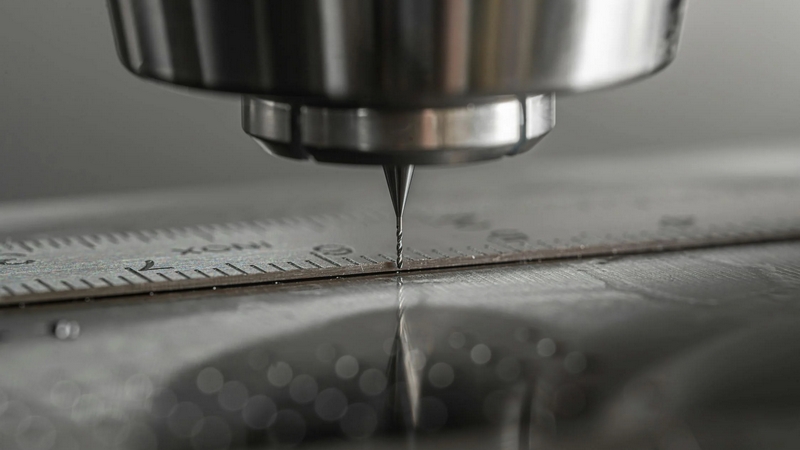
What is a CNC Router?
A CNC router, or computer numerical control router, is an advanced machine engineered specifically to carve, engrave, and shape sheet material into intricate designs and patterns. This type of CNC machine is particularly adept at cutting through materials such as wood, composites, aluminum, steel, plastics, and even glass with precision and speed. The unique capability of a CNC router lies in its design to handle large panels of material, making it an indispensable tool in various manufacturing processes where sheet materials are predominant.
The core mechanism that enables a CNC router to perform these tasks is its routing tool, which is essentially a high-speed spindle that can spin the cutting tool at various speeds, typically thousands of revolutions per minute. This spindle is mounted on an XY gantry system, allowing movement along both the X (horizontal) and Y (vertical) axes. The precise control of the routing tool’s path is achieved through computer programming, which directs the gantry to move the tool along specified coordinates, thereby cutting the material into the desired shape.
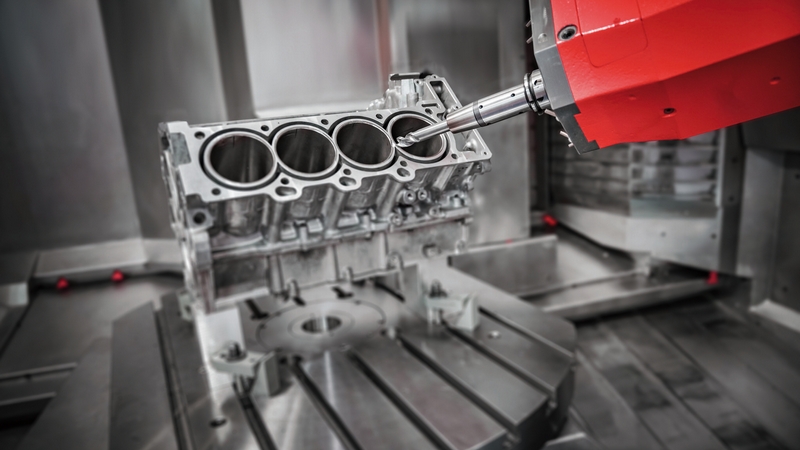
Although primarily designed for two-dimensional cutting tasks, CNC routers possess the capability to perform three-dimensional cutting operations. This versatility is extended by some models that include a rotation stage, enabling the fourth axis of motion, thereby allowing for the creation of more complex geometrical shapes and patterns. This additional axis can rotate the workpiece for multi-angle cuts or even full 360-degree rotation, which is ideal for intricate three-dimensional sculpting.
