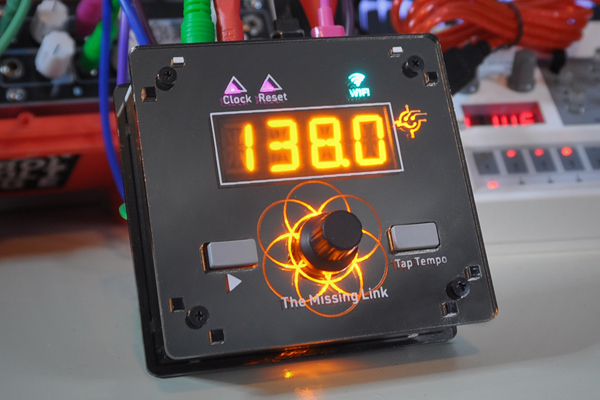
How Ed Guild Built The Missing Link Synchronizing Clock In Just Three Months
For musicians, one of the most important fundamentals to master is being able to keep time and establish rhythm, which becomes more and more important as the number of musicians playing together increases. That’s why bands have drummers and orchestras have conductors.
“It is thanks to time that we can make sense of music, and if we didn’t organize it in some fashion (rhythm), all we would hear would be a random collection of sounds,” says Paolo Lattanzi, ensemble instructor and the director at NY Ensemble Classes.
For electronic musicians, being in sync is especially important to avoid sounding like this random collection of sounds. However, being in sync is often easier said than done—a predicament that Ed Guild, who has DJ’d, VJ’d and performed with bands since 2001, has experienced first-hand time and again.
“When multiple electronic musicians get together to jam, there’s often this big discussion on how to sync everybody up in order to get everyone playing in time with each other,” he explains. “Sequencers need a shared clock source in order to play in time together, kind of like a pianist and a violinist listening to the same metronome or conductor to keep in time with each other.”
Makes sense. But the challenge is that electronic music setups are quite unique with each musician configuring theirs in slightly different ways. “There’s usually some negotiation on who will have to compromise their setup to share clock signals,” Ed continues. “And then, usually one sad person gets left out because they ran out of long cables to stretch over to their setup.”
Jam sessions are supposed to be fun, not a drag, which got Ed thinking. As the old adage suggests, “Necessity is the mother of invention,” and Ed saw an opportunity to fix the sync problem so that everyone could be making sweet music together in no time.
Introducing The Missing Link
What was missing was a universal clock of sorts that all the musicians could easily access. Say hello to The Missing Link, an analog clock generator for synchronizing modular synths, drum machines and other electronic noise makers.
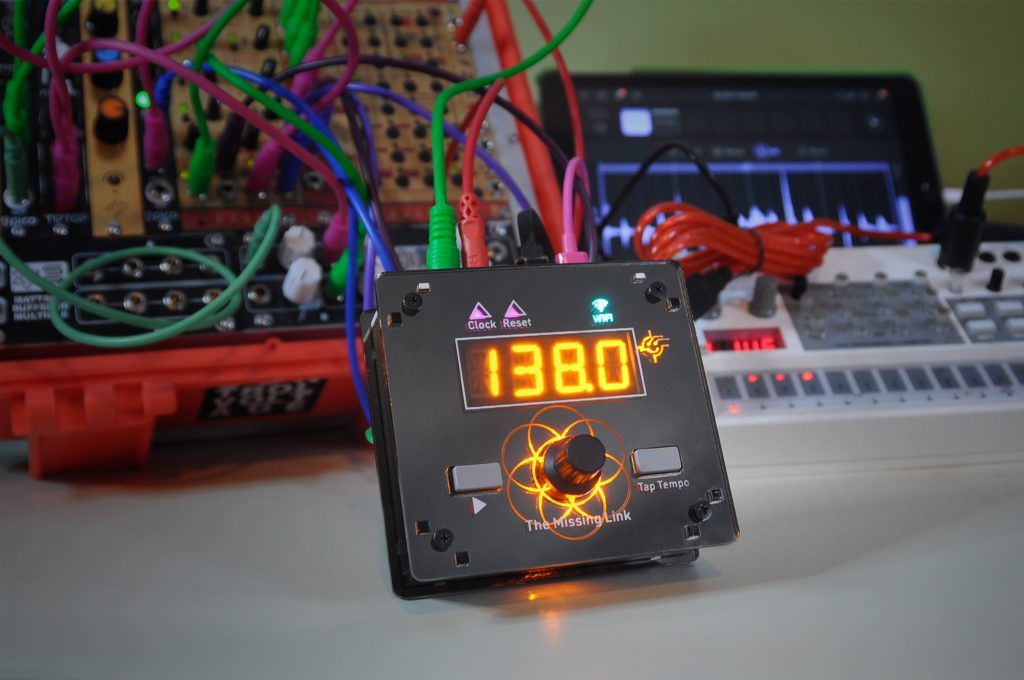
“With The Missing Link, if each person has one in their setup, then you just connect to the same WiFi network and everyone is synchronized. No negotiations needed!” Ed says. “And if one person decides to pack up and go, they won’t disrupt the rest of the players.”
