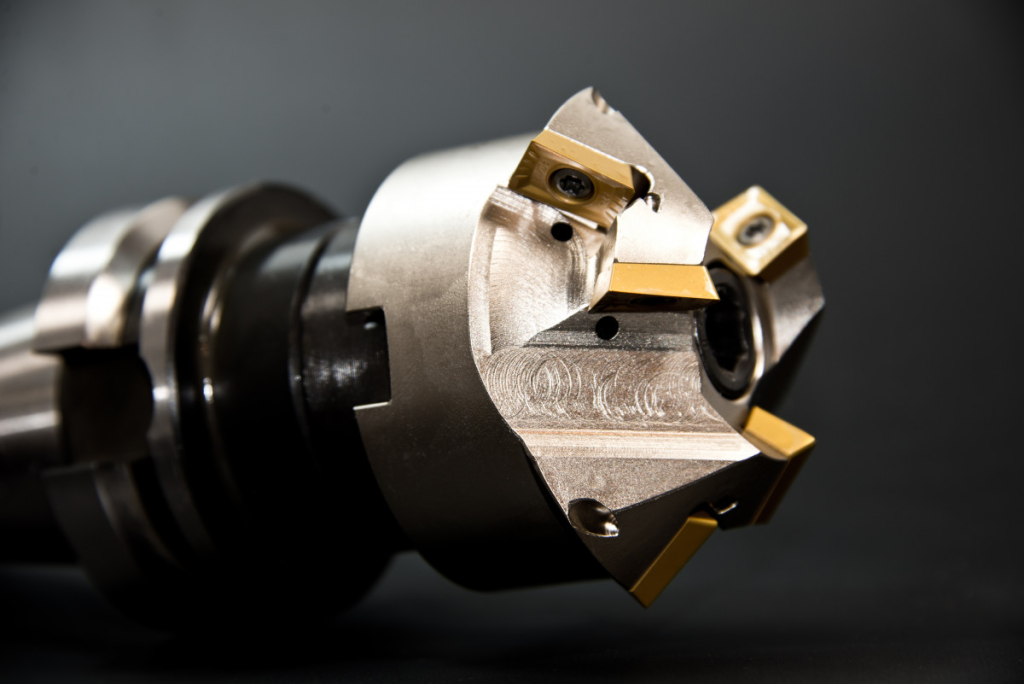
Overview of CNC Machining
As CNC Machining has been around for the better part of 50 years, it has had the opportunity to become an extremely important part of manufacturing, and its use continues to be widespread.
The core operation of a CNC involves a computer sending numeric commands to a controller which then moves individual axis of a toolhead, and this can be used to perform a multitude of different tasks depending on the tool being used. For example, a large drill can be used to make large holes in metal for creating engine blocks, or a small mill can be used to create intricate mechanical parts such as gears and cogs. Even blades can be used by CNCs to cut sheet metal into specific shapes, and these tools can also be used to score metal for later bending.
However, CNCs are not without their faults, and one of these is their extreme slowness. The need for slow feed rates to prevent damage to tools and workpieces also increases the time taken to produce a part, and this increases the cost. But this slow production rate comes with the benefit of extreme precision, something which CNCs are renowned for. In fact, CNCs are so precise that they are often used to create equipment used to create other equipment, such as lathes and other milling machines.
Overall, CNCs continue to play an essential role in the manufacturing industry thanks to their ability to create complex 3D shapes with great precision. Their ability to use a wide range of different tools allows for great versatility, and their slow production rate allows for great precision. But this slow production rate also makes CNCs expensive to run, meaning that they are typically used for prototypes or high-quality engineered parts.