CNC routers are particularly prevalent in industries where precision is crucial. The printed circuit board (PCB) industry relies heavily on these machines to route out intricate circuits from copper-clad laminates. The precision cutting ability of CNC routers ensures that the delicate paths of PCBs are accurately shaped, thereby maintaining the functionality of the electronic devices they are used in. Similarly, the prototyping industry benefits greatly from CNC routers. Whether it’s creating detailed architectural models or functional automotive components, CNC routers facilitate rapid prototyping of parts by allowing designers and engineers to quickly produce physical samples from digital designs.
In addition to their primary roles in specific industries, CNC routers are also versatile enough to be used in sign making, furniture design, and even art installations. By providing both speed and precision, these routers enable creators and manufacturers to not only work efficiently but also push the boundaries of design and creativity.
Overall, the CNC router stands out as a pivotal tool in modern manufacturing, combining advanced technology with versatile functionality to meet the growing demands of various industries. Its ability to meet the needs of precision and mass production makes it an essential component in today’s manufacturing landscape.
How Does a CNC Router Work?
At the heart of a CNC router is a three-axis gantry system paired with a powerful router. This gantry system allows the router to move along three axes: the X-axis (left to right), the Y-axis (front to back), and the Z-axis (up and down), enabling it to manipulate materials with precision and flexibility. The router itself is typically powered by a direct current (DC) motor, but can use multi-phase motors for more powerful applications. Attached to this motor is a router bit, which is the most critical component of the machine. Unlike a standard drill bit designed primarily to create holes, the router bit includes special blades along the sides. These blades allow the bit to cut not only downwards but also laterally, carving intricate patterns and shapes into the material being worked on.
To achieve the desired effects on various materials, these router bits are spun at extremely high speeds, often exceeding 10,000 revolutions per minute (RPM). The exact speed, however, can vary depending on the type of material being cut and the feed rate, or the speed at which the material is fed through the machine.
Central to the operation of CNC routers are the motors that drive the movement of the router along the gantry system. These motors are typically stepper motors, known for their precision in control. Stepper motors operate under numeric control, meaning they adjust their position by following specific numeric commands. These commands are communicated to the stepper motors through electrical pulses, and a computer generates these pulses based on detailed numeric files known as NC (numeric control) files. These files contain coded instructions on how the machine should move to achieve the desired design or cut. The pulses dictate not only the direction and extent of each movement but also the speed at which these movements should be executed.
To interpret and execute the instructions contained in NC files, CNC routers are equipped with specialized CNC software. This software reads the NC files, translates the coded instructions into actionable commands, and sends the corresponding pulses to the motors. This seamless integration of hardware and software allows CNC routers to produce complex and precise cuts, making them indispensable in settings where accuracy and repeatability are critical.
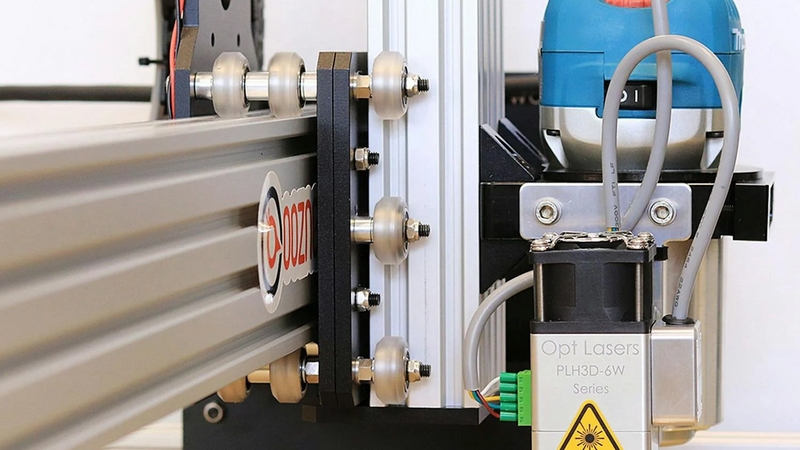
What Controls a CNC Router?
