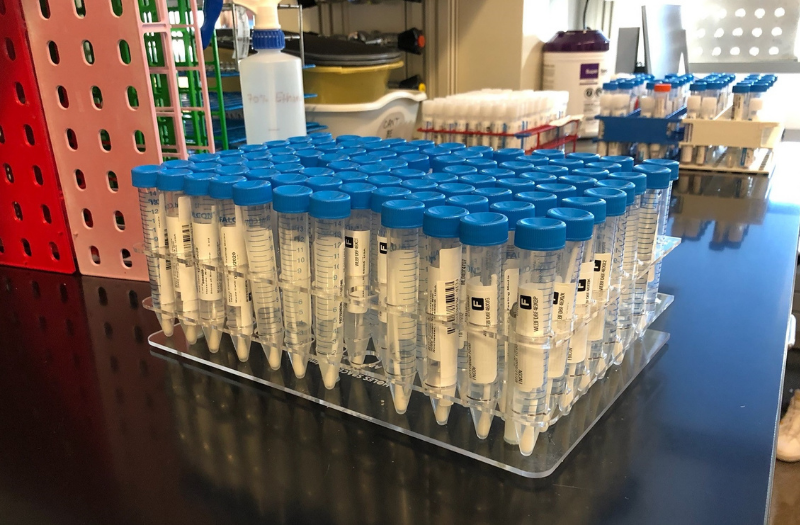
How A College Freshman Helped His Scientist Dad Go From Problem To Product In 28 Days
The spring of 2020 is one for the history books. But amid the sickness, lockdowns and economic downturn, there has actually been good news. Families are spending more time together, there’s immense gratitude for those on the frontlines and people are finding creative solutions to real-world problems.
Meet Aaron Beckman, a college freshman studying mechanical engineering at the University of Wisconsin-Madison, and his father Kenny, director of the University of Minnesota Genomics Center (UMGC).
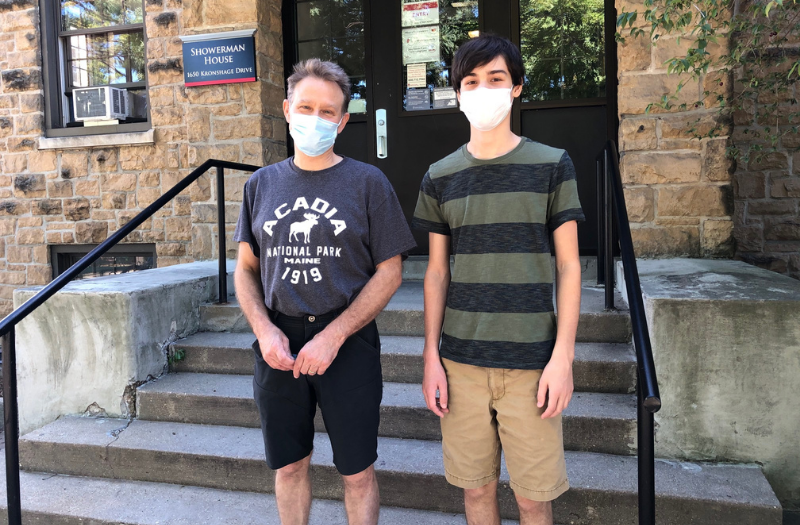
One night around the family dinner table, Kenny was sharing some of the struggles the labs under the UMN umbrella were having to not only complete the growing number of tests for coronavirus but also do additional retesting of samples when necessary. With the demand for testing growing exponentially, labs were experiencing a backlog—and there was a curious culprit.
Test tube racks.
While it may seem that test tube racks are relatively insignificant in the grand scheme of virus testing, they actually play an important role in the testing process.
Properly designed test tube racks save lab technicians time when setting up testing runs and facilitate a more streamlined testing process. They also help reduce confusion and the possibility of errors. Unfortunately, most test tube racks on the market aren’t properly designed.
What problems do the current test tube racks cause? Why aren’t proper test tube racks commercially available? What solution did Kenny and Aaron develop together? Read on to see how smart youth and super-smart wisdom came together to solve a real-world problem in COVID-19 testing labs.
Identifying The Issues
As director of the UMGC, Kenny supervises a 40-person, 8,000-square foot suite of labs that provide a wide array of DNA- and RNA-based genomics technologies for hundreds of researchers at the UMN and elsewhere. The Genomics Center is a part of a broader UMN effort that involves a number of other labs from the Medical School and the Fairview Hospital system (which is closely aligned to the Medical School under the “M Health” brand). Together, they provide testing for the state of Minnesota.
