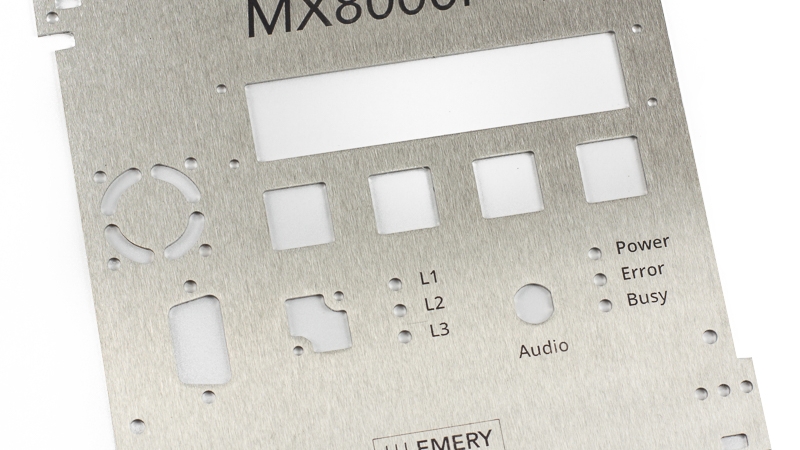
What is Aluminum Sheet Metal Fabrication?
Aluminum Sheet Metal Fabrication is the process of creating aluminum parts utilising sheets of aluminum and using manufacturing techniques commonly used with sheet metals. For example, aluminum sheets can be pressed, stamped, punched, drilled, CNC milled, laser cut, water jet cut, and plasma jet cut.
Each of these processes has its own pros and cons, meaning that it is important to recognise the difference between them, and when to use each one. In the case of a punch and die, the use of a singular mechanical action allows for the creation of parts extremely rapidly, but this requires custom dies which can be expensive.
But of all the manufacturing options available to engineers when dealing with aluminum sheets, laser cutting provides arguably one of the best solutions, thanks to its high precision, speed, and repeatability. Furthermore, laser cutting is also ideal for creating 2D aluminum parts with complex shapes and cut-outs, thanks to the ability for laser cutters to move in both axis freely.
Other processes, such as CNC and water jet cutting, can be used for both precision and large-scale production, while plasma jet cutting is best used for cutting thick sheets of metal. Drilling is another common manufacturing step that involves creating holes aluminum sheets, and this is often used for creating mechanical fixtures such as brackets and mounts.
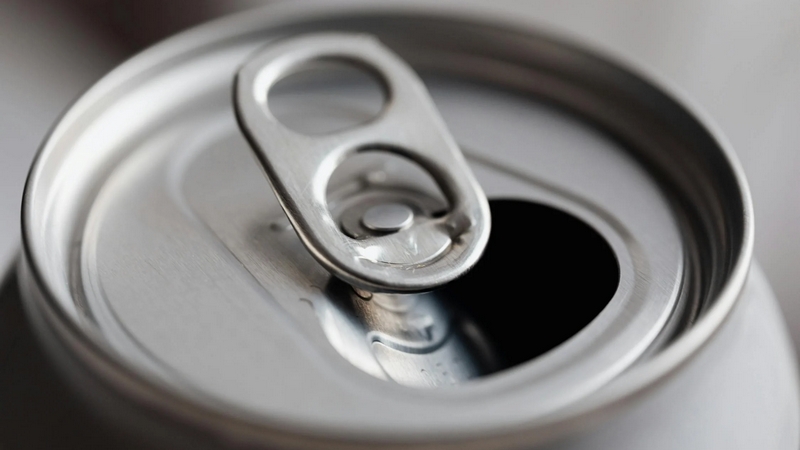
Types of Aluminum Sheet Metal
Aluminium, a highly malleable and lightweight metal, is available in a variety of grades that allow for its characteristics to be adjusted. From decorative to structural applications, aluminium sheets can be used in almost any environment thanks to its excellent strength to weight ratio, electrical conductivity, and machinability.
The 5052 aluminium grade is one of the most commonly available varieties of aluminium and is ideal for consumer and industrial applications. Its cost-effectiveness, lightness, and high strength make it suitable for a wide range of parts including enclosures, brackets, and structural components.
While corrosion resistance is not a major concern for 5052 aluminium, some applications may require a higher degree of protection. In these instances, the 6061-T6 aluminium can be used due to its temperature treatable properties and high strength. The excellent strength of 6061-T6 makes it ideal for aerospace and automotive applications, and its resistance to corrosion also makes it suitable for use in tanks and fluid transport.
A more corrosion-resistant aluminium, the 1100-O variety, makes it ideal for decorative and electrical applications. The extreme softness of 1100-O aluminium requires extra care during manufacturing processes, but the resulting material offers excellent resistance to corrosion. This trait makes 1100-O ideal for raceways and other environments where strength is not essential.
Options for Surface Finishes
Aluminium parts can have numerous surface finishes, all of which can massively improve the appearance and performance of a part. One common option for engineers is to take advantage of laser engraving, which allows for graphics and text to be etched into the aluminium. While engraving can be used for any design imaginable, it is especially useful for adding unique logos and serial numbers to parts in industrial and automotive environments.
Another popular choice for those needing to remove excess material from the edges of parts (as well as smoothing edges) is deburring. As sharp edges and pieces of melted material can form during laser cutting, deburring helps to remove small shavings and burrs that can interfere with further processing and performance.
For those needing to create parts that conform to high standards of quality and aesthetics, polishing is also an excellent choice. The ability to polish laser-cut aluminium makes laser-cut parts market-ready, meaning that they can immediately be used in consumer products.