The operation of a CNC router is a complex process that requires a high degree of precision and accuracy. The first stage involves the use of a computer to interpret a design file and determine the tool paths needed to produce the design. This stage is critical as it directly affects the quality of the final product and the efficiency of the production process. Once the tool paths have been determined, the CNC router then reads these tool paths and begins to produce the design. During this stage, the router uses a variety of different control systems to move the toolhead along two axis as well as controlling the feed rate of the toolhead.
The control systems used by CNC routers can either send pulse width modulated signals to stepper motors or use direct drive motors that accept digital commands to move the axis by specific amounts. In either case, the conversion of digital information into physical motion is critical for producing a high quality product. Furthermore, the use of micro stepping allows for highly controlled movement of the toolhead over the workpiece, and the use of gear reduction helps to provide a high degree of torque.
While CNC routers can operate entirely automatically, they are often used in conjunction with human operators who are responsible for loading and unloading workpieces as well as performing quality control. The use of human operators helps to reduce the cost of operation as well as provide a level of flexibility to the production process. However, this also means that CNC routers are less efficient than they can be, and the use of manual intervention increases the cost of production.
Benefits of a CNC Router
Computer Numerical Control machines represent a significant manufacturing technology with their ability to provide unmatched precision and accuracy in part and component production. The use of numerically controlled axes guides tools such as drills and lathes with extreme precision, and the use of engineered bits allows for cutting and shaping materials down to the micron level. Furthermore, the use of negative feedback loops ensures that the machine produces parts to the desired specification by making adjustments based on output measurements.
One of the major advantages of CNC machining is its ability to adapt to new designs without the need for extensive tooling changes. Unlike other manufacturing processes, CNC machines can be reprogrammed with ease and speed, reducing tooling costs. This makes CNC ideal for custom designs and small batch productions, something which injection molding and 3D printing cannot compete with. While 3D printing does not require molds, it is an extremely slow process and the parts it produces are nowhere near as precise as those made using a CNC.
CNC machines are also able to produce parts to production standards from prototypes, something which cannot be done with 3D printers. The parts produced by a CNC are also a more accurate representation of the final part as compared to 3D printed parts. However, CNC parts can be expensive to produce due to the use of bits, but the low cost of CNC machining compared to injection molding makes it a viable option for low-volume production.
The ability of CNC machines to produce prototypes accurately also makes them ideal for testing and evaluation. The parts produced by a CNC can be used in real-world applications and environments to test a design for its strength, durability, and performance. This helps engineers understand how their design will behave in the real world, and this can be especially important for products that are expected to undergo rigorous use and abuse.
In the case of custom designs, CNC machining is the only practical manufacturing method available. Custom designs will require custom molds, and these are only economical when manufacturing parts in the millions. 3D printing can be used for custom designs, but the parts it produces are not suitable for mass production, and the precision offered by 3D printers pales in comparison to CNC machines.
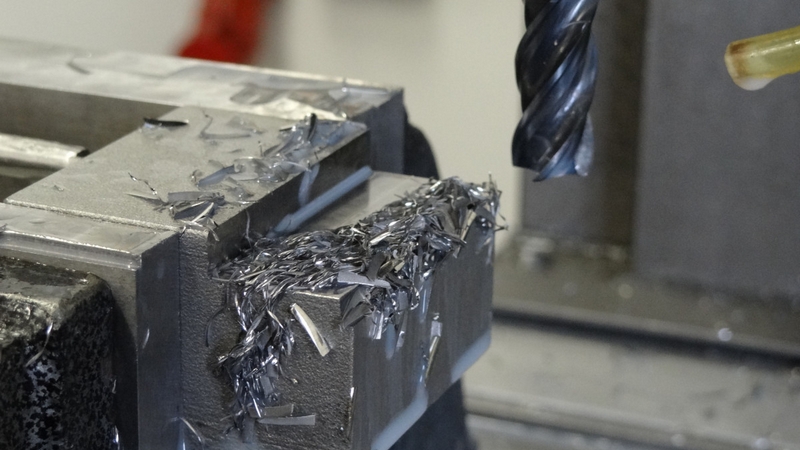
Specific Parts of a CNC Router
At the center of a CNC router is the bed, which serves as the platform where materials are placed and securely held during the cutting process. Stability and flatness of the bed are crucial for precision, as any irregularities can lead to errors in the final product. Materials such as wood, metal, or plastic are typically fixed onto the bed using clamps or vacuum hold-down systems.
