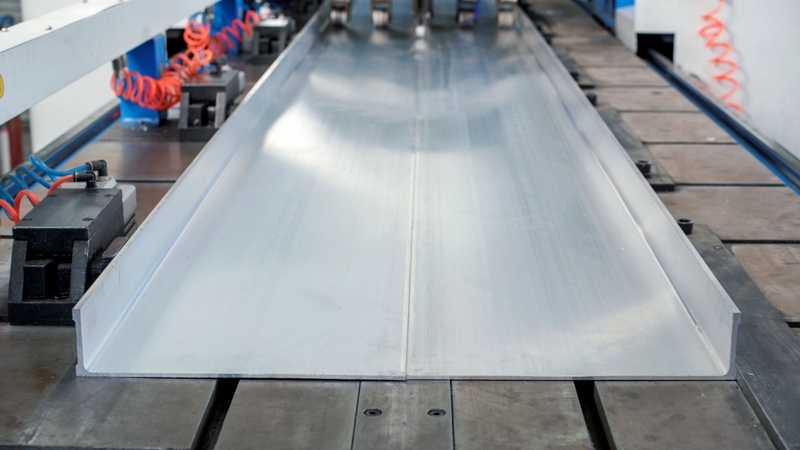
What is Sheet Metal Fabrication?
Sheet metal fabrication is a manufacturing process that utilizes sheets of metal to create a wide range of different parts and products. However, the term “sheet metal fabrication” specifically refers to the numerous manufacturing techniques used with sheet metals, including laser cutting, bending, welding, and forming. The sheet metal fabrication industry has a long and rich history dating back to the early days of metal working, and played a key role during the industrial revolution where large-scale production was needed for iron and steel.
Ponoko laser cutting services are primarily used for sheet metal fabrication with a wide range of different metal types available. Ponoko also offers a range of other services including metal bending, welding, and metal molding. Furthermore, Ponoko offers a range of different welding options including MIG, FIBER, and TIG, all of which are suitable for use with Ponoko laser-cut parts. The wide range of services combined with expert engineers enables Ponoko to tackle any metal fabrication project that customers may have.
Common Materials Used
When it comes to choosing the right metal for sheet metal fabrication, it is essential that only laser-safe materials are used. For example, highly reflective materials such as aluminum and copper cannot be laser cut using standard CO2 lasers as the reflected light can damage the laser itself. While these materials can be cut using fibre lasers, their high-reflectivity must first be removed either by engraving, using a rough finish to the material, or switching to a different wavelength of laser light.
The color of a metal can also be an important factor when choosing a suitable metal for laser cutting. While CO2 lasers can cut most metals, the resulting cut edge can experience discoloration depending on the extent of the burn from the laser beam.
The density of a metal can also influence its suitability for laser cutting. Generally speaking, denser metals are harder to cut through, and thus require higher-powered lasers. At the same time, denser metals also have greater tensile strength, meaning that they can be formed into thin sheets without cracking, thus making them easier to cut with a laser cutter.
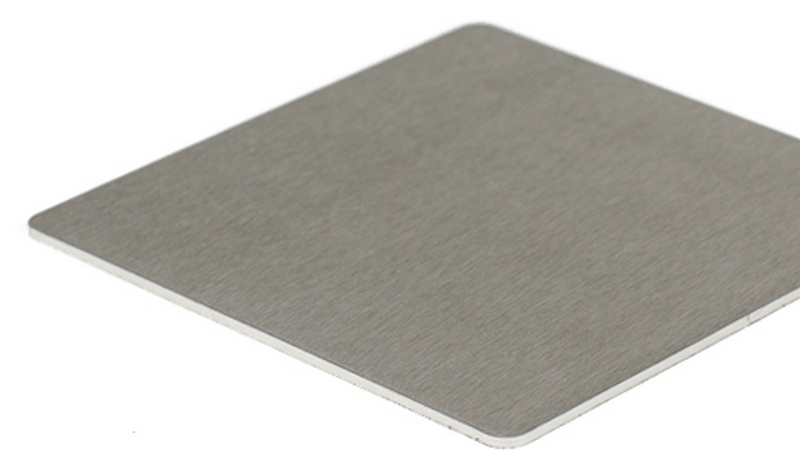
The tensile strength of a metal can also be an important consideration when choosing from different grades of a metal. For example, cold-rolled steel is stronger than aluminum, meaning that it can be formed into thinner sheets. However, cold-rolled steel is also more difficult to cut through, requiring higher-powered lasers.
