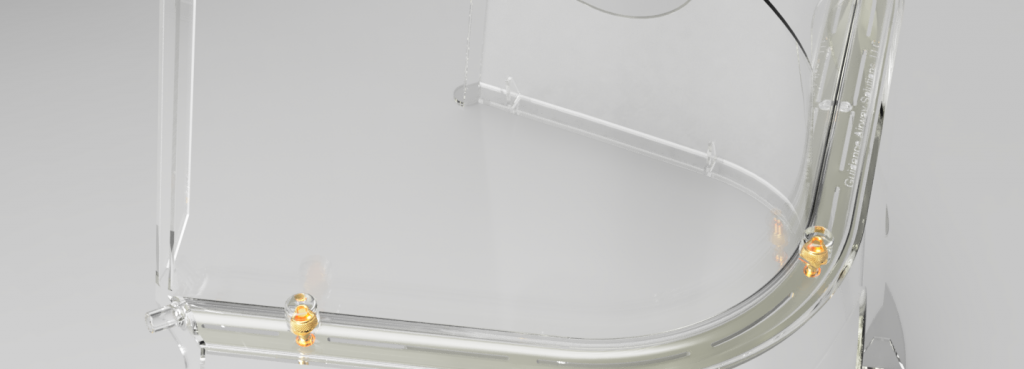
By creating a portable negative pressure air curtain, intubations can be conducted in any room that has suction capabilities, reducing the need for dedicated negative pressure rooms.
Dr. Herskovic notes that the device can be left in place for the duration of many procedures, which eliminates the need for transfers to and from negative pressure rooms, thus protecting all providers in and out of the OR. It’s also useful for non-intubated anesthesia cases (such as MAC sedation) as well.
Solution 2: Easy-To-Clean Design
The roundness of the Guidance design allows for easy cleaning; no corners or hard edges that are difficult to sanitize. Additionally, since the device is portable, patients don’t have to be moved from their initial treatment room to a negative pressure room, meaning only one room (plus the Air Curtain device) needs to be cleaned rather than two full rooms, saving a lot of time.
Solution 3: Ability To Mass Produce + Stackable Storage
Composed of lightweight, but strong, recyclable plastic, the Guidance Negative Pressure Air Curtain is less bulky than the traditional acrylic designs. “The shape is optimized to decrease bulk where it is not needed while the dome-like shape imparts strength to the design,” Dr. Herskovic says. “The shield is also molded from one piece, adding strength to the design. In addition to being tougher, our product is much lighter; it can easily be moved with one hand.”
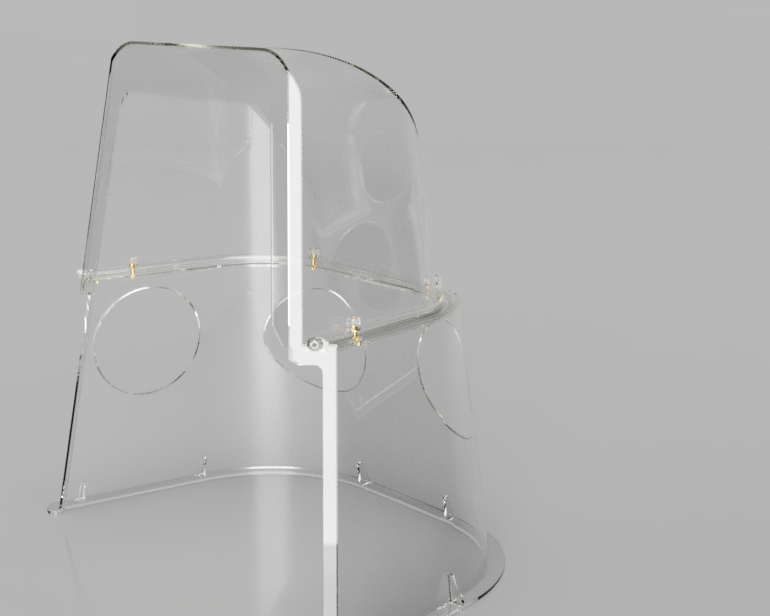
The simple design allows the Guidance Air Curtain to easily be mass produced, giving medical facilities the ability to have an appropriate stock of PPE if the need arises. And since the design is stackable, storing multiple units takes up minimal space.
Working With Ponoko
Most medical devices are made up of several components that use the best manufacturing method for each part. The Guidance Air Curtain is an excellent example of how molded elements can be combined with laser cut parts from Ponoko to create a cost-effective solution.
Dr. Herskovic designed the dome-like shield to be custom molded in one piece. Because the dome and single-piece design imparts strength, much thinner plastic could be used compared to typical intubation boxes.
Then he worked with Ponoko to laser cut the flat baffle that is made from clear acrylic for transparency and accuracy.
