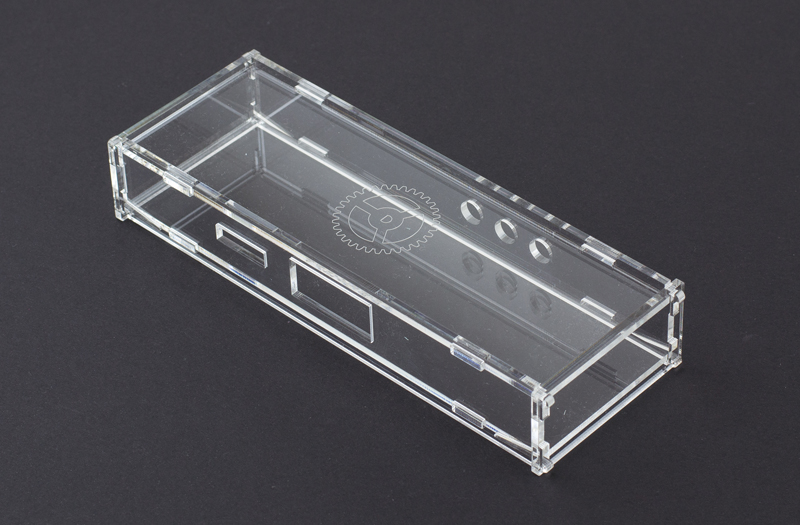
Steps To Take Before Laser Cutting Acrylic Parts
Step 1 – Check that acrylic is the material you need
The first step is to confirm that acrylic is indeed the appropriate material for the application. Environmental factors such as temperature, humidity, and exposure to UV light can affect the performance of acrylic, and therefore, it is important to consider these factors when choosing a material. For example, some acrylics can yellow when exposed to UV light, and therefore, may not be suitable for outdoor applications. Other materials such as acrylic-PETG may be more appropriate for applications that require a high degree of flexibility.
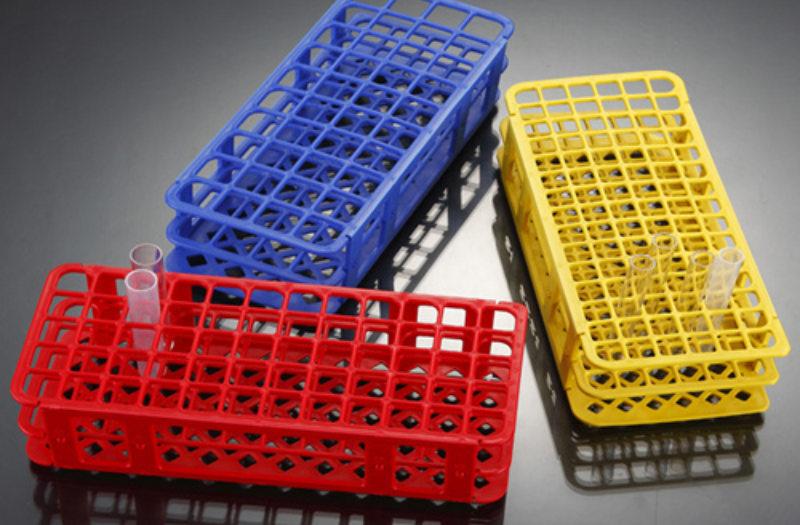
Step 2 – Design your part to our manufacturing tolerances
Just because a CAD package can create perfect parts, that doesn’t mean that such parts can be manufactured in the real world. Due to variations in laser beam width, material tolerances, and the position of the moon and sun, the final measurements of a part will fall within an expected tolerance range. As such, these tolerances need to be carefully considered so that parts will always fit together and be useful in their final application.
Step 3 – Use our instant online quote for a real-time price!
The next step is to use our instant online quote system to get a price for the part. This is also an ideal time to consider material alternatives and production at scale. For example, a design may be able to use a cheaper material, or the use of a different production method may be more cost-effective. Furthermore, the online quote system can also be used to explore different engraving options including colour engraving and metal engraving.
Step 4 -Order before 11AM
Finally, once the design has been confirmed, it should be ordered before 11AM to take advantage of our same-day shipping service. Those in the San Francisco Bay Area can even get their parts delivered to their desk before the end of the day, and those in the mainland US can expect their parts to arrive the very next day. If we fail to deliver on this promise, we will provide a full refund on the shipping cost.
How Does Laser Cutting Acrylic Work?
Being a plastic, acrylic is an excellent material to laser cut as it is easily vapourised, leaves behind virtually no residue, and can be used to create high precision parts. Furthermore, its cost-effective nature makes it great for both prototyping and mass production, and the many material options gives designers plenty of freedom.
Due to the clear nature of acrylic, it needs to be cut using CO2 lasers (powers from 1kW to 10kW) as acrylic is fairly opaque to IR light (CO2 lasers are invisible being in the IR spectrum). Despite fibre lasers having significantly higher powers, only CO2 lasers are capable of producing a high-quality cut and finish. Another advantage to using lower energy lasers is that the parts are not subjected to intense energies which can induce thermal shock (and therefore, potential future warping).
