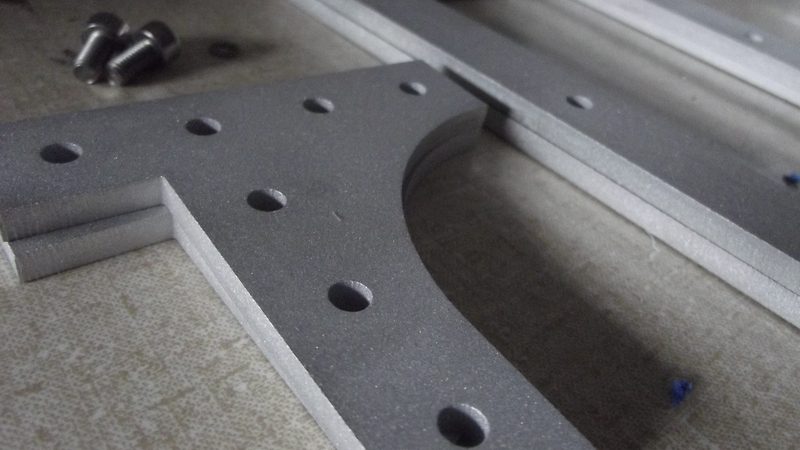
CNC machining is a manufacturing process that is highly regarded for its ability to produce parts with great precision, and this makes it ideal for applications that require parts to fit together seamlessly and function reliably. Many industries, including aerospace and automotive, rely on CNC machining for components that need to meet strict dimensional tolerances and precision standards.
Choosing the right surface finish for CNC-machined parts is essential as the finish can both affect the appearance of the part and its performance. A part that requires a high degree of smoothness, such as a part that will be polished, may require additional machining passes to remove large amounts of material and to help with the polishing process. A part with a rough finish, such as one that will be painted, can take advantage of faster machining times and less detailed machining processes.
The functionality of a part can also influence the choice of surface finish. For example, parts that need to have good grip, such as handles and controls, may benefit from a textured finish, while parts that need to reflect light, such as mirrors, may require a highly polished finish.
Selecting the right surface finish for CNC-machined parts is not always easy, and common mistakes include choosing finishes that are too rough or too smooth for the application as well as not ensuring that all parts manufactured have the same finish. Such mistakes can lead to parts not fitting together correctly or having poor performance characteristics.
When avoiding these pitfalls, it is essential that engineers and machinists work together to ensure the best outcome for a project. Those with years of experience in the field of CNC machining can provide valuable insights into the best materials and machining strategies to use for specific applications.
In essence, while CNC machining is excellent for precision, the choice of surface finish is just as important. A well-considered finish can make all the difference between a parts performance and its appearance.
What Are the Best Surface Finishes – No Finish
In the realm of CNC machining, the choice to leave a surface unfinished is often driven by practical considerations. For many applications, an unfinished CNC machined surface is more than sufficient for its intended function without the need for further refinement, and this approach can be particularly beneficial when the aesthetic appearance of the part is not a primary concern or if the part will not be visible in its final application. For example, internal components of machinery or parts that will be hidden within larger assemblies do not require a polished finish.
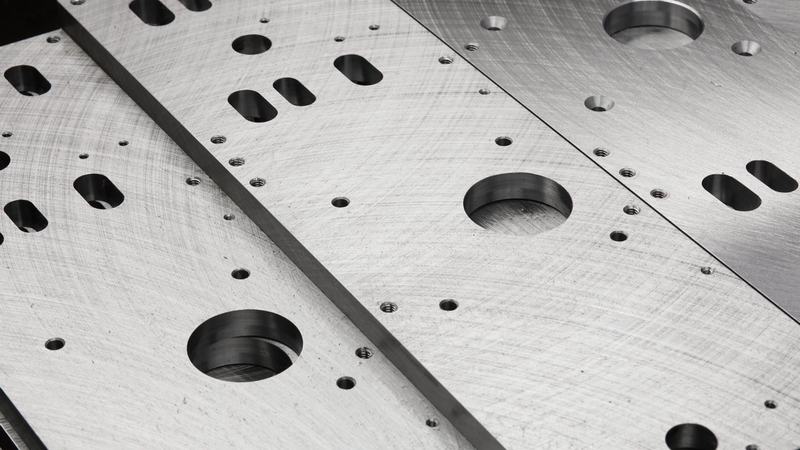
Choosing to forego additional finishing processes on CNC machined parts also leads to significant cost savings as finishing techniques such as sanding and polishing require additional time and resources. By eliminating these steps, manufacturers can reduce production costs, making the parts cheaper to produce, and this cost-effectiveness is especially crucial in industries where large quantities of parts are required or where budget constraints are a significant factor.
