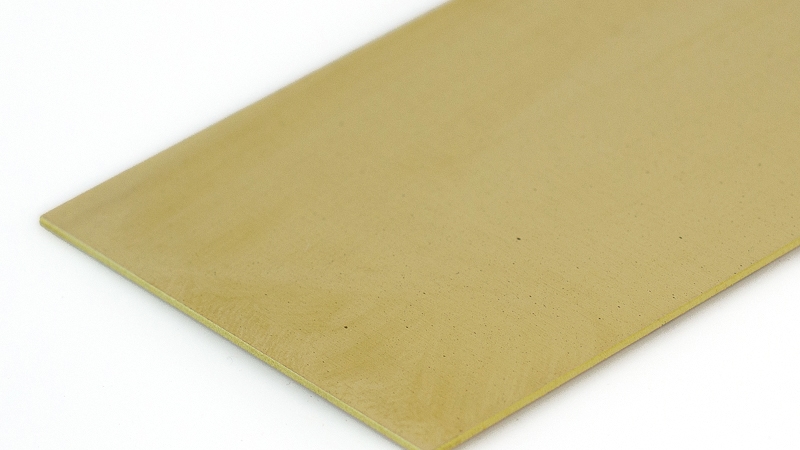
Why Brass Sheet Metal Fabrication Matters!
Brass is a versatile material that offers numerous advantages, making it an ideal choice for various applications. Its antibacterial properties make it ideal for applications where hygiene is paramount, and its smooth surface finish makes it visually appealing, making it perfect for decorative pieces. Additionally, brass has extremely low surface friction, making it ideal for applications that require components to glide or move smoothly, such as mechanical systems and actuators.
However, just because brass is an excellent material doesn’t mean that it will automatically produce good parts; the manufacturer is equally as important. Ponoko fully understands the requirements of brass components and has years of experience in manufacturing custom brass parts, having been used in a wide range of applications, including automotive systems and satellites orbiting Earth. Our expertise in precision manufacturing ensures that every part leaving our facility meets the highest standards, whether it’s a prototype or a production piece.
At Ponoko, we not only focus on precision to reduce the time taken to manufacture parts, but we also strive to do so at speed. Our manufacturing capabilities enable rapid production, and this means that prototype iterations can be produced and tested in record time. This efficiency also results in cost savings, making custom brass parts more economical, even for low-volume production runs. With every iteration of a design, our expertise helps to reduce both the time to market and the overall cost, making us the ideal partner for engineers looking to optimize their projects.
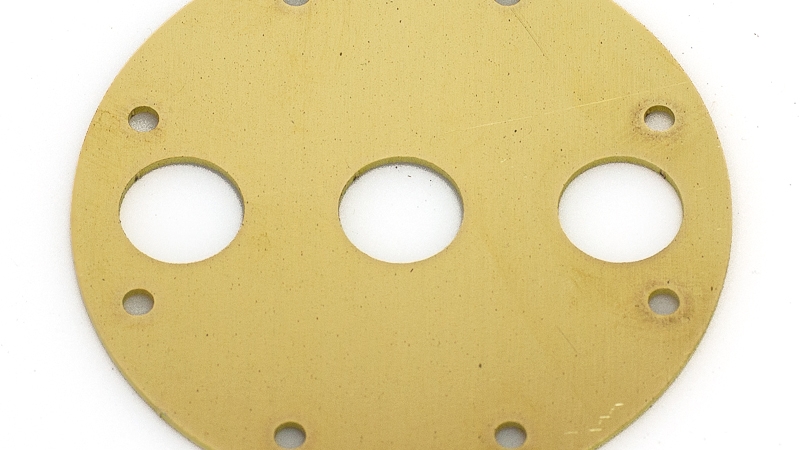
What is Brass Sheet Metal Fabrication?
Brass sheet metal fabrication involves taking brass sheets and using various manufacturing techniques to bring them to life. One such technique is shearing, whereby a sheet of brass can be sheared through to create a clean cut right through the sheet. For example, shearing can be used to cut out rectangular shapes that will later be used as a base plate for a larger design. The smooth finish of the sheared edge also means that no additional machining is needed on the edges, which in turn helps to reduce manufacturing costs and time.
