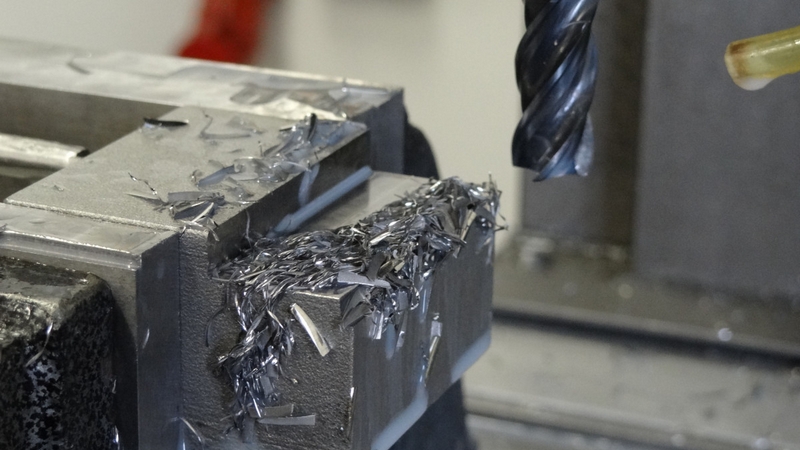
What is As-Machined Finish?
When a part is manufactured, it rarely comes out of the production line fully ready for use. Additional finishing stages are usually required to enhance the part’s functionality and aesthetic appeal.
For example, certain finishes can make a product waterproof, ensuring that it remains functional and doesn’t suffer damage when exposed to moisture. This is particularly important in industries such as electronics, where moisture can lead to short circuits and other malfunctions. Other finishes are designed to protect parts from oxidation, which can otherwise weaken materials and reduce their lifespan, and such protection is essential for parts used in automotive and aerospace industries.
Finishing processes also play a key role in the appearance of a part, with common techniques including sanding, polishing, and painting. Anodizing is another common finish that not only enhances the appearance of a part but also provides corrosion resistance. However, some parts may not require additional finishing, and in these cases, the As-Machined finish can be beneficial.
This type of finish retains the appearance of a part after machining, including tool marks and minor imperfections, and is often chosen for parts that do not require a high degree of aesthetics or where additional finishes do not significantly contribute to the part’s function. The As-Machined finish can help to reduce costs and shorten production times compared to other finishes, making it a cost-effective option for mass production.
Design Considerations
As parts are manufactured, they can go through various processes to enhance their surface finish, including grinding and polishing. However, it is also possible for parts to be sold with an as-is finish which means that no additional surface treatments have been done on the part. This type of finish is advantageous as it helps to keep costs down as well as enabling engineers to utilise unaltered parts in critical applications where material properties are not affected by additional processing stages.
But parts that have an as-is finish require engineers to consider the potential effects of oxidation. Unlike plastic and stainless steel, pure metal such as copper and steel are highly vulnerable to oxidation which can lead to the formation of rust and patina. Such oxidation not only affects the appearance of the part but also has potential adverse effects on the part’s mechanical and electrical properties. For example, oxidation can affect electrical conductivity and increase the surface resistance of the material.
The oxidation process can be accelerated in the presence of moisture and air, meaning that engineers need to take into account the environment in which the part will be used as well as considering how the part may be stored. If, for example, steel parts are to be stored outdoors, it is essential that they are coated with a rust inhibitor to prevent early oxidation.