However, leaving CNC machined surfaces unfinished also introduces trade-offs that must be considered. One of the most noticeable issues is the visibility of tool path lines which can result in a surface that looks jagged and uneven. This can be problematic for parts that are meant to be aesthetic or where a smooth and uniform appearance is essential.
Achieving a high-quality finish such as a shine or polish on an unfinished CNC machined surface can also be challenging as these typically require additional processes. Without such processes, surfaces are typically matte and lackluster, and this can be a drawback for products where visual appeal is important such as consumer electronics, automotive exteriors, and decorative items. In these cases, the additional effort and cost of finishing are often justified to meet the desired standards of appearance and feel.
What Are the Best Surface Finishes – Powder Coating
Powder coating has become a popular choice for finishing metal parts due to its ease of application and durability. Its ability to provide an even coat ensures uniform coverage, while its ability to adhere strongly to metal surfaces makes it ideal for parts that experience vibration and shock. The ability to customize the curing process also allows for unique properties to be engineered into the coating, such as electrical resistance and surface friction.
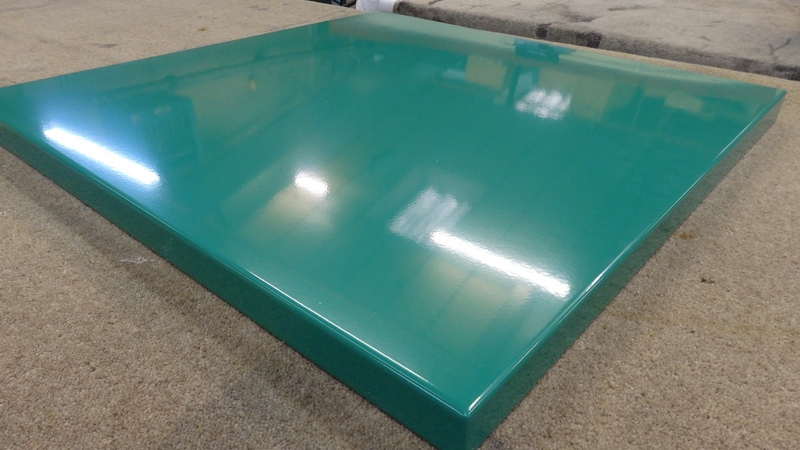
The protective properties of powder coating make it ideal for parts that are exposed to harsh environments. Its chemical resistance protects parts from corrosion, while its abrasion resistance protects parts from mechanical damage. This makes powder-coated parts ideal for outdoor and industrial use, including automotive, agricultural, and construction industries.
The electrical resistance of powder-coated parts also makes it ideal for use in electrical applications, including motor and lighting components. The ability to control surface friction also makes it ideal for applications that require grip, such as vehicle brakes, and the ability to control slipperiness makes it ideal for conveyor belts.
While powder-coated parts are ideal for many applications, they are not without their limitations. The need for a curing process, either via heat or light, means that powder-coated parts cannot be used in applications that require immediate use. The required setup also means that powder coating is less ideal for prototyping, as the need for a large industrial oven or UV facility makes it uneconomical.
The difficulty in achieving uniform coats on small parts also makes powder coating unsuitable for precision miniature parts. However, powder coating is ideal for larger parts that are experiencing significant mechanical vibration and shock, such as automotive and industrial equipment.
What Are the Best Surface Finishes – Polish finish
The need for precision and smooth surfaces is a common thread that runs through various industries, including aerospace and automotive manufacturing, where even the slightest deviation can lead to performance issues. For instance, engine components that are not precisely made will experience vibration and uneven wear, while parts that carry moving mechanical components need to have surfaces that are as smooth as possible to reduce friction. A surface that is highly polished also has a more precise dimensional accuracy due to the removal of imperfections, something which is essential in fields that require parts to fit together with great precision.