Finally, engineers can also take advantage of printing for custom graphics. Unlike engraving, direct printing (both screen printing and inkjet), allows for full-color designs that can be used to create highly eye-catching parts. Printing also allows for text and graphics to be combined with other finishes such as polishing and deburring for a part that is both functional and visually appealing.
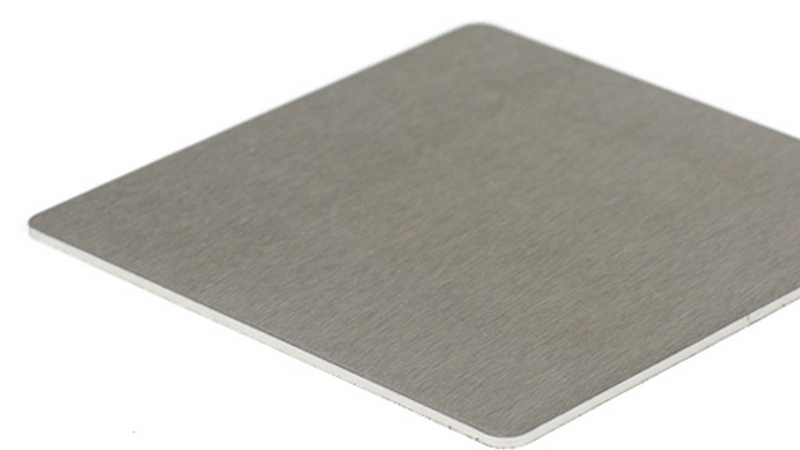
Design Tips for Your Aluminum Sheet Metal Project
When approaching a sheet metal project with aluminum, the first consideration that must be taken is the thermal expansion that aluminum experiences. As laser cutters rely on the thermal properties of a material to allow for vaporization, it is essential that a design takes into account how a piece of aluminum will change in size as it is heated. This is particularly an issue for those creating precision parts, such as cogs and gears, where even a slight warping can affect performance. To avoid this, engineers should focus on creating broad, strong structures that support the part, instead of relying on small edges to hold the part in place.
Another consideration that engineers need to take is the soft nature of aluminum. While this makes it easy to machine, it also means that aluminum has poor mechanical strength compared to other materials such as steel. As such, designs that rely on aluminum for structural support need to take this into account and potentially reinforce the material with steel or other strong materials.
The softness of aluminum also introduces problems when trying to create 3D structures using sheet metal. As the metal can be easily bent, it is possible for parts to warp and lose structural integrity during the manufacturing process. Thus, designs that need to use sheet metal should focus on welds and fittings that create strong structures, instead of relying on bends.
A major advantage of aluminum that engineers should take advantage of is its ability to resist rust. One common challenge faced with metal fabrication is the need to protect materials from the environment, especially if that environment is coastal or industrial. The rust-resistant properties of aluminum make it ideal for such applications, meaning that engineers should take advantage of this when designing parts for harsh environments.
However, aluminum is prone to corrosion (acid, alkali etc.), meaning that engineers should consider the environment that their parts will be in. For example, aluminum parts that make contact with acidic compounds will eventually break down, exposing underlying metal structures and resulting in a failed part.
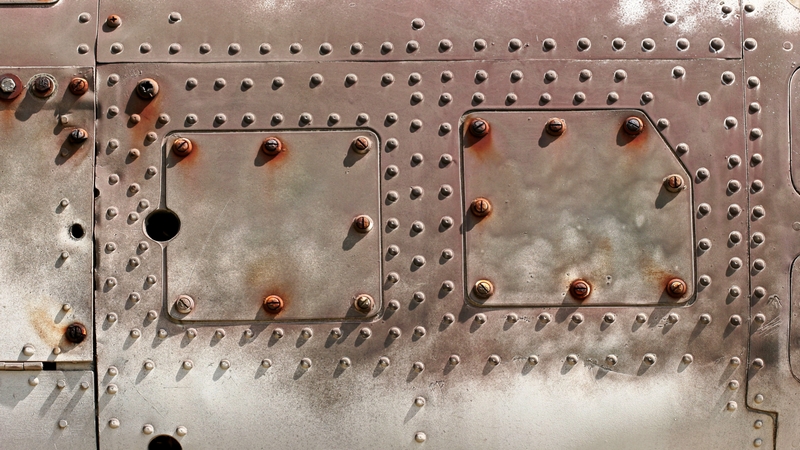
Question on using aluminum sheet metal in your next project
Does aluminum rust?
Aluminum doesn’t rust, but it can corrode depending on the environment it is in. The protective oxide layer that aluminium extrudes helps to prevent corrosion in most environments, but areas that are in close proximity to the sea as well as areas of high acidity can cause aluminum to corrode.
Is all aluminum the same?
No, aluminum comes in numerous material types, each with their own advantages and disadvantages. Some are ideal for basic commercial applications, while others are suited for aerospace and medical industries.
Is aluminum expensive?
Aluminum is one of the cheapest metals thanks to its ease of production, which involves direct electrolysis of its ores. The use of electricity to extract aluminium from its ore also means that aluminium is an ideal material for those looking to shift towards more environmentally friendly materials. However, some grades of aluminium can become expensive, and it is these expensive varieties that are mostly seen in aerospace and medical applications where strength to weight ratios are critical.
Is aluminium easy to machine?
Aluminium is one of the easier metals to machine thanks to its soft nature, making it cheaper to work with compared to steel. Its ease of machining also makes it ideal for recycling, and the many recycling options available for aluminium waste help to further reduce its cost. The machinability of aluminium also makes it suitable for block machining, and the numerous machining techniques available for aluminium include milling and CNCs. As such, aluminium offers engineers a low-cost material option that is easy to work with and recycle.