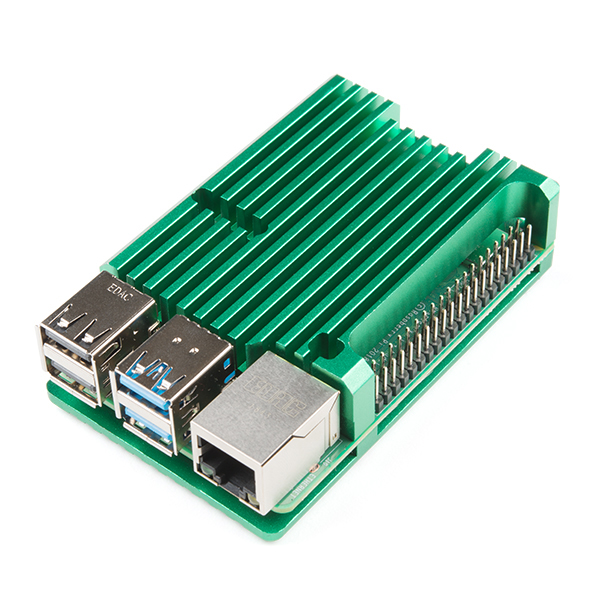
What is Anodizing?
Anodizing is a specialized electrochemical process that converts the surface of metal into a decorative, durable, and corrosion-resistant anodic oxide finish. Primarily used on aluminum, anodizing can also be applied to other metals such as titanium and zinc, and the resulting oxide layer fully integrates with the underlying substrate, making it impossible to chip or peel.
The primary function of the anodic layer is to protect the base metal from various forms of corrosion. Naturally, aluminum oxidizes when exposed to the atmosphere, but the anodizing process thickens this layer significantly, making it far more resilient to environmental factors such as moisture and salt. This makes anodized metals highly resistant to corrosion, explaining their widespread use in industries such as aerospace, automotive, and construction.
Anodizing also enhances the aesthetic appeal of metal parts with the ability to infuse colors into the anodic layer prior to sealing. The resulting finish is vibrant, glossy, and long-lasting, making anodized components popular in consumer electronics and architectural applications where appearance and durability are essential.
Additionally, the anodic layer offers electrical insulation properties, making anodized aluminum ideal for applications requiring electrical isolation. This is particularly crucial in the electronics industry, where components need to be insulated from each other to prevent electrical shorts, and in applications involving electrical housings and enclosures, where safety and functionality are paramount.
How Does it Work?
Before the anodizing process can begin thorough preparation of the part is crucial. The initial step involves sanding the surface to remove any irregularities and smooth the metal. This is followed by a chemical stripping or pickling process to remove any old coatings or oxides. The part is then cleaned to eliminate any residual grease dirt or impurities ensuring that the anodizing process is uniform and consistent.
Once the part is fully prepped it is submerged in a tank containing a strong acid (typically sulfuric acid) which acts as the electrolyte. The part is then connected to the positive terminal of a power source effectively making it the anode in the electrical circuit. Two other plates, usually made of lead or aluminum, are placed in the tank and connected to the negative terminal of the power source serving as cathodes.
When the power source is turned on an electric current passes through the electrolyte and oxygen ions are released from the acid. These oxygen ions combine with aluminum atoms to form an aluminum oxide layer which is an integral part of the metal surface unlike paint or plating. The molecular bonding that occurs during anodizing creates a finish that is much more durable and resistant to corrosion. This oxide layer significantly enhances the hardness and wear resistance of the metal making it suitable for high-performance applications. Furthermore the porous nature of the layer allows for dyeing which is how anodized parts can have a wide range of colors. The anodizing process therefore not only enhances the aesthetic appeal of metal parts but also provides a layer of protection and durability.
The anodizing process can be stopped and checked for uniformity and then submerged in a dye of choice. After the anodizing process is complete the part is sealed in a hot bath of boiling water to prevent oxygen from getting to the surface of the anodized layer. This prevents the natural oxidation of the aluminum which would otherwise see discoloration of the anodized layer.
What Is It Used For?
To start, the oxide layer formed through anodizing is highly resistant to corrosion, and as such, is ideal for parts that expect to be exposed to moisture and salt as well as those that may rust such as automotive parts.
Anodizing also provides protection against additional oxidation that can damage the underlying metal. The resulting oxide layer is uniform in thickness and adheres well to the metal surface, and this uniformity and adherence make it highly effective at preventing oxidation.
Anodizing can also be used to improve the functional properties of a part. For example, heat sinks used in electronic devices can be anodized to improve their ability to dissipate heat. The anodized surface is able to release heat more efficiently which helps to prevent overheating of components and improve the overall performance of the device.
Aesthetic enhancements can also be realized with anodizing. The thickness of the oxide layer can be controlled to produce a wide range of colors on metal parts without the need for painting or other coloring methods. This is particularly beneficial for industries such as consumer goods where both durability and aesthetics are important.
Finally, the porous nature of the anodized layer allows for dyeing before sealing which can be used to create highly coloured, long-lasting finishes. This is commonly seen in industries such as automotive and architecture where both durability and aesthetics are essential.