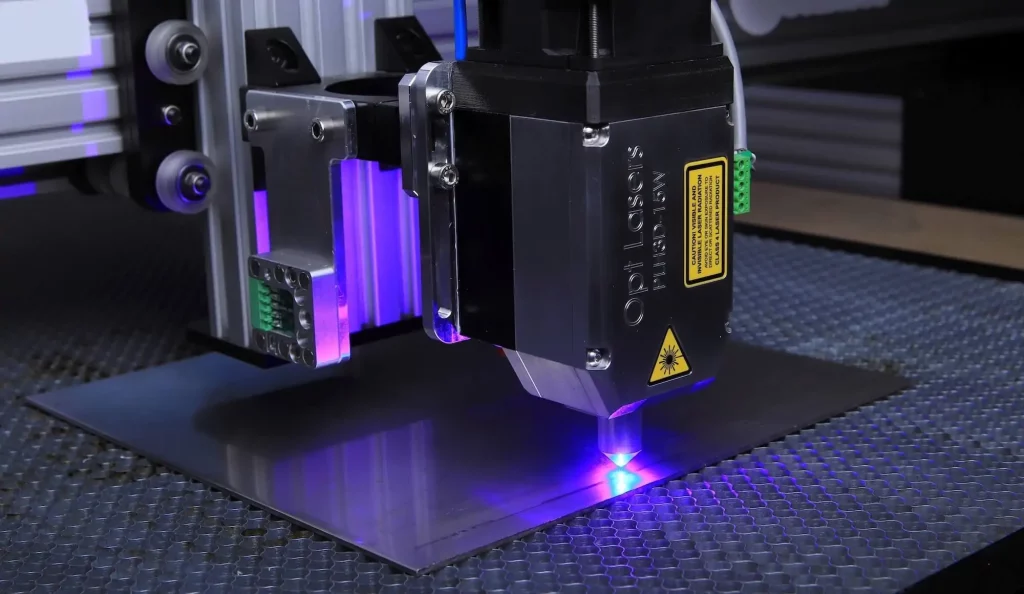
Because CO2 lasers are an order of magnitude cheaper to run and operate compared to fibre lasers, this also allows for acrylic parts to be much more cost-effective (this can be clearly seen with the fact that we have one fibre machine to x CO2 machines).
The first stage in cutting acrylic starts with choosing an appropriate acrylic stock, based on the custom requirements (color, size, thickness etc.). Once chosen, the material is carefully placed onto the cutting bed of the laser cutter, and the machine performs a calibration cycle to ensure that the material is properly secured and positioned.
After this initial setup, the design to be cut is loaded into the laser cutter, and the machine begins the cutting process. Once completed, the operator can disengage the laser, gather the cut parts, and recycle the larger stock material that has been left behind.
Types of Acrylic You Can Laser Cut
Acrylic is a family of plastics that come in a wide range of different types, each with its own unique characteristics. One such characteristic that varies between different types of acrylic is the surface finish, with some being smooth and clear, while others have a matt texture. This means that designers can take advantage of different textures to create unique aesthetics, but this also means that some acrylics are better suited for certain applications than others. For example, smooth acrylic is ideal for engraving and printing, while matt acrylic is ideal for hiding scratches and fingerprints.
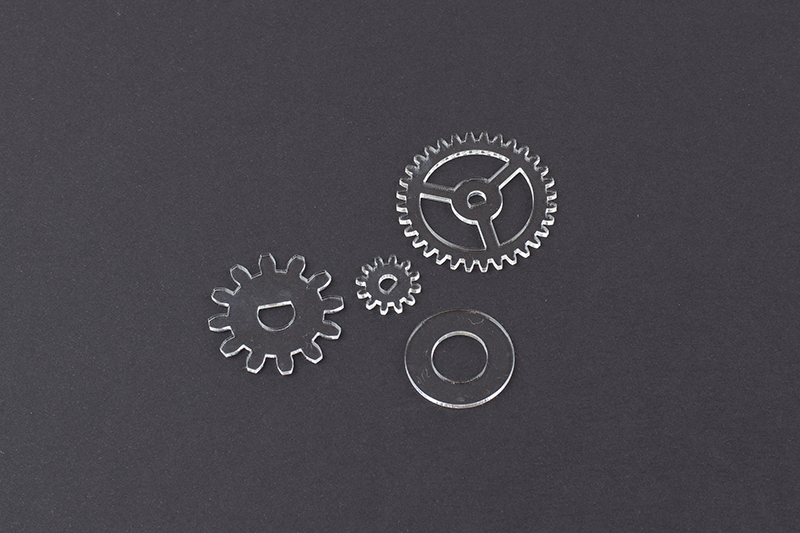
Another characteristic that varies between different types of acrylic is the color. Acrylic can be made in a wide range of colors, including opaque, semi-transparent, and clear. This means that acrylic can be used in a wide range of applications, including signs, enclosures, and light guides. Furthermore, the opacity of acrylic can also be useful for hiding the contents of a design, such as the inside of a box or the electronics inside a product.