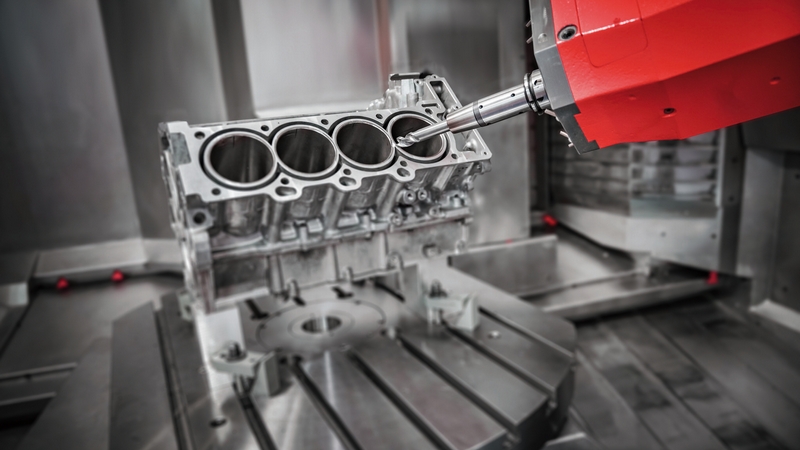
CNC Machining Applications
When it comes to manufacturing, there are numerous technologies available to engineers, including plasma cutting, CNC machining, manual labor, and water blasting. CNCs are typically used with large blocks of metal and have as many as 5-axis, with these machines being able to create very complex 3D structures. However, CNCs are slow and expensive to run as they use tooling bits which wear down over time. Furthermore, they require constant flow of coolant to prevent bits from overheating that can cause further damage to the CNC and the workpiece itself.
As such, CNCs are not typically used in production runs, but instead, are used during prototyping stages. This use case also includes the early stages of product development where engineers require a small batch of parts to test out new designs, while also eliminating the cost for expensive molds or machine setups.
However, CNCs can also be used in production environments for parts that require extreme degrees of precision. This is commonly found in the aerospace industry, where manifolds, connectors, and airfoils need to be manufactured to tight tolerances. The automotive industry can also take advantage of CNC precision, including engine blocks, gearboxes, and valves.
Other unusual applications for CNC milling include scientific equipment, such as pressurized systems, sensor blocks, and unique fittings for specific experimental setups. Fittings for PCBs can also be used to create custom PCB enclosures and cases, while the electronics industry can take advantage of CNCs to create custom heatsinks.
Finally, the fine jewelry industry can also take advantage of the precision offered by CNCs. Materials such as metal and wood can be used to create intricate designs, including small enclosures, decorative pieces, and even functional parts, such as locks and gears.
Overall, CNCs offer engineers a wide range of possibilities, whether prototyping a new product or creating precision parts for mass production.
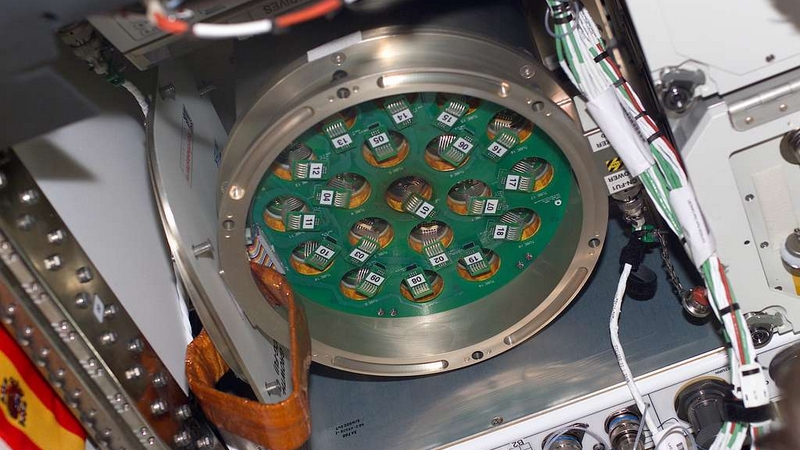
Common Mistakes We’ve Seen
When taking advantage of the many benefits presented by CNCs, it is essential that engineers also take precautions to avoid common mistakes that can lead to project failure. For instance, the ability of CNCs to produce features with great precision should not be taken to mean that features can be made arbitrarily small. In fact, the mechanical forces exerted by cutting tools can cause features to break off if they are too small, meaning that engineers must ensure that features have sufficient material to support them.