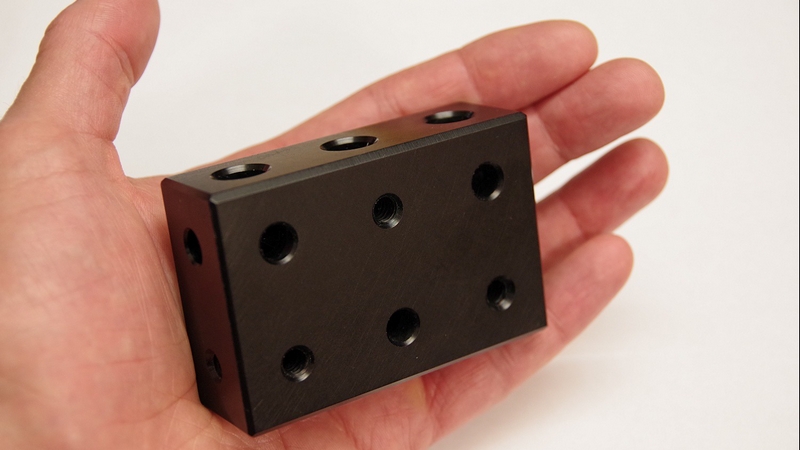
What is the Importance of Anodizing?
Anodizing stands out in the manufacturing industry due to its ability to enhance the natural properties of metals. For one, the inherent strength and longevity of anodized products are significant advantages.
During anodizing the metal surface is transformed into a hard layer of oxide which is fully integrated with the underlying substrate. This means it cannot chip or peel away unlike paint or coatings which can deteriorate or flake off over time. This molecular integration ensures that anodized finishes are highly durable and can withstand harsh environmental conditions without degrading. This makes anodizing an excellent choice for applications that require a long-lasting finish such as in aerospace components, architectural facades and various outdoor equipment.
Furthermore, anodizing is highly cost-effective, and can be used for the coloring of metal without the need for painting or additional coatings, which not only reduces production costs, but also enhances the metal’s aesthetic appeal and increases its resistance to corrosion. This is particularly beneficial for consumer goods and architectural elements where both appearance and performance are critical.
Environmentally, anodizing is a relatively benign process compared to other metal finishing techniques. The primary chemical used in anodizing is sulfuric acid, which is used to create the anodic oxide structure. Despite the strong pH of the anodizing solution, it does not produce harmful environmental by-products. The only by-product of the anodizing process is oxygen, which is released at the anode the part being anodized, thus posing no significant environmental threat.
Additionally, the solutions used in anodizing tanks can be treated and neutralized more easily than those used in many other industrial processes. Once the anodizing process is complete the acidic solution can be neutralized with a base such as sodium hydroxide to a safe pH level before disposal. This ability to neutralize the solution helps in minimizing the environmental impact of the anodizing process making it a more sustainable choice in metal finishing.
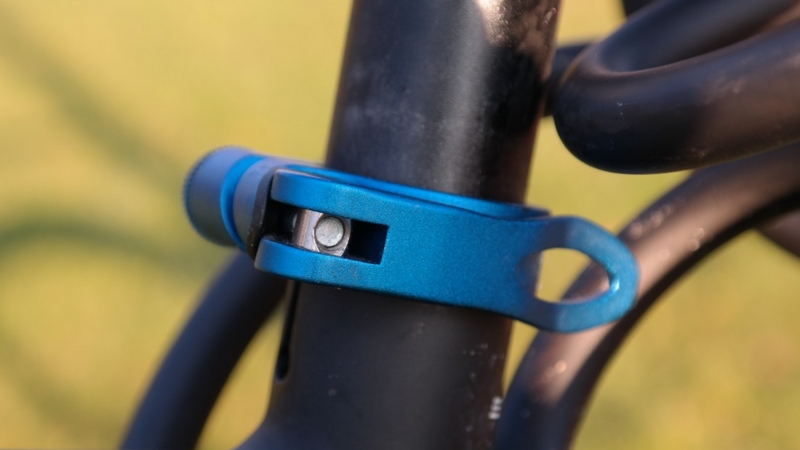
Key Takeaways
Anodizing is a specialized process that enhances the natural qualities of non-ferrous metals such as aluminum and titanium through the use of electrolysis. One of the primary advantages of the oxide layer formed during anodizing is its resistance to corrosion. This makes anodized metals ideal for use in environments that may be prone to moisture or chemical exposure such as automotive and marine components. The layer resists rust as well as wear and tear meaning that it can be used to protect structural components in applications that require strength.
The layer produced by anodizing also has non-conductive properties which makes it ideal for use in electrical applications. The high electrical resistance of the layer prevents heat build-up and also prevents sensitive electronic components from being shorted. As such, anodized aluminum is commonly found in the electronics industry.
Anodizing is also a cost-effective process that is environmentally friendly meaning that it is an ideal process for large-scale production. The process is relatively simple, meaning that it does not require highly complex machinery, and the use of an electrolytic solution means that there are no harmful by-products from the process.
Overall, anodizing is a highly advantageous process that offers engineers a wide range of benefits from corrosion resistance to electrical insulation. Its ability to be coloured also makes it ideal for aesthetic applications, and the environmental friendliness of the process makes it an ideal choice for mass production.
Why Choose Ponoko
Anodizing parts at home can be a rewarding DIY project for those who are looking to personally customize and protect metal components made from aluminum. However, trying to anodize parts at scale for professional use introduces a number of challenges that can be difficult to manage without the right equipment and expertise including carefully controlling temperature, electrical current, and the composition of the electrolyte solution.
In a professional environment where precision and reliability are essential, it is prudent to rely on manufacturing specialists who have years of experience and access to advanced technology. Their expertise ensures that each part is anodized to the highest standard, and their access to industry-standard equipment ensures that each part conforms to strict industry requirements.
As such, it is advisable to entrust anodizing to those who have a deep understanding of the process as this ensures that parts meet strict standards. By leaving anodizing to our experts, engineers can focus on their core activities and be assured that the components they use are of the highest quality.
Having manufactured over 2 million parts for 33,000+ customers, our expertise in anodizing positions us uniquely to deliver some of the industry’s best anodized parts. Our refined processes allow for efficient manufacturing while ensuring quality in all parts we produce, and this allows us to handle both small and large orders with ease. As such, our services are ideal for those needing a single part or ten thousand.