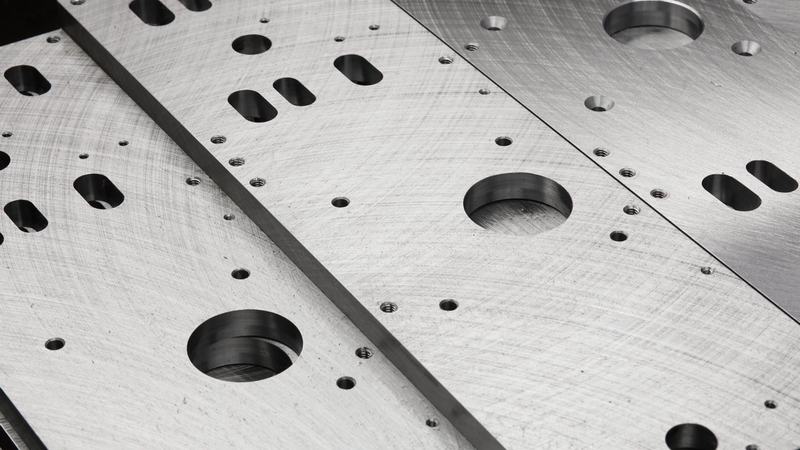
Internal surfaces of metal parts can also be problematic as oxidation can form on the inside of a part. Such oxidation can lead to blockages in fluid flow as well as affect the mechanical properties of the part. For example, oxidized steel can lead to a part being less strong and more brittle.
As such, it is crucial that engineers carefully consider the environment and potential uses of a part with an as-is finish. The as-is finish of a part should also be documented to ensure that engineers are aware of the finish and its implications. Additionally, engineers should also consider the potential for burrs and sharp edges to form on metal parts, especially those made from soft metals such as aluminum. Such edges can cause mechanical failure or injury.
Another challenge faced with as-is metal parts is the presence of swarf which can remain in drilled holes. This leftover material can interfere with further manufacturing processes as well as the final application of the part. For example, swarf in an engine block can lead to oil leaks from passages.
Finally, as-is parts can also have visible marks from the machining process which may or may not be acceptable to an engineer. Such marks can include grooves, scratches, and indentations which are a result of tool paths used by CNC machines. While these marks are perfectly normal, they may not be suitable for all applications, especially those involving aesthetics.
Reasons to Leave a CNC Piece As-Machined
Parts that are destined for further modifications such as electroplating benefit from not having a pre-applied finish, as such a finish can interfere with the adhesion and quality of the electroplating.
The cost implications of finishing a part can also be significant, and in cases where appearance is not a factor (such as internal components), the cost savings from not finishing a part can be substantial. Some designs require parts to interact with their environment in a specific way, and in these instances, an unfinished part is essential.
Rapid prototyping can also take advantage of unfinished parts as the aesthetic aspects of a part are not important in prototypes. Finally, companies with proprietary finishing technologies can utilize unfinished parts to apply their own specialized finishes in-house, ensuring control over the quality and finish of their parts.
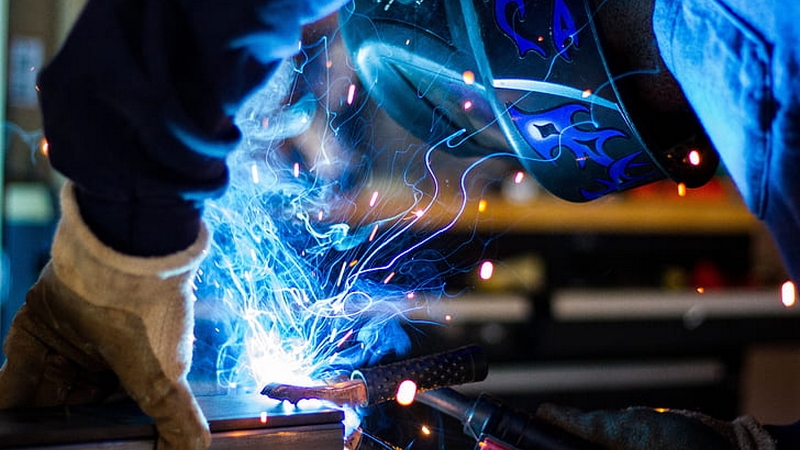
Key Takeaways
When discussing surface finishing in manufacturing and production, the term as-is surface finishing refers to a scenario where the surface of a manufactured part is left in its natural state post-production, without undergoing any additional processes to enhance its appearance or texture. This means that the part retains any marks, blemishes, or irregularities that were present as a result of the manufacturing process, such as those from machining, casting, or 3D printing. While as-is surface finishing might not be ideal for aesthetic applications where a smooth, uniform appearance is crucial, it serves well in scenarios where functionality and cost-effectiveness are more important than visual appeal.