Another common mistake that engineers often fall for is failing to take into account the need for access by the cutting tool. The need for the cutting bit to reach the surface of a workpiece means that hollow designs are only possible if they are sliced into individual layers, or have exposed areas that allow for a tool to be inserted. Furthermore, the length of the cutting tool also means that long protrusions from a surface cannot be manufactured using CNC milling, thus engineers should take this into consideration during product design.
The use of CNCs also means that engineers should be mindful of sharp corners, as these can lead to material fracture along the edge. Therefore, engineers should either avoid the use of sharp corners or provide reinforcement to areas that may be prone to cracking.
Finally, the suitability of a material should also be taken into consideration, as the mechanical and physical properties of a material may not be suitable for the application. The tensile strength, density, and malleability of a material can all affect the performance of a part, meaning that engineers must carefully consider these factors before selecting materials.
Overall, while CNCs offer engineers a highly versatile manufacturing option, it is essential that these potential pitfalls are avoided to ensure the success of a project.
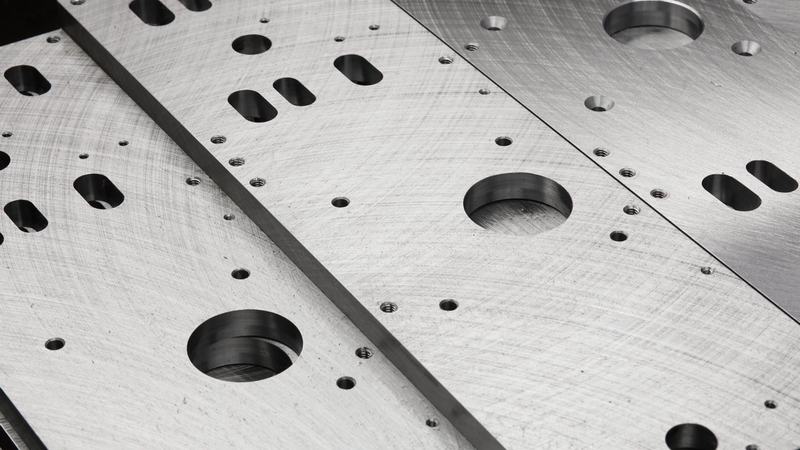
How We’re Different
When it comes to precision and accuracy, CNC machining is hard to beat with the use of axis control and high-precision feed rates, and this makes CNC parts ideal for industries that require precision such as automotive, medical, and defense.
But while CNC parts are precise and accurate, they are unable to be scaled with ease, and last-minute design changes can be costly. For example, trying to scale a CNC part to tens of thousands requires individual designs for each part being manually produced, and any design changes after production has started will result in large sums of money being wasted.
However, our expertise in CNC machining combined with our ability to scale from prototypes to tens of thousands allows for rapid project realization, and our ability to get parts delivered next day for those in NYC allows for design iterations to happen in days instead of months.
Furthermore, our experience in the field of manufacturing means that we can spot design errors and production issues before committing to any manufacturing, helping customers save time and money.
Overall, our ability to rapidly manufacture high-precision parts in any quantity means that engineering projects can realize their goals faster, and our expertise in CNC machining means that parts produced using our services will be perfect first time.
Our Process for Custom CNC Machining Quotes
Getting CNC parts from our service is simple and fast, meaning that you can spend more time focusing on how your part is designed as opposed to what service you need.
Firstly, start by uploading your design to our online uploader, specifying the material that you need, the quantity, and any surface finishes. Once uploaded, our cloud-based software solutions will identify potential manufacturing issues, and one of our experienced engineers will finalize the project and return a quote.