The ability to form a material also plays an important role in sheet metal fabrication. For example, brass is an ideal material for decorative parts due to its ability to be easily engraved and its resistance to corrosion, but it is not ideal for structural parts as it is one of the weaker metals (when compared to steel).
As such, engineers need to take into account a wide range of characteristics when selecting metals for laser sheet fabrication, including thermal conductivity, ease of forming, laser cut edge finish, and laser cut edge strength. Some parts will require high thermal conductivity, while others will require ease of forming. The color and finish of the laser-cut edge can also be important, especially in decorative applications, while the strength of the the laser-cut edge can be critical in structural applications (as the heating from the laser beam can heat treat the edge).
Popular Sheet Metal Fabrication Methods
Sheet metal fabrication plays a central role in the manufacturing of many metal parts due to the ability to construct 3D structures from 2D sheets. By far one of the most popular methods for cutting sheet metal is laser cutters, as they are extremely precise, do not require tooling, are quick, and exert no mechanical force on the part being cut. This lack of mechanical force also means that laser-cut parts can immediately be used in products without the need for further processing, something which cannot be done with CNC machined parts.
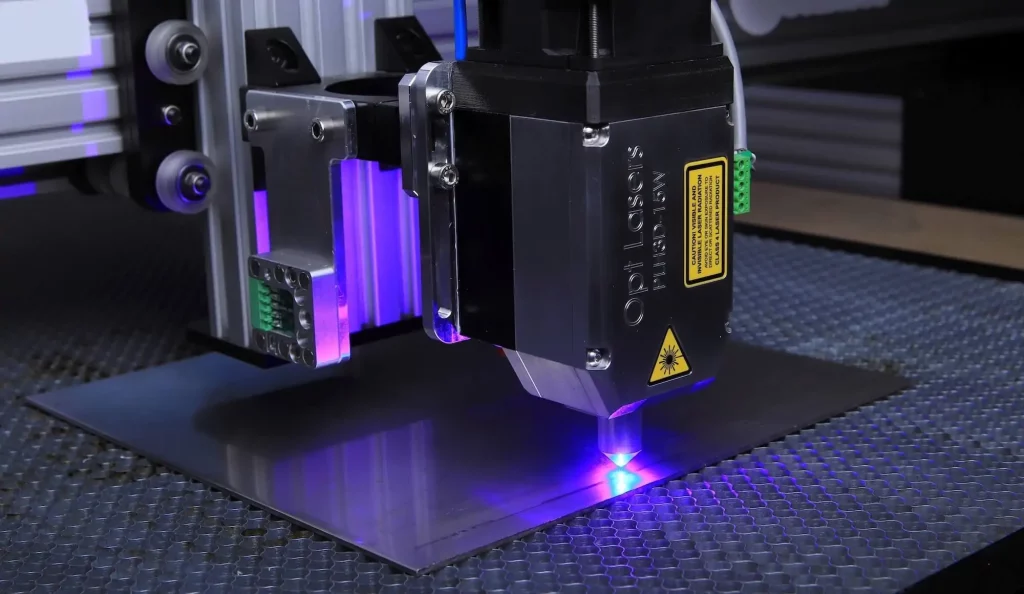
Other cutting methods do exist, with water jet cutters being ideal for cutting thick, thick metal. Their use of a high-pressure water jet allows them to cut through even the toughest metal, something which laser cutters generally cannot do. Plasma cutters are also able to cut through thick metal, and their use of a plasma stream allows them to cut through metal at extreme angles.
Sheer cutting is a fast process that can be used to cut large sheets of metal, but the inability to make cut-outs means that sheer cutting can only be used in applications where a part needs to be expanded into a sheet. For example, metal enclosures can use sheer cutting to expand a 2D metal shape into a 3D box, but a sheer cut-out is not possible.
