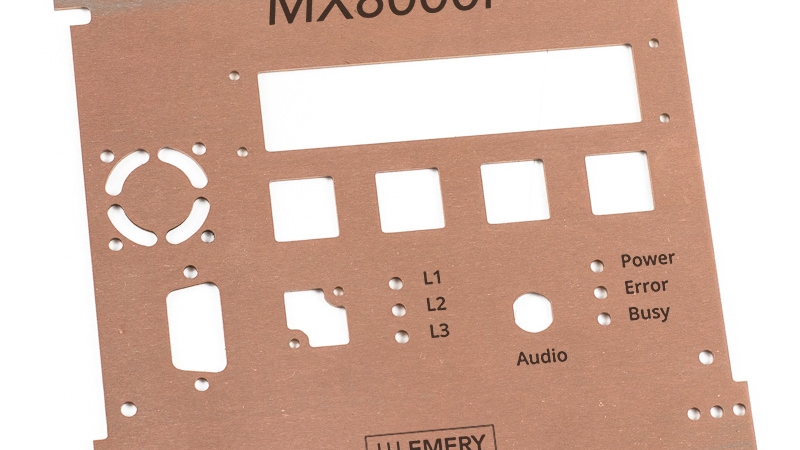
What is Copper Sheet Metal Fabrication?
As the world continues to rely on a wide range of metals for numerous applications, sheet metal fabrication has become a crucial aspect of manufacturing. One such metal that is relied upon in a wide range of different sectors is copper due to its highly conductive nature, malleability, and ease of machining. However, before we explore how copper sheet metal fabrication helps the copper industry, we first need to understand what the term “sheet metal fabrication” means.
Sheet metal fabrication refers to the production process of creating structures using sheets of metal. These sheets are often welded together, but other techniques can be used including riveting and bolts. When it comes to laser cutting, sheet metal fabrication can greatly benefit from laser cutters as they provide extremely precise cuts in a wide range of metals, can be engraved with patterns, and are quick to produce extremely complex shapes. Other machining techniques used with sheet metals include milling, water jetting, and plasma cutting.
The wide range of manufacturing techniques available for sheet metals thus allows for a high degree of flexibility during the production process, and this is particularly advantageous when working with materials that can be challenging to work with. For example, copper is known for its ability to oxidise, and this can make welding and other high-temperature processes difficult, but the use of an inert gas atmosphere can help to overcome such challenges (something which can be pumped into laser cutting and CNC stations).
The ability to engrave copper using a laser cutter also allows for designs to incorporate graphics and logos, something which is commonly found on electrical equipment, PCBs, and valuable objects such as jewelry. Finally, the ability to easily machine and shape copper makes it an ideal material for numerous applications, including bus bars, heat sinks, electrical contacts, and decorative pieces. The high malleability of copper also means that it can be easily recycled, making it an environmentally friendly choice for future engineering projects.
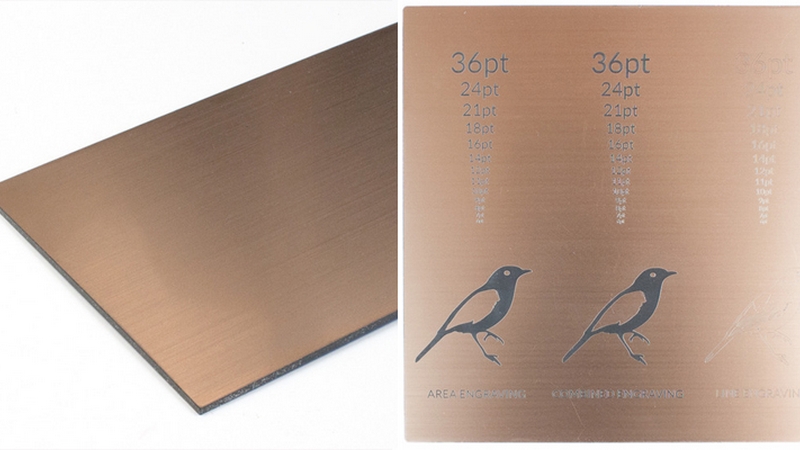
Types of Copper Sheet Metal
Copper is an extremely versatile metal that has been used by man for thousands of years due to its ability to be melted down, machined, and use in a wide range of applications. While copper can be 100% pure, it is rarely this due to the challenges associated with refining the metal to this degree, and copper that is 100% pure is far too soft for many applications. As such, copper products are often around 95% to 98% pure, with the remainder being additives that help with machinability and other physical properties.