After the quote is paid, our machinists will download your model and get straight to cutting your parts. Once cut, parts are processed as needed (surface finishes etc.), packaged, and shipped to you. For those in the Oakland Bay area, this can be as fast as same day, while those in Mainland US can receive their items as fast as next day.
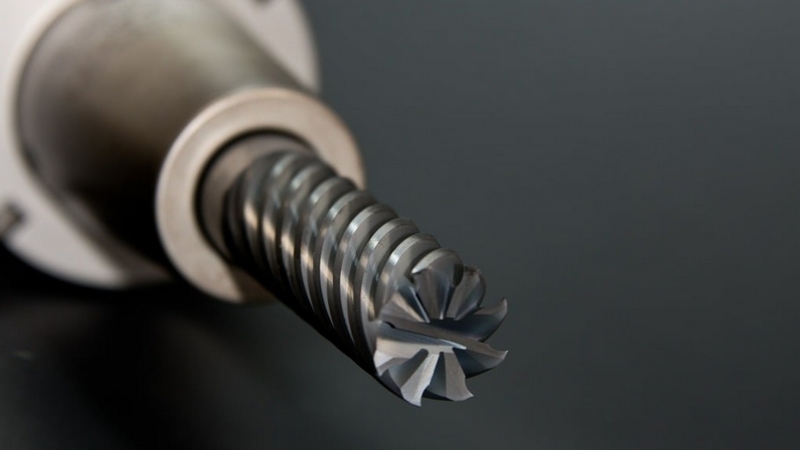
Key Takeaways
When it comes to getting prototypes manufactured, engineers have a wide range of options available to them. However, when it comes to accuracy and precision, CNC machining is arguably one of the best methods available. The use of large cutting bits and low feed rates helps to prevent damage to CNC cutting tools, while also ensuring that the tool bit is straight and true to its axis. This results in parts that are not only highly accurate, but also highly precise, making CNC machining ideal for those needing to produce individual prototypes or low-volume production runs.
Of course, the slow nature of CNC machining means that it can be a costly option, especially if designs change frequently. As such, it is always advantageous for engineers to explore other manufacturing topologies before committing to CNC machining. Luckily, Ponoko is able to work with engineers at every stage of a parts design, providing instant quotes that can be scaled from single pieces all the way to tens of thousands.
However, for those needing to produce thousands of parts, CNC machining becomes an expensive option, and Ponoko offers a wide range of alternative manufacturing techniques, including 3D printing and laser cutting. Ponoko laser cutting, in particular, is an excellent option for those needing to mass-produce parts as Ponoko laser cutters can operate at high feed rates, significantly reducing the time taken to manufacture a part. The ability of Ponoko laser cutters to mass produce parts also makes them ideal for use in future designs, eliminating the need for design changes should additional parts be required.
Overall, Ponoko offers engineers the full spectrum of manufacturing capabilities, allowing prototypes to be developed with the exact same processes used in mass production. This helps to eliminate design errors that can occur when trying to scale a prototype, and ensures that the final part will be production-ready.
Why Choose Ponoko for Your CNC Needs
Our ability to produce laser-cut parts to a high degree of precision for any order size is what makes us stand out amongst manufacturers. Whether it is satellite components, automotive parts, medical products, or custom military pieces, our precision allows for any part to be used in any environment with confidence. Unlike other manufacturers, we are not limited by order quantity, meaning that our prototype parts are on par with finished goods. This means that prototypes can truly be used as a final product, giving engineers a better understanding of their part’s capabilities and limitations.
Furthermore, our ability to scale orders enables manufacturers to move from prototypes to market with the click of a button, and our rapid same-day manufacturing and delivery accelerate project iterations from months to days.
Finally, when moving from prototype to production, the only design files needed are those used to produce the prototype, and after this initial part is produced, all subsequent parts will be manufactured to the exact same standards as that first part.