Like many labs across the country, the UMN facilities have pivoted to process COVID-19 tests. As of August, 2020, they have processed nearly 250,000 tests, with the highest number being 6,000+ in one day.
This is just through the UMN system. Across the U.S., thousands of labs are testing approximately 600,000 samples daily. But more is required. In fact, Kenny says there is a need for that testing to expand very dramatically—anywhere from 10- to 50-fold.
With the massive increase in demand, labs are being challenged to increase capacity and streamline efficiency while maintaining accuracy. One of the principal obstacles right now is backlogs. While there can be a number of reasons for backlogs (not enough personnel, machinery and space, for example), test tube racks are a surprising offender that compounds the issue.
Problem 1: Shortage Of Test Tube Racks
When specimens in test tubes arrive at a lab for analysis, they need a holding area. Hello test tube racks.
Because of the sheer numbers of COVID-19 tests to be processed, more test tube racks are needed. Just like there was a shortage of toilet paper at the beginning of the outbreak, there hasn’t been enough test tube racks in the supply chain to go around. If there’s nowhere to put incoming test tubes to prep for testing, the backlog begins.
Problem 2: Available Test Tube Rack Designs Don’t Align With Industry Standard
On the surface, it seems like any-ole test tube rack will do. Not the case.
Most mechanized lab testing machines are configured to analyze 96 specimens at a time. Thus, for maximum efficiency, the test tube rack should have the exact same format, i.e. 96 wells, as the testing machines. Unfortunately, this is not always the case.
“The standard layout for what is referred to as a ‘microtiter plate’ is an 8-row (A-H) by 12-column (01-12) array of wells in which biochemical reactions are carried out,” Kenny explains. “Almost all modern high-throughput biology research occurs in this 96-well format or its multiplex (384-well, 1536-well), using automation that can pipet liquids eight, 12, 16, or even 96 wells at a time.”
Processing specimens in 96-count increments is called a run. Being able to set up the test tubes in a run format allows them to integrate seamlessly with the testing machinery and is optimal to keep specimens organized.
To get an idea of what happens when test tube racks that have non-standard well configurations, check out this video from the Broad Institute in Boston that demonstrates what one has to do in the absence of 96-well racks.
“As you can see in the first minutes, the lab techs are taking 72-well racks (6×12), rotating them 90 degrees and then using two of them to get an ersatz 96-well layout,” Kenny says.
Clearly, test tube racks that don’t align with the 96-well testing configuration create more work for lab techs. In addition to the time wasted creating makeshift 96-well racks, the unused rows result in wasted space, which becomes an issue if specimens are required to be held in storage. With the number of tests being processed, it is critical to be able to store them as compactly as possible so this doesn’t impact the backlog even further.
Non-standard test tube racks also create problems with organizing and tracking individual specimens. “Keeping track of this mapping in an error-free way is really challenging,” Kenny notes. This eats up even more of lab tech’s precious time that could be spent doing the important work of actual testing.
Problem 3: Common Racks Don’t Have Enough Space In Between Test Tubes, Making Them Hard To Handle
The layout of most current test tube racks has very little separation in between test tubes, as can be seen in this common wire test tube holder rack.
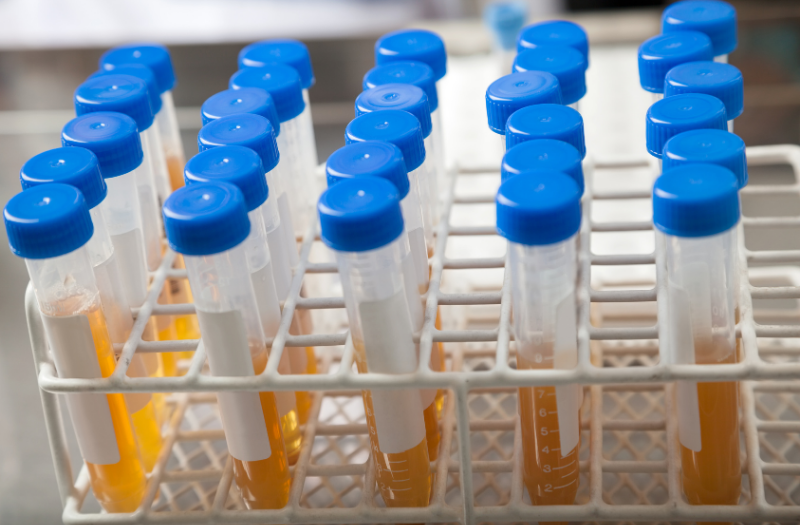
Notice that the only reason there’s any space between columns is that there are alternating columns that are kept empty. Now imagine test tubes being in every well.