One such additive is zinc, and the resulting copper-zinc alloy has a wide range of applications including plumbing due to its malleability, resistance to corrosion, and ability to be easily machined. Another common additive is tin, and copper-tin alloys (such as bronze) are commonly found in large bearings that need to be non-corrosive as well as have a high tensile strength.
Copper can also be alloyed with nickel, and these copper-nickel alloys are commonly found in decorative hardware and other consumer products. For example, 110 H02 Copper is corrosion resistant, has excellent electrical properties, and a high degree of ductility. Being 99.5% pure, this type of copper is great for all kinds of applications, including electronics, scientific equipment, and chemical systems.
110 Annealed copper is the same as 110 H02 copper, except that it has been annealed to reduce its hardness and improve ductility (and thereby making it suitable for further machining and mechanical manipulation).
Photochemical Machined (PCM) copper is another option for engineers, but it isn’t a particular material, instead, it is a manufacturing process that stands out from traditional methods. PCM is photochemical machining, which utilizes etchants to remove unwanted copper from a part. This is ideal for extreme precision applications, including mechanical moving parts, scientific parts, and PCBs.
Options for Surface Finishes
Like most sheet metals, copper sheets can have a wide range of different surface finishes. A mirror polish can be used to reflect light and give copper a highly professional and high-end appearance, while a matte finish can be used to remove some of the shiny appearance of copper.
Copper can also be engraved with patterns and text to create highly distinctive designs. This is commonly seen on copper panels used in electronics that indicate user settings as well as decorative pieces such as plaques. The extreme precision possible with engraving also makes it ideal for copper parts requiring a high degree of accuracy (such as those found in the PCB industry).
Printing is another option for surface finishing of copper, and this is ideal for creating designs with colour as well as text. A printed design can be overlaid on a mirror or matte finish for a highly professional appearance or for use as decorative piece.
Copper can also be photoetched to create extremely intricate designs with high degrees of precision. Photoetching involves a mask of a design which is then placed in a tank of strong acid, and the exposed areas of the mask are attacked by the etchant, thus removing it.
The high ductility of copper also makes it easy to debur, removing sharp edges that can potentially cut users as well as making future manufacturing processes easier (such as soldering). A burr can also make it difficult to produce high-quality prints and engravings, making deburring an essential step in the manufacturing process.
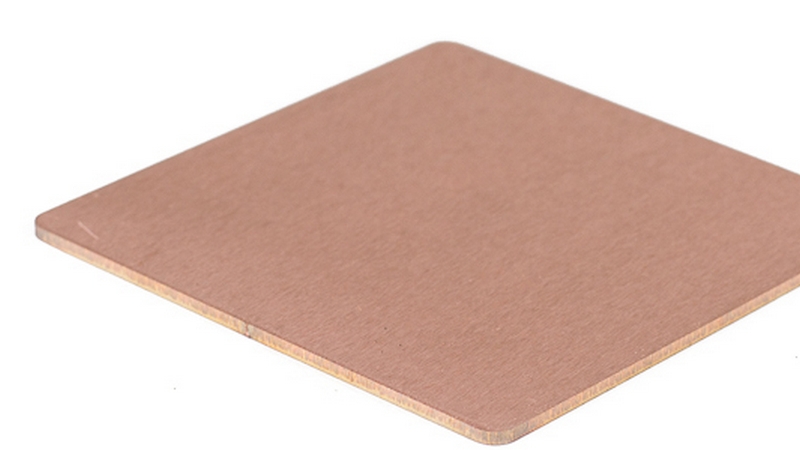
Design Tips for Your Copper Sheet Metal Project
When exploring materials for a project, it is essential to not only consider the functional aspect of the material but also its potential impact on the final result. As laser-cut copper can exhibit warping and expansion due to the extreme heat generated by the laser, small features on the edge of a design may struggle to maintain their precision.
Therefore, designs that require high levels of accuracy should take this into account and either avoid the use of small features, or accept that there will be a certain degree of variation. The heat treatment caused by laser cutting also affects the characteristics of the edge, and this heat treatment can only be removed by using heating processes such as re-tempering.
Finally, the soft nature of copper means that it is easily machined, but this also means that it is also easy to scratch. As such, designs that will be exposed to the environment or expect to last a long time should consider hardening the edge through heat treatment.
Can copper be laser-cut?
Copper can indeed be laser-cut, but the numerous challenges that it presents makes laser cutting a difficult task. To start, copper is an extremely reflective material that absorbs very little of the infrared light produced by laser cutters, and this can lead to a reduction in laser cutter efficiency. Furthermore, the high-reflectivity of copper also introduces a real danger of laser beam reflection back into the laser itself, and this can damage sensitive components including lenses and mirrors.