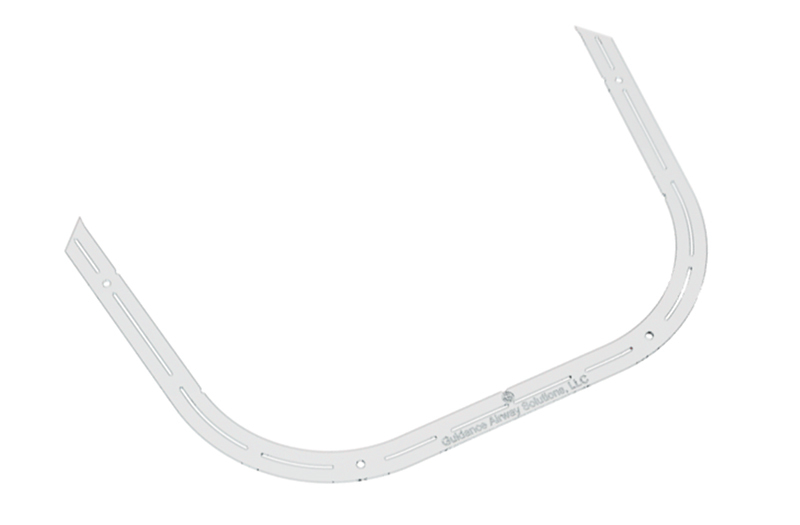
The molded pieces are combined with the laser cut parts to create the finished product.
“I considered 3D printing the baffle vs laser cutting,” Dr. Herskovic says. “But for a 2D object, laser cutting produces a more accurate model than 3D printing, especially when it comes to small holes [needed for assembly]. Additionally, laser cutting gives more predictable results.
“Ponoko also had the best interface and most options,” he continues. “You get an instant quote right away with any material you want, and the pricing is very good.”
Manufacturing On-Demand
Like any manufacturing process, you must iterate versions of the product to perfect the design. “Brainstorming multiple options is important to avoid falling in love with your first solution,” Dr. Herskovic says. “It’s also important to take critical feedback and truly consider the negative with any solution.”
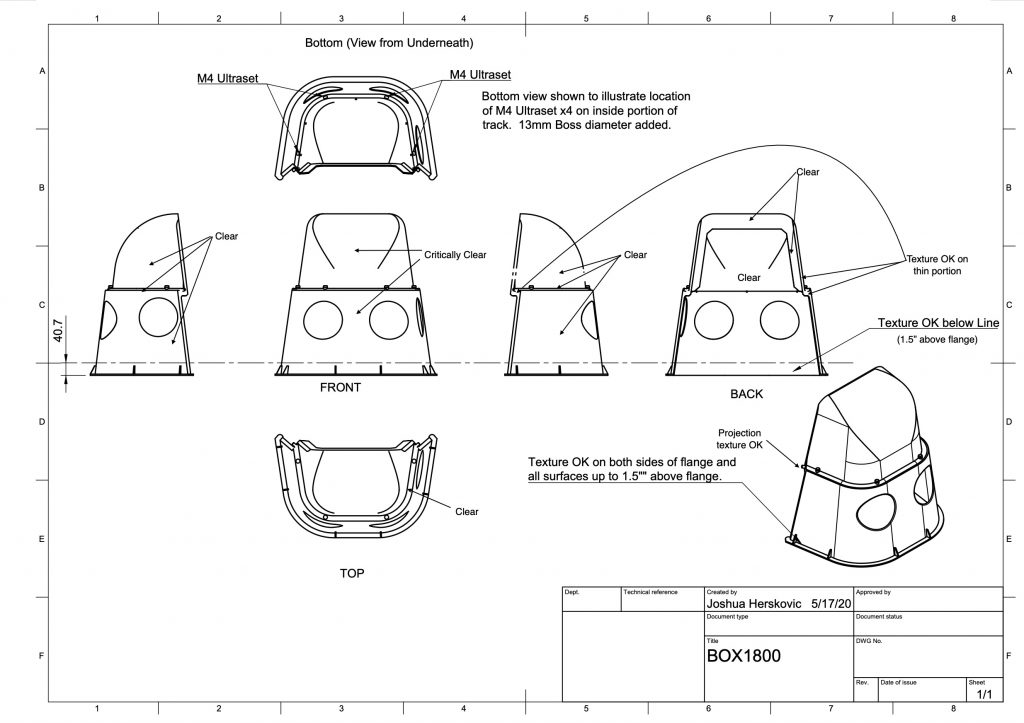
Good advice for bringing any kind of product to market. And Dr. Herskovic should know; the Guidance Air Curtain is the second device he has designed and manufactured.
“I’ve always been interested in medical innovation. However, the cost to develop a product from the ground up had previously been astronomical,” he explains. “Five years ago, I had the idea for another medical device (the FIRSTLOOK LTA) to help anesthesiologists. At the time, I had no idea how to bring this from sketch to product without breaking the bank. Luckily, new services were coming into place, allowing me to develop these ideas at much lower cost. I learned how to use Fusion 360 to generate designs. Companies such as Ponoko have dramatically taken the cost down in additive manufacturing (3D printing) and laser cutting. With this knowledge, I’ve also been able to help other surgeons take their ideas forward.”
Inspired by what Dr Herskovic built and want to make your own product? Here’s how:
1. Upload files to Ponoko to get an instant quote for making and shipping them to you today.
2. Make just 1—or 10,000!