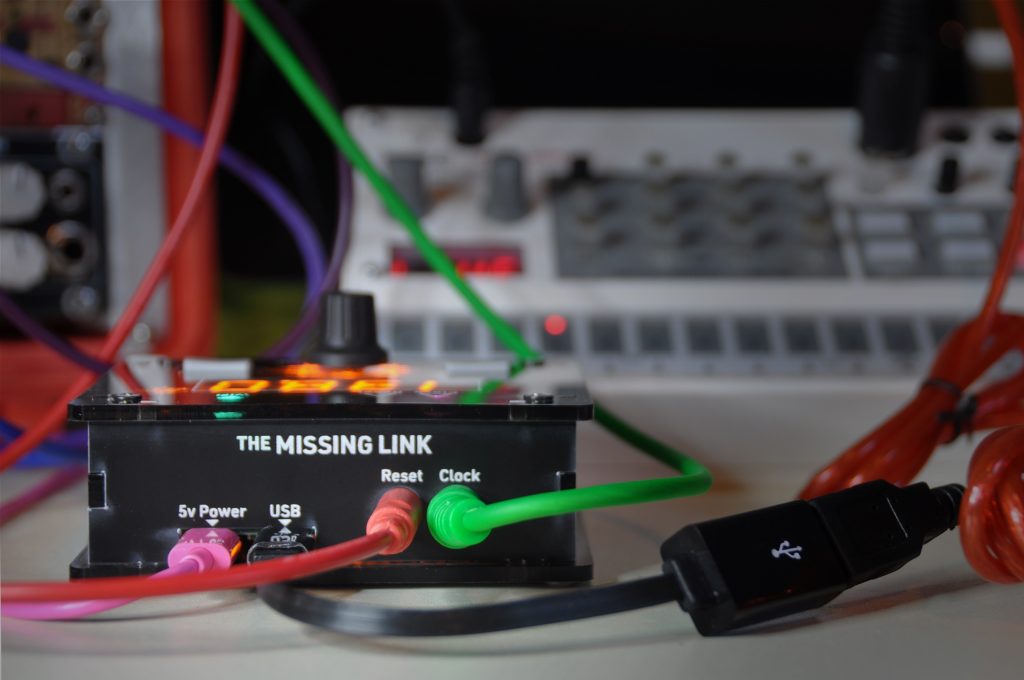
One of the things that makes The Missing Link special is that it supports Ableton Link. “To sync things, you usually must have lots of cables and adapters, but Ableton Link is an API for synchronizing musical applications over a local area network,” Ed explains. “It really makes it much easier to quickly jam out with your friends.”
Ed and a buddy designed and developed The Missing Link around the Raspberry Pi Zero W small board computer that runs a flavor of Linux. “It’s a pretty small but powerful computer that also supports WiFi that is FCC and CE certified,” he says. “The RPi Zero W is soldered directly to a PCB (printed circuit board) that holds all of the user interface widgets and the output jacks.”