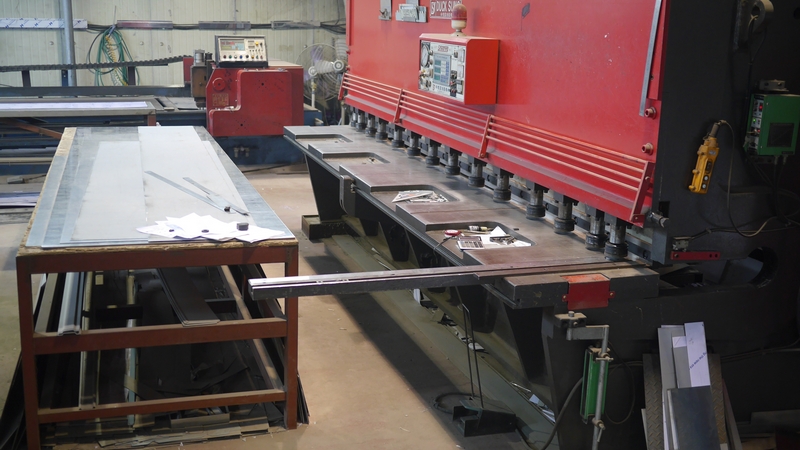
Bending is also a crucial stage in the fabrication of sheet metal parts as it allows for the creation of 3D shapes from 2D sheets via folds. While this can also be done with laser cutters, the use of a metal bending machine is far cheaper and faster, especially for large parts.
CNC milling is a method that can be used to create extremely precise parts, and their ability to cut any 2D shape means that they can be used in a wide range of applications. However, the slow nature of CNC milling makes it an expensive process, something which laser cutting can often do faster and cheaper.
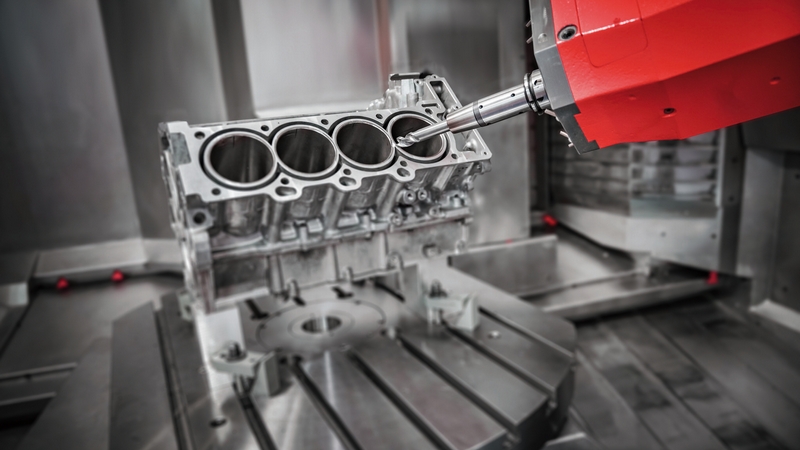
Overall, sheet metal fabrication is an essential step in the manufacturing of metal parts, and the various processes involved with sheet metal fabrication all play critical roles. Laser cutters are excellent for those needing precision parts that are fast to produce, while water and plasma jets are ideal for thick metal parts that need extreme force to cut through their metal stock. Sheer cutting is ideal for those needing to expand 2D shapes into 3D parts, bending is ideal for creating 3D parts via folds, and CNC milling is ideal for creating extremely precise parts.
How it Works (Step-by-Step)
- Stage 1 – Cutting
- Stage 2 – Deburing / Sanding
- Stage 3 – Bending
- Stage 4 – Cleaning / Finishing
- Stage 5 – Quality Inspection
The sheet metal fabrication process is a multi-disciplinary approach that takes a 2D design and turns it into a 3D structure. The first stage in this process involves taking a 2D sheet of metal and cutting it to size using various cutting techniques, including laser cutting and plasma cutting. If large parts are being fabricated, sheers can also be used to cut large sheets of metal into smaller parts.
After the parts have been cut to size, the resulting debris and burrs need to be removed. This is achieved with the use of deburring techniques, which also help to produce precision results. From there, the sheet metal can then be manipulated to shape, with bends being made in the metal to create 3D structures. The use of manipulative techniques allows for sheet metals to be folded without the need for welding, something which is especially advantageous for future designs that may need to allow for expansion and contraction.
Once the sheet metal has undergone bending, it is then moved onto the joining stage, where different sheet metals can be connected together. This is generally done via welding, but other techniques, such as riveting and bolts, can be used for specific designs.
The final stage in the fabrication process involves cleaning and finishing, where non-metallic debris is removed, and the surface of the metal is smoothed over. This allows for the part to be painted and decorated, as well as applying any other features that may be required.