As-is finishes are also suitable for structural parts that will eventually be hidden from view in the final product, such as internal components in machinery or the structural framework inside a larger appliance. However, there are certain materials and applications for which as-is finishing might not be suitable, including materials prone to oxidation and harsh environmental conditions.
Despite these potential drawbacks, there are many applications where as-is finishing is more than adequate, especially during early product development stages or for less critical components. Evaluating the functional requirements and environmental conditions to which a part will be exposed can help in making an informed decision about the necessity of further finishing, and this approach can help to reduce costs and streamline manufacturing processes. Overall, as-is surface finishing is not for everyone, but for many applications it presents a cost-effective option that is quick and easy to implement.
Why Choose Ponoko Finishing Services
The process of manufacturing a part is often plagued with numerous potential issues and challenges that can arise from the initial design phase to the final output. For example, miscommunications in specifications or inaccuracies in machining can lead to defects in the part, while poor material selection can result in parts that fail under stress. Surface finishes are also critical, especially for aesthetics and performance, but not all materials are compatible with all finishes, and applying finishes incorrectly can have negative consequences.
Understanding the interactions between materials and finishes is essential, but this knowledge is not widely available to engineers. This is where Ponoko can be highly beneficial; our years of experience in manufacturing gives us a deep understanding of the manufacturing process and the subtleties of different materials and finishes. This expertise allows our engineers to guide customers on how to achieve the best results for their project, ensuring that the desired outcome is achieved.
Our reliability and track record further demonstrates our capabilities as a manufacturer. With over 33,000 customers and 2 million parts manufactured, we have the expertise and resources needed to handle any manufacturing demand, whether it’s a prototype or a large-scale production run. The ability to deliver high-quality parts consistently instills trust in our customers, especially for critical and complex components, making us a trusted choice for engineers.
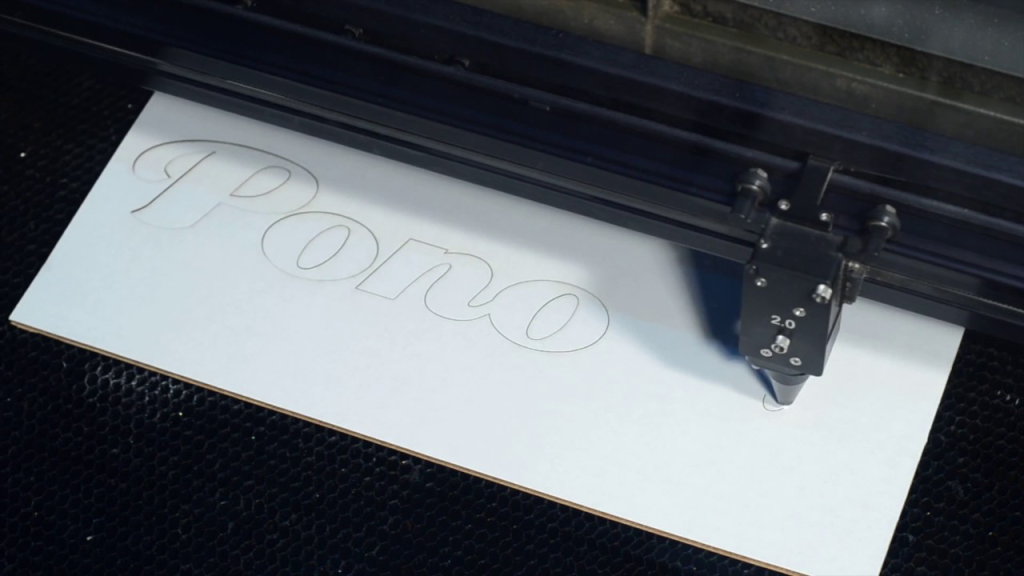