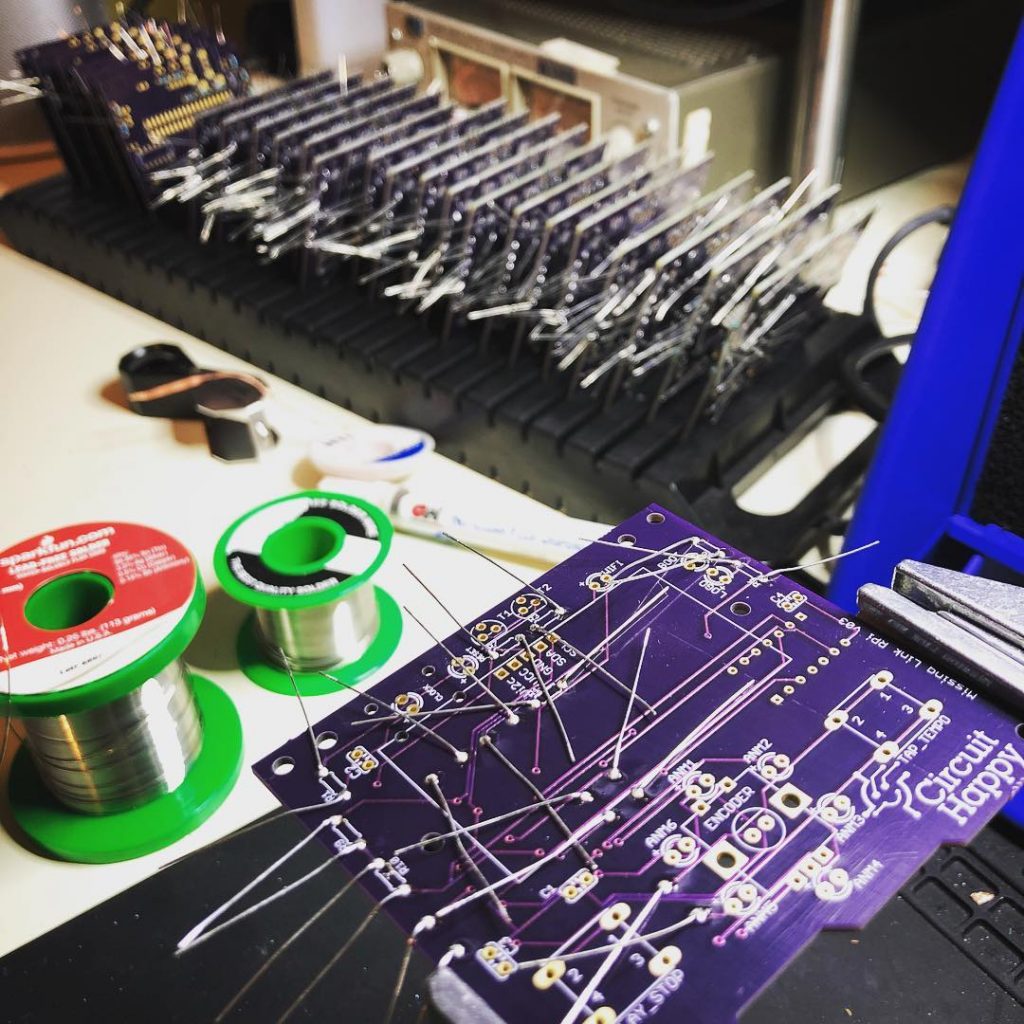
Designing Electronics Enclosures
While Ed spends his days surrounded by high tech digital components, when it comes to designing his next build, he goes old school.
“When I’m honing in on a design idea, I always use a notepad and pencil to sketch out how I think it should work,” he says. “I try not to think about the underlying implementation so I don’t limit myself. Once the sketch is complete, I bring it in to Adobe Illustrator to draw the ideas to scale. Next, I print out the faceplate design to see if the ergonomics make sense and the sizing works (e.g. buttons aren’t too close together). From there, it’s easy to convert that drawing to a layout for laser cutting with Ponoko. I can also use this same drawing to map out where my UI widgets will be placed on the PCB that will sit underneath the faceplate.”
In the case of The Missing Link, once Ed created the initial case design, it was time to select a manufacturing method and begin prototyping. “Making an extruded metal case seemed out of my price range and would require larger batch sizes to become affordable, plus a metal case would have less accessibility. Thus, I chose to laser cut my cases in acrylic because it was affordable for short runs (20-30 boxes per production run) and Ponoko has a wide palette of colors and textures to choose from.”