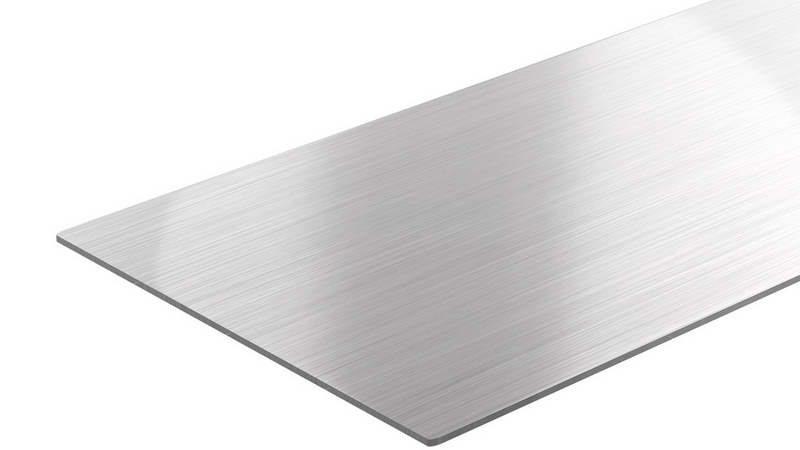
Achieving a high degree of polish requires a multitude of steps, including grinding, sanding, and buffing, which not only takes a long time but also requires great skill. The use of polished surfaces is also often limited due to their fragility, as such surfaces can easily become damaged if not carefully maintained. Exposure to harsh environments, abrasive materials, and even regular cleaning can all lead to the dulling of a polished surface, requiring parts to be re-polished.
As such, the use of polished surfaces is often reserved for applications where their unique properties are essential, including decorative pieces and high-precision mechanical components. In the case of luxury goods, the polished surface represents an element of exclusivity and high quality, while in the case of precision components, the smooth surface and precise dimensional accuracy is essential for performance.
What Are the Best Surface Finishes – Paint
Spray paint is a very popular method for finishing CNC parts due to its economic efficiency, and this is a major factor when mass producing parts. Maintaining high production rates and keeping expenses low is a crucial step for manufacturers, and spray painting allows for this to be achieved.
The versatility of spray paints also plays a key role; they come in a wide variety of colors and finishes that can cater to different aesthetic and functional requirements. For example, manufacturers can choose from matte, glossy, or textured finishes depending on the desired appearance and performance characteristics of the final product. A matte finish can be used to reduce glare while a glossy finish can be used to enhance color vibrancy and appeal. Textured finishes can add a unique tactile quality to parts which is beneficial for some applications.
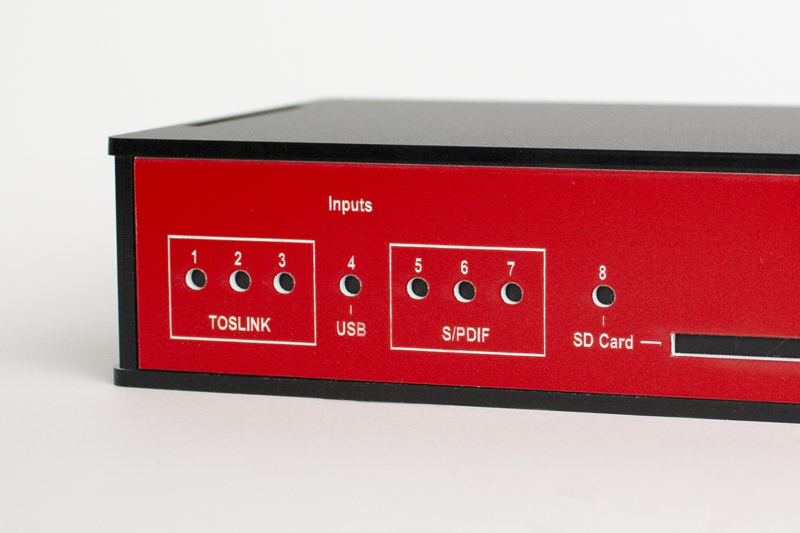
However, despite the many advantages of spray paint, it has its limitations, and one of these is its lack of durability. Paint applied to CNC parts can wear away or scratch easily especially if the part is subjected to constant mechanical use. For example, parts that are frequently handled, connected, or disconnected can quickly show signs of wear as the paint is not as resilient to physical impacts or abrasion as other finishes such as powder coatings or anodized treatments. This means that spray painting may not be suitable for parts that are integral to machinery or those that endure regular mechanical stress.