Under normal conditions, this is simply an annoyance. But when lab techs are trying to work through a backlog of COVID-19 specimens, being able to easily retrieve samples impacts how efficiently they can work, especially if retesting is required and they must access tubes in the middle of the rack.
Problem 4: Many Test Tube Racks Are Flimsy And Poorly Constructed
In addition to the wire versions above, there are also plastic varieties that snap-together, like these.
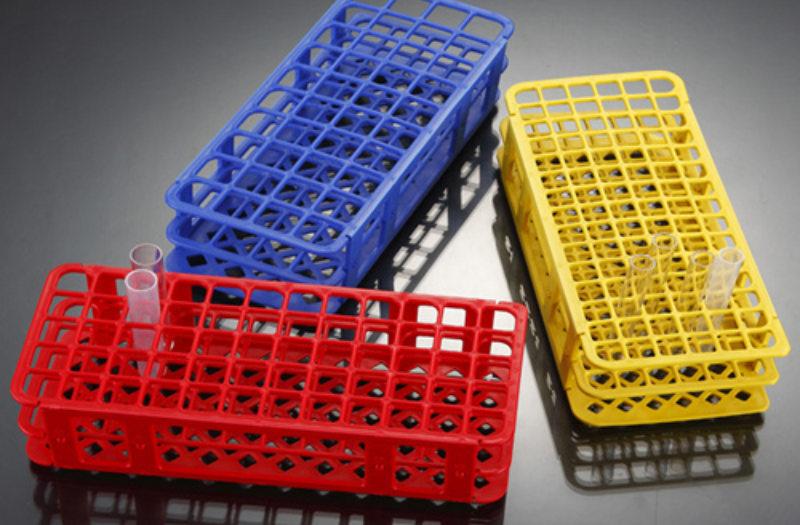
While they are relatively inexpensive, Aaron says that these styles are overpriced for what you get. Plus, they’re flimsy and can’t withstand the rigors of busy testing labs. A design that is sturdier—and easier to clean and sanitize—is needed.
Problem 5: Labeling Is Difficult With Wire And Plastic Test Tube Racks
As Kenny mentioned earlier, test tube racks that are designed to the 96-well industry standard have eight-rows (labeled A-H) and 12-columns (labeled 01-12). Being able to properly label test tube racks is critical in keeping specimens organized.
For example, let’s say specimen B7 needs to be pulled for retesting. Clear labeling ensures the right sample can easily be accessed for retesting and facilitates recording results accurately.
This process is hampered by the wire or plastic test tube racks because the tiny embossed lettering that is common on these types of racks is especially hard to read. Having to mentally orient the rack and then manually count to get the right specimen for testing is just one more thing to lengthen the testing cycle and slow down getting results reported.
Engineering A 96-Well Test Tube Rack To Meet Industry Standards
Kenny knew there had to be a better test tube rack design, so he recruited Aaron to evaluate the situation from an engineering perspective and create a custom solution that was superior to what’s currently available in the marketplace.
During high school, Aaron was very active with his school’s robotics (FRC) team. He learned about CAD as the Design Lead his sophomore year, was Build Captain his junior year and Team Captain his senior year.
By using the engineering-based problem-solving skills he learned in school, Aaron was able to develop a simple, yet highly effective, solution that addressed each of the five problems above so labs could put an end to the test tube rack conundrum.
Solution Consideration 1: Create Test Tube Racks That Are Affordable And Can Be Manufactured Quickly
Labs testing for coronavirus need a simple solution that is cost-effective, easy to assemble and can be put into practice immediately to help lessen the backlog.
That’s why Aaron turned to on-demand laser cutting. Acrylic is an affordable substrate, and manufacturing can happen in a couple days (overnight if necessary) whether you need one or 10,000 parts.
Once he determined the material and the method, Aaron could then turn his attention to the design.
Solution Consideration 2: Design 96-Well Test Tube Racks To Align With Industry Standard
Having a test tube rack that holds 96 specimens so each run could be set up to match the testing machine’s format is a critical aspect to Aaron’s solution. He began by creating a CAD rendering to determine the layout of all the parts.