Using computer numeric control, CNC cutting can be used to create highly complex shapes with great precision. Brass parts being fabricated using CNC cutting can include brackets, fittings, and enclosures that require a high degree of accuracy, such as an EMC shield that needs to have a high degree of consistency across all parts. The ability of CNC cutters to produce repeatable results also means that man-made parts using CNC cutters will be just as precise as mass-produced parts, thereby making hand-made CNC-cut parts reliable and dependable.
Laser cutters provide the ability to cut brass sheets at high speed, and the lack of tooling means that laser cutters do not suffer from the same issues seen by CNC machines, such as the need for new cutting tools and reduced machine performance as tools wear down. The ability of lasers to cut with great speed also means that they are an ideal choice for mass production of brass parts, and the high degree of accuracy and precision of lasers also makes them ideal for custom parts in high-quantity orders.
Another useful fabrication technique for brass sheets is bending, which can be used to turn 2D parts into 3D structures. For example, laser-cut 2D brackets can be bent into 3D brackets to create enclosures, fixtures, and fittings. The smooth nature of bent brass also means that no additional machining is needed on the edges, thereby giving bent parts the same finish as sheared parts.
Overall, brass sheet metal fabrication presents engineers with an ideal material thanks to its high durability, high-temperature capabilities, and high resistance to corrosion. The numerous fabrication techniques available to engineers further increases the capabilities of brass, making it ideal for a wide range of applications.
Types of Brass Sheet Metal
When it comes to selecting materials for a wide range of different applications, great care has to be taken as even the most basic materials can exhibit a range of different characteristics. For example, brass is an ideal material for those looking to create corrosion-resistant parts that can withstand a wide range of different environments, and our 464 Marine Grade brass is an excellent option in this case. As this material is lead-free, it makes it ideal for use in salty environments, such as near the ocean, and its high resistance to corrosion also makes it ideal for propeller blades, pumps, shafts, and rivets.
While our 464 Marine Grade brass excels in its ability to resist corrosion, our 260 H02 brass is an ideal material for those looking to create parts with a high degree of ductility. This means that 260 H02 brass is ideal for use in applications that require parts to be bent, such as door hardware, as well as ammunition cases. By not snapping or cracking under stress, 260 H02 brass is also ideal for applications that require a high degree of strength to weight ratio, and its ability to resist corrosion also makes it ideal for propeller blades, pumps, shafts, and rivets.
For those looking to create engraved signs or other metallic decorative pieces, our 353 brass is an ideal option thanks to its high hardness. As such, engraved designs will last for a long time, and the high tensile strength of 353 brass also makes it ideal for nuts and gears. The high strength of 353 brass also makes it ideal for soldering, which requires a high degree of surface area to metal contact; the malleability of 353 brass would otherwise see it deform under soldering temperatures.
Overall, all of our brass products offer engineers with a high degree of versatility, whether it is for creating decorative pieces, equipment that requires high tensile strength, or parts that need to resist corrosion.
Options for Surface Finishes
When it comes to providing surface finishes, sheet brass is just as capable as any other sheet metal. The first finish that is particularly useful is sanding which is commonly used to remove rough features and provide a smooth finish. However, it should be noted that such a finish may not be entirely smooth to the touch, and the high-grit nature of such a finish makes it more applicable in areas where aesthetics are not the main concern. An example of where a sand-based finish would be beneficial includes structural components such as brackets and mounts.
Deburring is another surface finish option available to sheet metal brass components, and this is especially useful where small holes have been drilled or cut out. During the manufacturing stage, it is possible for sharp debris and swarf to build up around holes and cut-outs, and this can lead to parts being difficult to assemble. A deburred part, however, has edges that are smooth and clean, and this helps to also improve the longevity of parts (such as enclosures), by preventing damage from sharp edges.