What Are the Best Surface Finishes – Anodising
Anodising is a specialized process that enhances the natural oxide layer on the surface of metal parts, primarily aluminum, by increasing its thickness and hardness via an electrochemical reaction. To achieve this, aluminum is submerged in an acid electrolytic bath and an electric current passed through the solution, resulting in the growth of the aluminum oxide layer from the metal itself. The layer formed through anodising is highly advantageous for various reasons. Its electrically insulative properties prevent electrical current flow, reducing the risk of electric shocks and making it essential in applications where non-conductive materials are crucial. The toxicity of the layer also makes it safe for use in food and medical industries, eliminating health risks associated with other finishes. Additionally, the extreme chemical stability of the anodised layer ensures resistance to weathering and chemical attacks, making it suitable for long-lasting products. Anodised aluminum is also resistant to corrosion, making it ideal for environments exposed to saltwater and harsh industrial conditions.
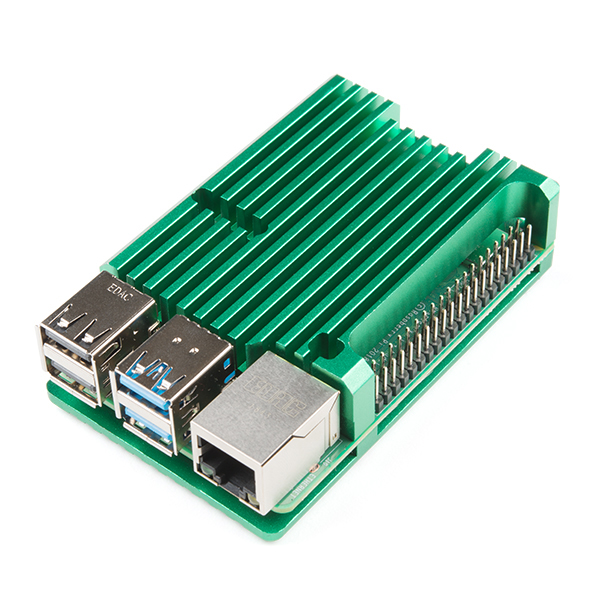
While anodising offers excellent benefits, it is a costly process. The need for specialized equipment, energy, and precise control increases the cost of anodising, making it more expensive than other finishes like powder coating and painting. However, the superior durability and electrical insulation of anodised aluminum make it a cost-effective option in the long run, especially for applications requiring high degrees of corrosion resistance and electrical safety.
Common Mistakes We’ve Seen
When exploring the realm of surface finishes, a typical online search might focus primarily on the technical hurdles of the process itself, such as the importance of surface preparation or the intricacies of maintaining precise current levels during electroplating. These foundational aspects are crucial, yet with our extensive experience in the field, we ensure that such challenges do not impede your project. However, it is essential to recognise that while we excel in executing technical aspects flawlessly, errors often arise from clients not considering the end-use of the parts, environmental conditions, cost, and functionality.
For instance, some clients opt for polished finishes in components destined for corrosive environments, leading to rapid degradation through tarnishing and oxidation, thereby reducing the parts’ lifespan and effectiveness. Additionally, some clients fail to select cost-effective surface finishes, resulting in wasted resources and project budgets. A common example of this includes the use of alternative finishes that offer similar durability and aesthetics at a lower cost, thereby enhancing project viability.
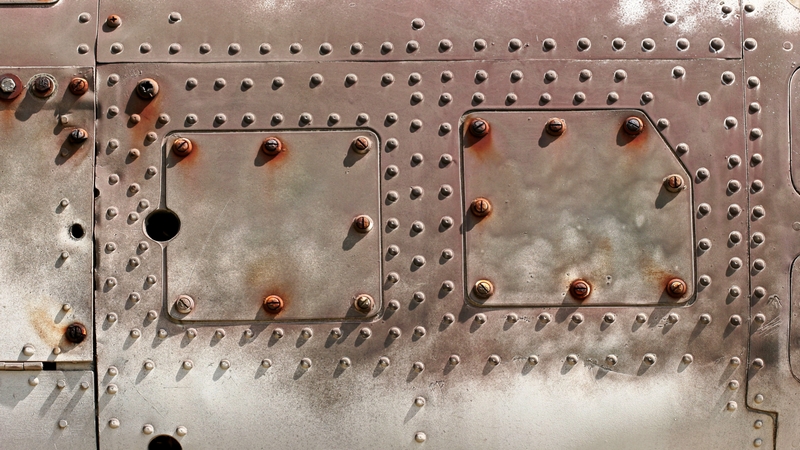
The functionality of parts in assembly and operational processes can also be compromised by poor finish selection. For example, parts requiring adhesive bonding often overlook the need for a rough surface finish, which is essential for adhesion. A smooth finish, which may be aesthetically pleasing, can reduce the bonding strength, leading to weak bonds and potential failures in the final product. Anodization, which offers corrosion resistance and aesthetic appeal, also presents challenges. The resulting insulative barrier can hinder electrical continuity, potentially leading to safety risks and operational inefficiencies, especially in grounded enclosures used in electrical setups.