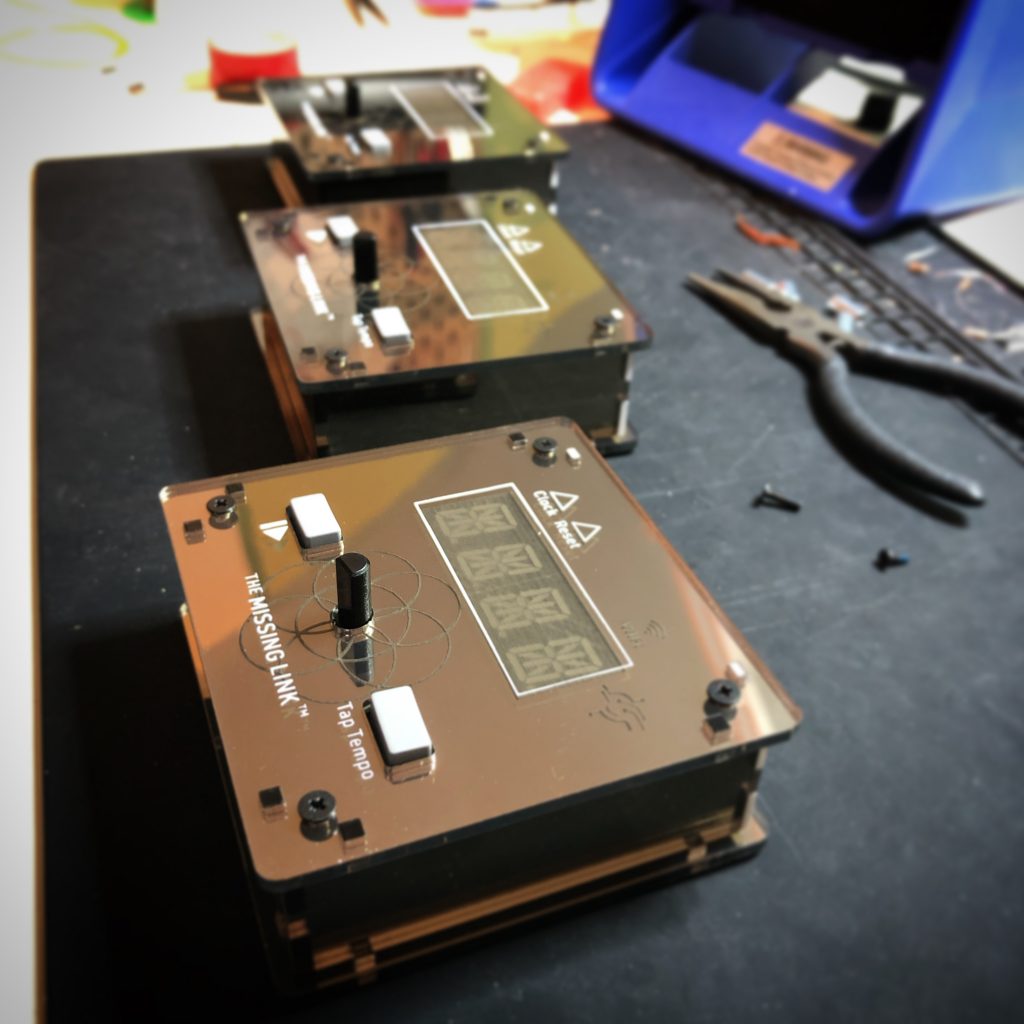
While black acrylic is a favorite for many hardware engineers, Ed decided to go a different direction for the faceplate and used bronze mirror acrylic. “I love the bronze mirror acrylic because you can etch away the back coating to reveal translucent windows that light up beautifully,” Ed says. “The result is a dazzling display shining up through a perfectly smooth faceplate. It looks very distinctive compared to the black metal boxes these types of utility devices usually come in.”
Working With Ponoko
As mentioned above, Ed originally looked at metal case manufacturers when considering different production options. “But it seemed so much more involved and intimidating to get a quote for your job,” he says. “Conversely, I was impressed to see how Ponoko worked. I simply uploaded my file, chose the material and received a detailed view of the costs (cut time, shipping, job priority). Plus, I didn’t have to look any further once I saw all the available materials. I made a test design to try out the Ponoko service and was quite pleased with the whole process.”
Having the ability to quickly iterate prototypes also helped Ed bring his product to market quickly. “The amazing thing with getting my cases produced via laser cut acrylic is that the prototype design IS the final design if it’s good to go,” he says. “I don’t have another step to produce the case in another material. I think I went through three iterations that I cut in acrylic before I landed on my final design. It took about three months to hone in on the design while I was juggling PCB design as well.”
What one piece of advice does Ed have for other makers? “Don’t be afraid to try out a few materials before you settle on one,” he says. “I happened upon the mirror finish acrylics on a lark when I was first testing out the Ponoko service. I didn’t intend to make my box with a bronze mirror acrylic; I was just curious what it looked like in real life so I did a test cut on it. But when I saw the output, I realized this was exactly what I was going to use. I think a lot of my customers are drawn to my product not only for its feature set, but also how it looks. It is quite unique.”
To learn more about The Missing Link and keep up with all of Ed’s endeavors, visit Circuit Happy and follow him on Instagram.