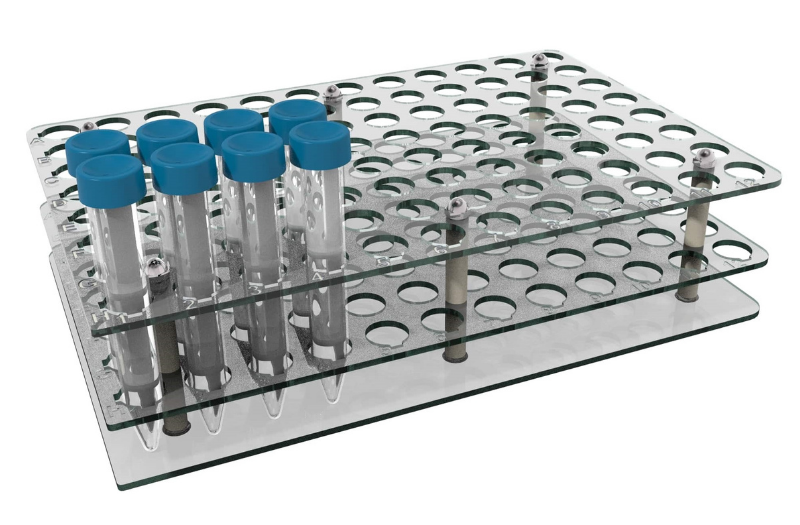
Next, he did several quick 3D prints of the first prototype on his desktop printer to initially test the concept. After some tweaks, he then came to Ponoko to laser cut the second prototype out of acrylic (with 3D printed risers) so the Fairview Hospital lab technicians could test them out. They requested a few more modifications that made their way into the final (third) version that is in use today.
Solution Consideration 3: Add Additional Space Between Wells So Test Tubes Are Easier To Access
In addition to having a 96-well layout, the test tube racks now have more space in between each individual well.
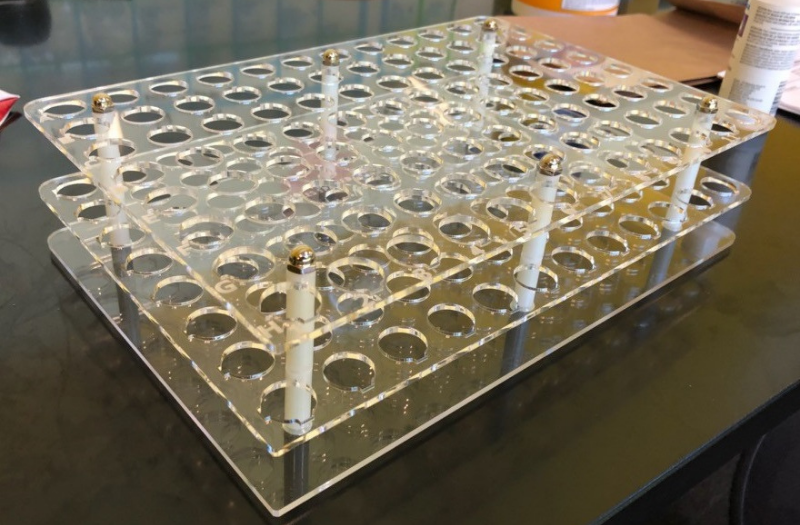
Larger spacing between test tubes means they are easier to grab, even in the middle of the rack.
Solution Consideration 4: Construct Test Tube Racks Out Of A Sturdy Material That’s Easy To Clean
What makes laser cut acrylic so great for this application? It’s strong without being too heavy. It’s a flat sheet, so it can easily be cleaned and sanitized.
Solution Consideration 5: Include Labeling Directly On The Racks
Engraved row and column letters help with indexing the test tubes. Notice these are significantly larger and easier to read than the tiny embossed lettering on common snap-together racks.
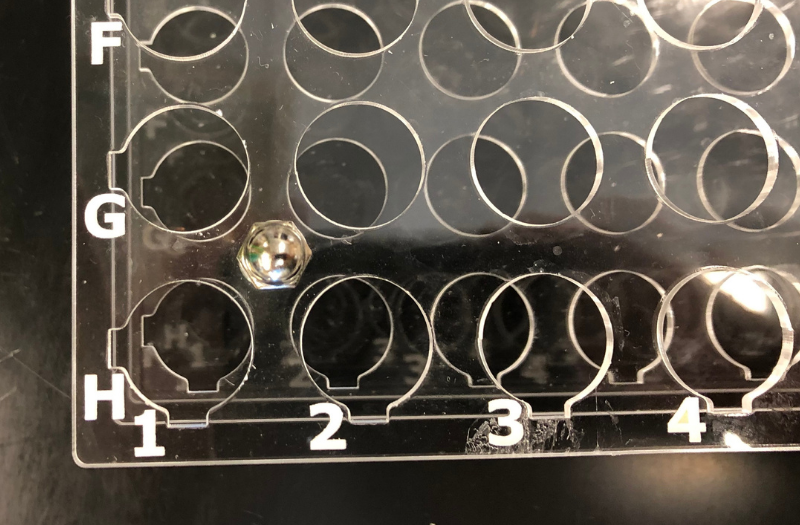
Improving Workflow And Efficiencies At COVID-19 Testing Labs
How has this new test tube rack design impacted the productivity of the UMN labs? “The racks enable one to set up the test runs and later re-pull samples for re-dos much more easily and without errors since the layout of the test run (96-well) is now identical between the racks of raw samples and the layout of those samples in test runs,” Kenny says. “By facilitating the process of efficiently storing and retrieving samples that need to be retested, the racks help eliminate errors and speed up testing. Plus, they make the life of the lab techs far more pleasant by removing a major hassle from the process.”