The movement of the CNC router is controlled by motors, commonly stepper motors, which are responsible for moving the machine along the designated axes. These motors are precisely controlled to ensure that the router moves accurately according to the design specifications inputted into the computer. Each axis of the machine—X, Y, and Z—has its own motor, enabling the router to create complex three-dimensional shapes.
Mounted to the Z-axis is the router itself, which includes a powerful motor equipped with a routing bit. This bit spins at high speeds and carves into the material, guided by the design sent from the computer. The choice of routing bit can vary depending on the material being cut and the intricacy of the design, ranging from fine tips for detailed work to larger cutters for rough shaping.
Traditionally, CNC routers have used threaded machine screws on each axis to convert the rotational movement of the motors into linear motion. However, advancements in technology have led to the adoption of linear motors in some modern CNC machines. Linear motors offer smoother and faster movement as they eliminate the need for threaded screws, reducing mechanical wear and maintenance needs.
Another essential component of CNC routers is the homing pad, which is used to accurately position the router bit at the start of each new project. This ensures that the bit is correctly referenced, aligning it precisely with the coordinates of the design file. This referencing is critical for maintaining consistency, especially when producing multiple parts of the same design. To prevent the machine from moving beyond its operational limits, limit switches are installed on each axis. These switches automatically halt the movement of the router if it reaches the edge of its working envelope, protecting the machine from potential damage caused by collisions or over-travel.
The controller acts as the intermediary between the CNC router and the computer. It interprets the signals from the computer and drives the motors accordingly. This component is connected to sensors that monitor the status of the router and its axes and also includes a user interface for parameter settings and monitoring the status of the router. The use of a controller allows for computer control and remote operation of the CNC router.
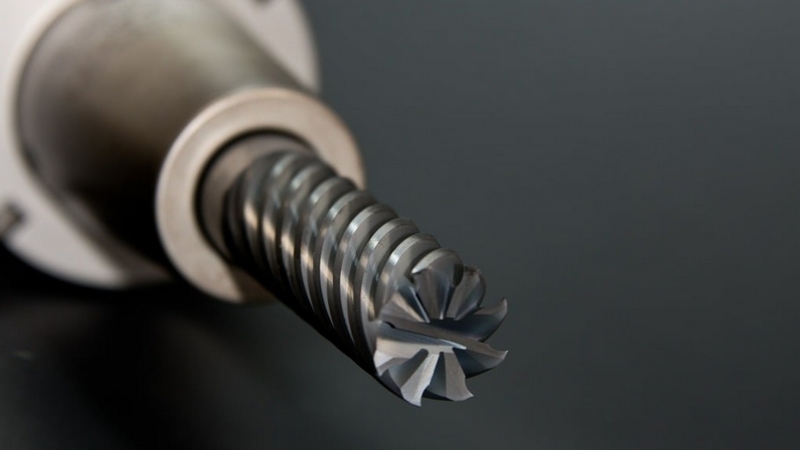
Materials That Can Be Cut on a CNC Router
CNC routers are highly advantageous in modern manufacturing and design workshops due to their ability to work with a wide range of materials, including metals and plastics, with great precision. Unlike traditional manual cutting tools, CNC routers use computerized controls to interpret designs and cut materials according to specified dimensions, making them an essential tool for both prototyping and mass production. Their versatility also enables CNC routers to be used in various industries, ranging from automotive to consumer electronics, and their precision makes them suitable for both high-quality prototypes and mass-produced products.