Overall, the sheet metal fabrication process is a cost-effective method for producing high-quality metal parts that can be used in a wide range of applications, from automotive to medical devices. Its ability to combine both additive and subtractive processes makes it a unique method for building 3D metal structures from 2D sheets.
Key Takeaways
Sheet metal fabrication is a critical aspect of modern manufacturing that involves several key processes to convert sheet metals into various 3D structures. The term ‘sheet metal fabrication’ specifically refers to the numerous methods used with sheet metals, including laser cutting, bending, welding, and forming, to create 2D shapes that can eventually be combined to manufacture 3D structures.
Numerous sheet metals can be used in the fabrication process, with some of the most common including steel, aluminum, brass, and copper. While the choice of metal will often depend on the eventual application of the fabricated part (such as strength, malleability, and corrosion resistance), all of these metals can be manipulated using common fabrication techniques.
The first stage in sheet metal fabrication typically involves subtractive processes that remove excess metal from a sheet. For example, a metal plate can be cut into a specific shape using a laser cutter or a CNC machine to create a 2D part from a large sheet of metal. Other techniques, such as water cutting and plasma cutting, can also be used during this stage to cut out shapes from sheets of metal.
Once the parts have been cut out, the second stage involves manipulative processes that change the shape of the part without removing any material. One common manipulative technique used is bending, whereby the metal is made to fold at specific creases. This is often used to create 3D shapes from 2D parts, such as boxes, brackets, and lids.
The third and final stage in sheet metal fabrication often involves additive processes that join multiple parts together to create a final 3D structure. The most common technique used during this stage is welding, whereby two or more parts are melted together under high temperature to create a strong bond. Other techniques, such as bolts and rivets, can also be used to join parts together, and in some cases, soldering can be used to connect electrically conductive parts.
Overall, sheet metal fabrication is an essential manufacturing step that plays a critical role in the production of a wide range of metal parts found in many different industries. Its ability to start with basic 2D shapes and then manipulate these into complex 3D structures makes it a highly efficient process that offers engineers a low-cost manufacturing option for prototypes and mass production alike.
Why Choose Ponoko for Your Sheet Metal Fabrication Needs
When ordering sheet metal fabricated parts, engineers have more than enough stress to deal with, whether it is a prototype or a scaled-up production run. The very act of using a manufacturing service means that engineers have to entirely trust the manufacturer to produce parts to a high degree of quality and precision.
For example, materials such as steel and aluminum exhibit a wide range of properties, including density and tensile strength, and these can vary between different manufacturers. As such, Ponoko goes out of its way to source high-quality materials from reputable manufacturers, ensuring that the characteristics of any given material are consistent. The precision and accuracy offered by Ponoko ensures that all manufactured parts perform as expected, and the lack of variation in parts ensures that designs are consistent, even when ordering large quantities. In fact, Ponoko is so confident in the quality and precision of its manufactured parts that all parts come with a 365-day money-back guarantee.
With over 2 million sheet metal parts manufactured for 33,000+ customers, Ponoko has proven itself as a high-quality sheet metal fabrication service, and its 99.7% part precision record demonstrates this. Whether a single prototype or ten thousand market-ready parts are being ordered, Ponoko provides engineers with the consistency and precision they need.
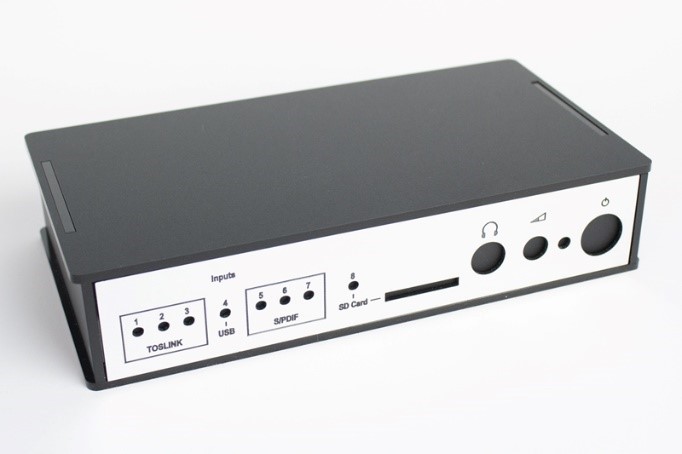