These examples highlight the importance of understanding the part’s intended use and operational environment. Ensuring that the chosen surface finish aligns with these factors is critical for project success, underscoring the need for thorough planning and consultation during the design phase. By addressing these aspects, clients can avoid costly mistakes and achieve both functional and economical outcomes in their projects.
Why Choose Ponoko for Your CNC Needs
Ponoko is a laser cutting and engraving company that stands out from its competitors due to its ability to navigate the complexities involved with CNC machining. While it may seem that such machining is a straightforward process, numerous decisions must be taken into consideration that not only affect the aesthetic appearance of the final part but also its functionality and durability. The surface finish of a part, for instance, can impact its wear resistance as well as its friction and corrosion properties, but finding reliable information on the best finish for a specific application is often challenging.
Ponoko differentiates itself from other service providers by having a deep understanding of the intricacies involved with CNC machining. This expertise enables Ponoko to effectively guide clients through the production process, addressing both technical and practical concerns along the way. Their technical proficiency also ensures precision manufacturing capabilities, with a 99.7% precision rating, and over 2 million parts manufactured for 33,000 customers.
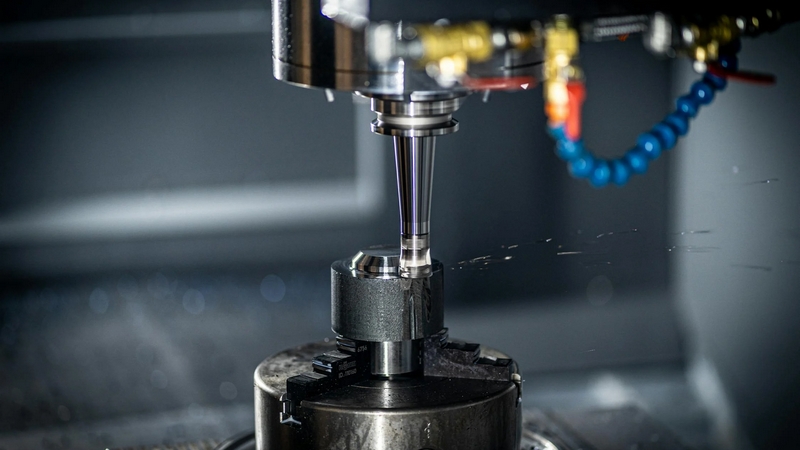
Furthermore, Ponoko offers a 365-day guarantee on all parts, accompanied by a no-questions-asked return policy, which is rare in the industry. This policy demonstrates Ponoko’s confidence in the quality of their work and commitment to customer satisfaction, alleviating risk for customers seeking high-quality CNC parts. The combination of Ponoko’s expertise, precision manufacturing capabilities, and customer-centric approach makes them an excellent choice for those needing top-notch CNC services.
Key Takeaways
The use of CNC milling is superior when creating intricate 3D structures that require accuracy due to the ability for CNC milling to create complex geometries and precision-controlled cuts. However, choosing the right surface finish for CNC-milled parts can be challenging as surface finishes affect the appearance, performance, and durability of the final part.
Surface finishes can also be important for parts operating in specific environments and applications, with common finishes including anodising, spray paint, powder coating, and polishing. Anodising is ideal for parts needing corrosion resistance and wear resistance, while spray paint offers color and aesthetics. Powder coating provides a durable finish resistant to corrosion and wear, and polishing is ideal for aesthetic and material compatibility purposes.
Ponoko’s experience in manufacturing enables a collaborative approach with customers to ensure that all specifications are met, and the use of various manufacturing techniques and finishes helps customers find the best solution for their needs.