When it comes to metals, CNC routers are particularly effective, as they can cut metal sheets into complex patterns and shapes with great accuracy, which is essential for precision parts. Furthermore, the cost-effectiveness of CNC routing makes it a suitable method for custom parts and prototypes, unlike other metal shaping processes such as 3D metal printing, which can be expensive due to the cost of printers and materials. However, CNC routers can also be used with plastics, where their ability to create intricate 3D shapes makes them ideal for prototyping and mass production.
Wood is another material that benefits from the precision and accuracy of CNC routers, and the ability to create structural parts enables CNC routers to be used in a wide range of applications, from furniture to architectural elements. However, it is essential that CNC routers are dedicated to specific materials to prevent contamination and damage, as metal fragments can embed in wood and vice versa.
While CNC routers offer many advantages, one technical aspect that must be considered is the need to secure workpieces during the cutting process. This is achieved using tabs that prevent the part from moving during routing, which could lead to inaccuracies or damage. After the routing process, these tabs need to be removed manually, which is an additional step in the finishing process, but this is essential to maintain the integrity and precision of the final product.
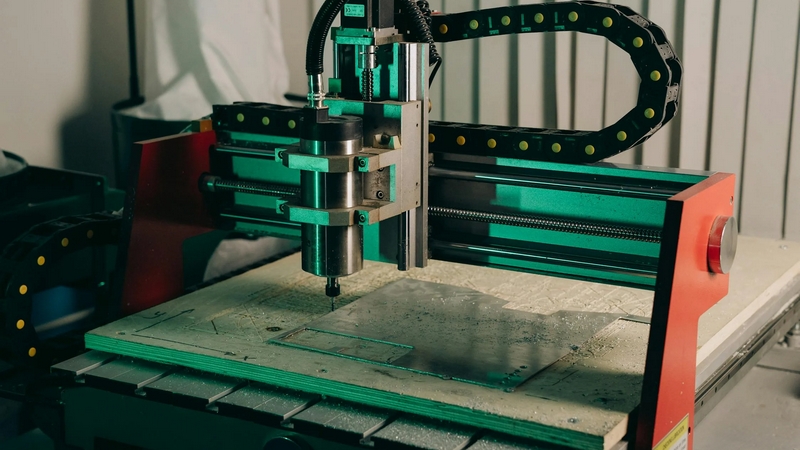
Key Takeaways
CNC routers are often criticized for their slow operation but are highly valued for their exceptional precision. Their precision is unmatched in many industries and makes them a preferred choice when creating intricate designs whether it’s wood carvings or components for aerospace. While speed is not essential for CNC routers, their slow operation is a small trade-off for the accuracy and quality of the output. These machines follow programmed instructions meticulously to cut and shape material with a level of accuracy that manual processes cannot match.
One of the major advantages of CNC routers is their ability to handle a wide range of materials. Whether it’s wood, plastics, foams, or even metals, CNC routers can efficiently manipulate these materials into the desired shape. This ability is particularly beneficial for industries that deal with a variety of materials including automotive and furniture manufacturing. Furthermore, the minimal tooling requirements of CNC routers make them cost-effective to run as tool changes are rarely needed. If tools are needed, they can easily be interchanged due to the non-dedicated nature of CNC router bits.
While CNC routers are capable of 4-axis operation, most applications only require 3-axis. These three axes provide sufficient flexibility for manufacturing and prototyping, and the use of 4-axis is generally only required for specialized applications. The ability to cut in all 3 dimensions also makes CNC routers ideal for 3D carving as well as 2D cutting.
CNC routers are also essential prototyping tools as they can rapidly produce functional prototypes. Engineers and designers can take advantage of the high precision and quality of CNC routers to produce prototypes that closely resemble the end-product. The ability of CNC routers to produce high-quality parts means that prototypes are robust enough to be used in testing and can even be used directly in mass production. This reduces the cost and time associated with prototyping and designing.
CNC routers may be slow, but their precision, versatility, and ability to produce high-quality parts make them essential in both prototyping and mass production. Whether creating a wooden box or a metal bracket, CNC routers offer engineers and designers a reliable and efficient machining solution.