A polished finish is the most refined surface option available, and can be useful for parts where aesthetics are essential. A part with a polished finish will be so smooth that it will feel like glass, and reflections will be mirror-like. However, such a finish is also extremely challenging to achieve, and the high degree of machine effort needed makes it expensive. As such, a polished finish is typically reserved for parts that are being used in high-end applications.
Overall, sheet metal parts can take advantage of a wide range of different surface finishes, and the variety of options allows for designers to craft parts that not only look good, but also feel good.
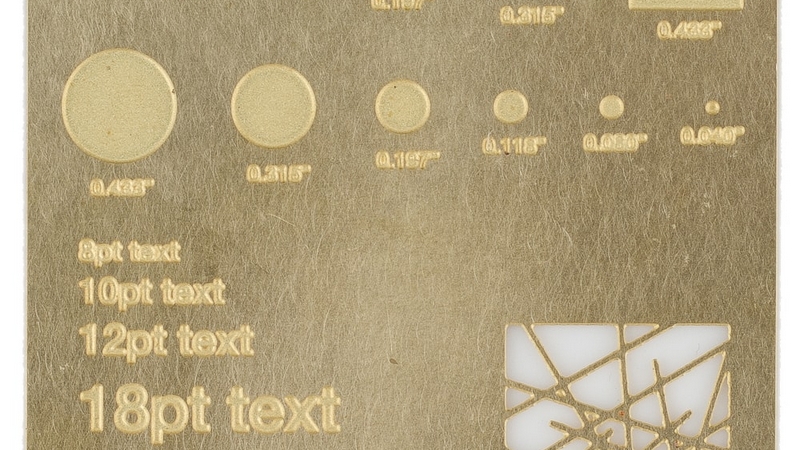
Design Tips for Your Brass Sheet Metal Project
When working with brass, it is essential to recognise that not all brass is created equal, as different variations can exhibit varying characteristics. For instance, some brass varieties feature grain lines on their underside, such as 353-H02 brass, which specifically have this feature to prevent fingerprints from showing. This highlights the importance of carefully checking the properties of brass before commencing a project, as using the wrong type of brass can lead to unintended consequences.
Another important consideration when working with brass is its high surface smoothness, which also contributes to its low surface friction. While this smoothness makes brass ideal for applications that require minimal surface roughness, it also means that brass parts can move around during the cutting process, especially for smaller parts. As such, engineers need to take extra precautions when cutting brass to ensure precision and accuracy.
Brass can also be prone to corrosion, meaning that engineers should consider the environment in which their parts will be used. For example, decorative brass parts may be exposed to sweat, and over time, rust stains and marks can form. To prevent this, engineers should select brass variations that resist corrosion, such as some 303 variations, which are specifically designed to age well.
Finally, engineers should be aware that the electrical properties of brass also vary depending on the specific variation. Therefore, applications that require specific electrical characteristics should choose brass that meets those needs. Overall, engineers should always double-check their brass, as the many characteristics of brass can lead to a multitude of potential problems.
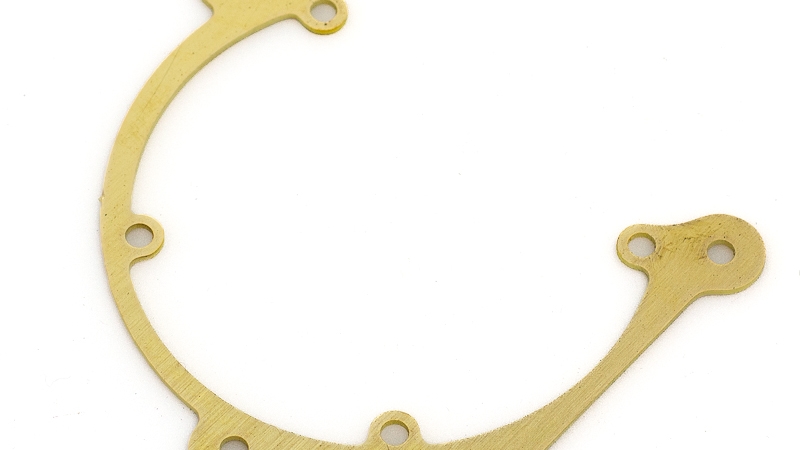