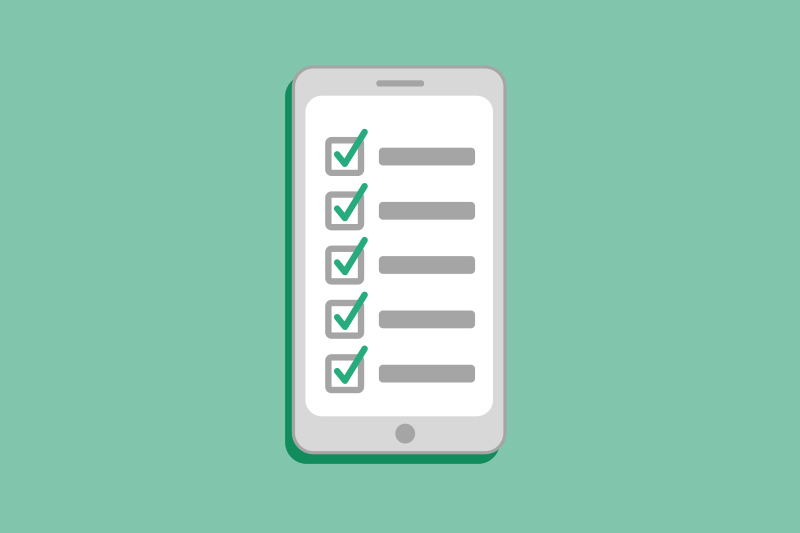
Best Practice For Successful Electronics Designs
This post was written by Chris Hii and reposted with from the Predictable Designs blog
Designing smart, secure, and power efficient electronic devices is truly an art. The design process from concept, to prototype, to deployment can be long and arduous, but at the end of the day it is truly rewarding to see your creation come to life.
A product design is successful when it meets required functionality, can be easily manufactured, is reliable, and withstands the environment it was designed for.
These principles are a quick and easy guideline for design engineers looking to save time and money (not to mention headaches) right from the start.
Considerations in Product Design
These are the considerations to keep in mind while designing embedded electronic hardware solutions.
Understand the operating environment
The system must be designed to tolerate the environmental requirements and conditions. For example, a system that operates solely indoors will have very different requirements than a system that operates outdoors in all weather conditions.
The operating temperature range, pressure, humidity, required ruggedness, exposure to radiation, etc. must all be considered in the design and validation phases. Also, don’t forget about power dissipation and thermal analysis.
Design in additional margin where possible
Don’t box yourself in where you don’t have to. Adding provisions for additional capacitance, the ability to increase current limits, supporting higher-resolution screens, etc. are all good ideas as long as other constraints like cost and development time don’t override them.
Keeping options open gives you more flexibility down the road. This is also applicable for power supplies. Over-design them when possible to allow for future functionality and increased power draw.
Plan for future features where possible
If you know a feature or an upgrade may be coming, plan for it early on whenever practical. Again, this leaves you with more options in the long run.
However, don’t go overboard and you need to always prioritize minimizing your development time, cost, and risk. Always keep the Minimal Viable Product (MVP) concept in mind when you consider designing for future features.
Know your components
Read the entire data sheet and all reference materials thoroughly to ensure understanding of the part capabilities and limitations.
Design for flexibility
Plan ahead to incorporate “additional” options that may prevent the need for an extra design spin to add a feature down the road.
This for example can include adding a footprint for a Wi-Fi or Bluetooth module, but not populating it unless or until needed.
Add provisions to ease debugging
Make debugging easier on yourself and your team during the board bring-up and development phases. You will be thankful later.
One good way to start: use pull-up/down resistors instead of making direct connections to VDD and GND for IC configuration pins.
Give yourself options to disconnect power supply inputs and outputs in case you need to take current measurements or otherwise isolate supply rails.
Make the firmware developer’s life easy. Consult them early in the design for what interfaces may help them develop and test the code. This usually includes a debug port (SWD, JTAG, etc.), a UART, and one or more GPIOs or LEDs.
Always think about testing. Add ample test points for automated production testing in a “bed-of-nails” or similar type test jig.
A consumer product will only be successful if it can be manufactured and tested reliably. Untested or poorly tested designs can hurt customer relations and the bottom line with extensive returns and RMAs.
Incorporate electrostatic discharge (ESD) protections
ESD is inevitable on any user-accessible interface, so plan accordingly to protect your design. Use protection diodes, current-limiting resistors, and other devices to protect every pin exposed to the outside world.
Add electromagnetic interference (EMI) mitigations
EMI problems can be far-reaching and negatively impact your device’s performance, reliability, and ability to be sold to the public.
Regulatory restrictions vary around the world but in general most electronic products will need to comply with one or more sets of EMI restrictions.
Minimize your chances for EMI issues from the start of the design, by adding common-mode chokes, ferrites, and other EMI-suppressing devices to all connector interfaces.
Use balanced, differential interfaces over single-ended for high-speed signals whenever practical.
Consider the BOM cost early on
If the BOM costs get carried away, the project may be doomed from the start. Careful planning and estimating with your designers can help avoid unwelcome surprises. Keep an eye on the BOM cost throughout the design phase.
If you can’t manufacture and sell the product at a reasonable profit then there is no point in proceeding further.
Validate component availability
Work with your preferred distributor(s) early on to understand availability and lead times for your critical components.
Passives like resistors and capacitors can generally be replaced with form/fit/function (FFF) compatible alternatives during manufacturing, but this may not be possible for other components like ICs and connectors.
Create clean, well-documented schematics
The fact is you may very well have to switch designers before your product is totally complete. So you need to make this transition as smooth as possible by having proper design documentation.
Nothing is worse than having to look at a cluttered rat’s nest of a schematic diagram and try to make sense of it.
It is a good idea to use a hierarchical topology. Place inputs on the left of sub sheets and outputs on the right.
Add notes through the schematics to indicate design considerations, IC settings, filter parameters, and other non-trivial information to whoever looks at the schematic next.
Specify all component parameters for the BOM. Be leery of specifying “generic” for anything but resistors. Even capacitors with the same capacitance, voltage, dielectric, and package types can vary a lot from manufacturer to manufacturer.
This same advice also applies you any software development, and you want your code to be properly documented so others can easily work on it in the future as needed.
Be sure to download your Ultimate Guide: How to Develop and Sell Your New Electronic Hardware Product.
This article was written by Chris Hii and was originally posted on Predictable Designs, a company which helps entrepreneurs bring new products to market.