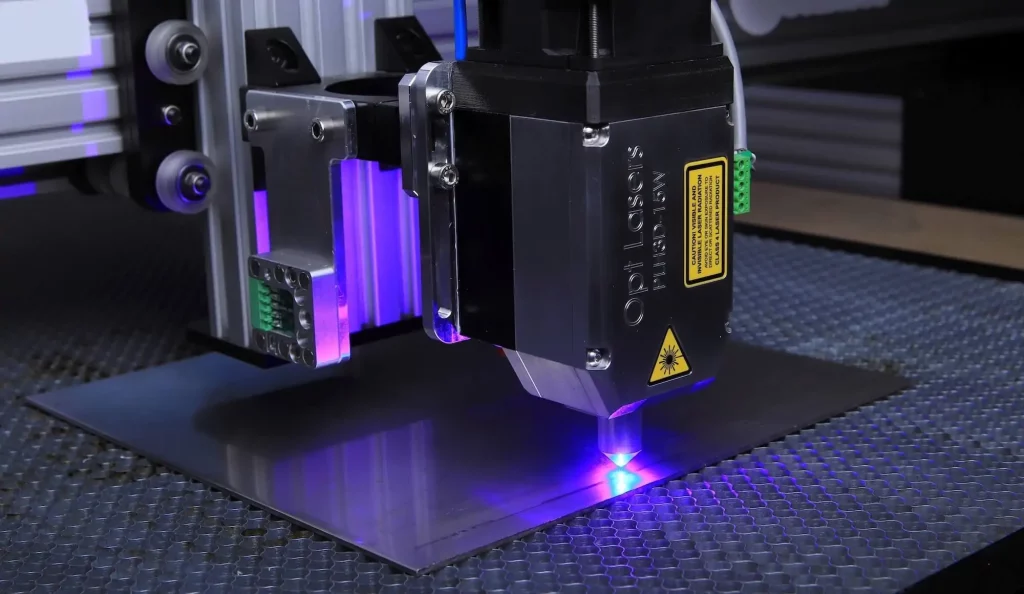
Is copper sheet metal expensive?
Copper is a precious metal, as such, is an expensive material to choose. However, one only needs to look at the properties of copper to understand why it is so highly valued. Thanks to Ponoko’s experience in the field of machining and laser cutting, our services help to make laser cut copper parts highly economical. Furthermore, because Ponoko is able to produce parts extremely quickly, the time saved in engineering projects helps to save money in the long run, allowing engineers to focus on part design and design iterations.
How do you prevent copper sheets parts from tarnishing?
Copper parts, being exposed to the environment, will eventually tarnish unless protected from moisture and/or oxygen. One common method for preventing oxidation is to apply a conformal coating of lacquer, commonly found in automotive-grade products, but such coatings make soldering of copper parts difficult, if not impossible, and can also interfere with the conductivity and malleability of copper.
An alternative method is to electroplate the copper with a thicker layer of a metal such as gold, but this also affects the properties of the underlying copper. Thus, it is essential that engineers consider these factors when choosing a method for preventing tarnishing.
What industries is copper sheet parts ideal for?
Copper sheet parts are ideal for a wide range of various industries that require high conductivity, precision, and repeatability. One industry that can highly benefit from laser-cut copper parts is the electronics industry. The high conductivity of copper makes it ideal for manufacturing bus bars and other power distribution mechanisms, and the precision of laser-cut parts makes them highly suitable for microwave and RF applications.
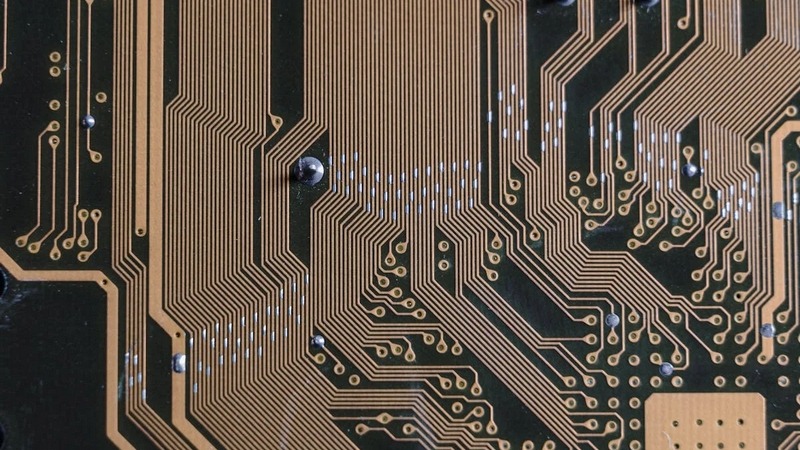