Why Choose Ponoko
Ponoko is a manufacturing service that removes the complexities associated with CNC routing, allowing engineers and product developers to focus on what they do best; designing and innovating. Unlike other manufacturing services, Ponoko has years of experience with over 33,000 customers and 2 million products produced, ensuring that all aspects of a product’s life cycle, from prototyping to mass production, are handled by experts.
The technical aspects of product manufacturing can be complex, including setting up CNC machines, ensuring precision cuts, and maintaining equipment. Ponoko takes all of this into consideration, so customers do not need to invest in and manage complex machinery. Instead, Ponoko leverages its expertise to offload these technical aspects, allowing customers to focus on design and product development.
Ponoko’s services cater to a wide range of production needs, making it an ideal partner for engineers and designers. The manufacturing process is streamlined, ensuring customers can quickly move from prototypes to mass production. The collaboration between Ponoko and its customers enables efficient manufacturing solutions that benefit both parties, allowing for a smoother transition from concept to market-ready product.
The ability to outsource manufacturing to Ponoko also reduces the financial burden associated with product development. The cost of purchasing and maintaining CNC equipment, as well as material expenses, can be prohibitive for small businesses and individual entrepreneurs. With Ponoko, these costs are absorbed by Ponoko, allowing customers to allocate their resources more effectively.
Ponoko’s commitment to quality ensures that all products meet strict standards, regardless of the order size. This means that both prototypes and mass-produced items receive the same level of precision and care, offering a seamless transition from one stage to the next. The focus on quality and efficiency enables Ponoko to provide competitive pricing, making CNC manufacturing services accessible to all.
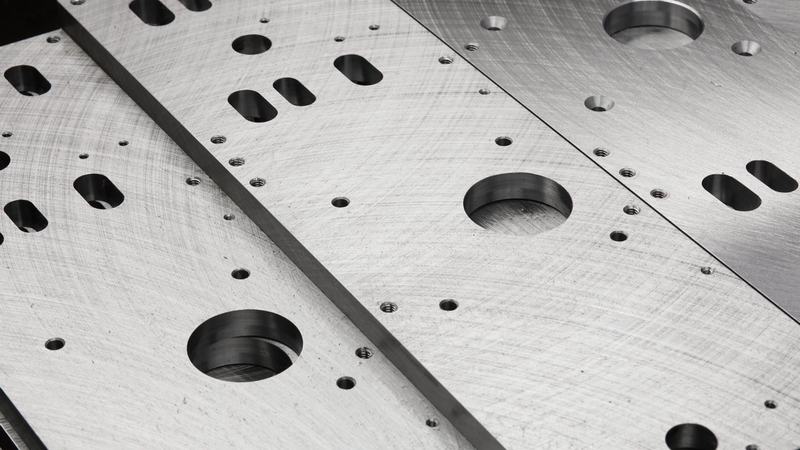
The use of CNC routing in combination with laser cutting provides customers with a wide range of materials and technologies, offering flexibility in product design. The precision and accuracy of CNC machining ensure that the final products conform to tight tolerances and meet high standards of quality. The ability to produce both prototypes and mass-produced items using the same process also enables a product to retain its aesthetic consistency, which is particularly important for branding and recognition.
Ponoko’s commitment to innovation and technology enhances the product development process. The integration of cutting-edge equipment, such as laser cutters and CNC machines, enables fast and accurate production. The use of automation and machine learning algorithms also improves the efficiency of the manufacturing process, reducing the time taken to produce products and enhance the overall customer experience.
By partnering with Ponoko, engineers and product developers can leverage a wealth of expertise and resources to bring their innovative ideas to life. The collaboration between Ponoko and its customers facilitates a smoother transition from concept to market-ready product, benefiting both the creators and the end-users. The focus on quality, precision, and efficiency ensures that the final products conform to high standards, enhancing the customer experience and driving innovation in the product development sector.