What’s great about these test tube racks is that the design is completely open source. Aaron has uploaded the files on Github, and they’re free for anyone to use.
“The design is meant to help any lab that could benefit from it,” Aaron says. “Currently, that would include coronavirus testing labs that are testing anywhere from a few hundred to a few thousand samples per day. Of course, since it’s open source, there is no push to market the design for profit. Rather, my goal is to make sure that it’s known as an option in case it could help anyone.”
Working With Ponoko: Flat Sheet Material Precision Cut Fast (And At Low Cost)
Once Aaron iterated designs on the computer through CAD and 3D printed several cheaper prototypes to make sure the concept worked, he began looking for laser cutting services so he could order larger quantities of the final parts. Like most Ponoko customers, he found us via Google search.
“Ponoko seems to be the only website with a proper instant-quote service and other websites had terrible volume pricing,” Aaron says. “Ponoko’s pricing is logical for one part up to thousands of them. The wide range of materials is also great. The price and no minimum order size definitely make it more accessible for small-scale makers [to get started with an eye on future growth].”
While Aaron built his alpha prototypes via desktop 3D printing, he switched to laser cutting for his beta prototypes and the final product. “Laser cutting allowed us to produce a sheet-based design, which is ideal for a test tube rack,” he explains. “Each rack is made up of three laser-cut profiles connected by bolts and spacers, allowing for a rigid and lightweight end product.”
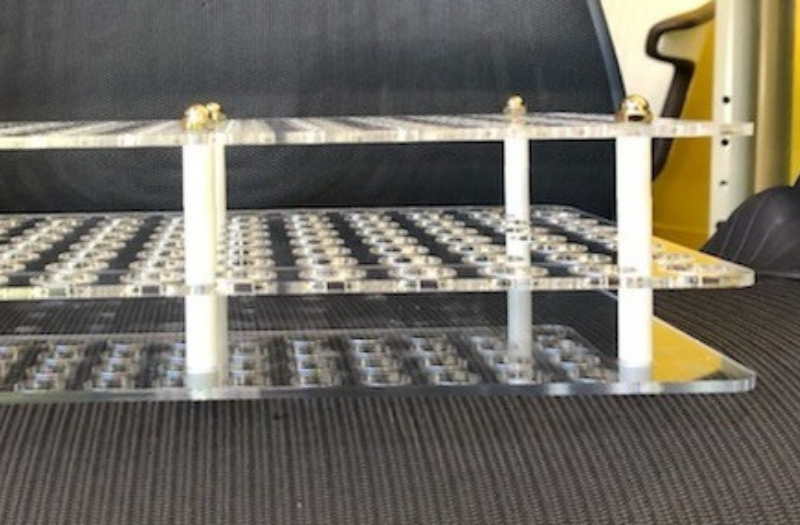
“We chose 3mm clear acrylic because it allows us to engrave the underside of the design and have text visible through the material, thus keeping the top clean and smooth while the labels are readable,” Aaron continues. “Also, acrylic is relatively chemical resistant, strong and inexpensive, making it suitable for this project.”
Little Solutions That Make A Big Impact
In times of crisis, many people want to pitch in to help in some way but they don’t know how. There’s a misconception that small contributions are just a drop in the proverbial bucket and don’t have significant impact. But that’s really not true, as Aaron and Kenny have proved.
Something as simple as a redesigned test tube rack really can make an impact. This is a major lesson for any kind of engineer to learn. By employing on-demand digital manufacturing, it’s possible to turn an idea into a solution to a big modern-day problem and into the start of a business.
Inspired by what Aaron and Kenny built together and want to make these test tube racks yourself? Here’s how:
1. Get open-source, Ponoko-optimized designs from GitHub.
2. Upload them to Ponoko to get an instant quote for making and shipping them to you today.
3. Make just 1—or 10,000!