Impact-modified acrylic is another type of acrylic that is ideal for applications that may be subjected to sudden forces. This type of acrylic is designed to absorb sudden forces, thereby reducing the risk of damage, but this comes at the cost of reducing the transparency of the material. This type of acrylic is ideal for applications that need to be able to withstand shock, such as enclosures and product packaging.
IR transmitting acrylic is another type of acrylic that is ideal for applications that need to block all light except IR. This type of acrylic is ideal for remote controls, sensors, and other applications that need to be able to see IR light, but not visible light. This type of acrylic is also ideal for applications that need to be able to transmit IR light, such as IR cameras and sensors.
The Proper Way To Laser Cut Acrylic
We are often told that there is no right or wrong way with doing things, but when it comes to laser cutting acrylic, there is indeed a proper way to do so!
The first consideration that engineers must take when handling acrylic is that the material is coated with a protective layer. These layers are left on the material right up until the point of laser cutting and ensure that the acrylic does not scratch during transportation. If these layers are removed prior to laser cutting, then any mechanical force against the acrylic will result in scratching.
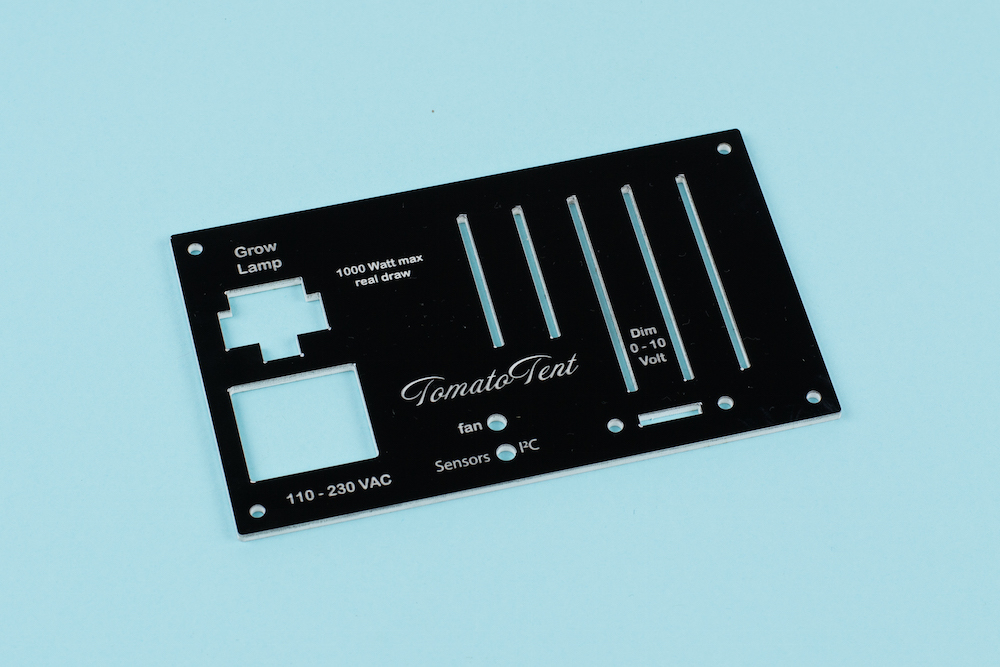
Another consideration that engineers must take is the type of laser used. As acrylic is transparent to visible light, only those that use wavelengths absorbed by acrylic can be used. Thus, only laser cutters that use UV or IR beams can cut acrylic effectively.
During the laser cutting process, vapourised acrylic can settle on sensitive components such as mirrors and waveguides. Therefore, laser cutting stations must have the proper extraction systems that not only prevent this issue, but also catch contaminates that might otherwise affect the local air quality.
The distance between the laser head and the acrylic also plays a crucial role in laser kerf (the divergence in the width of the cutting beam). To minimise deviations in the final part, the width of this beam should be as consistent as possible. Therefore, the distance between the laser head and the acrylic remains constant, requiring an extremely level bed.
What Type Of Laser Cutters Can Cut Acrylic?
As acrylic is often clear, using a laser cutter that produces a visible beam is out of the question. Thankfully, acrylic is 98% absorbent to IR and UV light meaning that CO2 lasers are by far the best choice when laser cutting acrylic. While fibre lasers are extremely powerful and able to cut through some of the toughest materials, their ability to cut right through acrylic without fully cutting makes them unsuitable for acrylic. As such, CO2 lasers are not only able to cut acrylic efficiently, but can do so with great precision.
Examples of Laser Cut Acrylic Projects
Raspberry Pi Enclosure
The Raspberry Pi is an excellent example of a device that has become immensely popular amongst most industries due to its versatility, and the enclosure developed for the Raspberry Pi perfectly demonstrates how 3D shapes can be constructed using 2D parts. This concept can be applied to any project that requires a 3D enclosure, and the use of laser-cut acrylic makes this even more feasible.
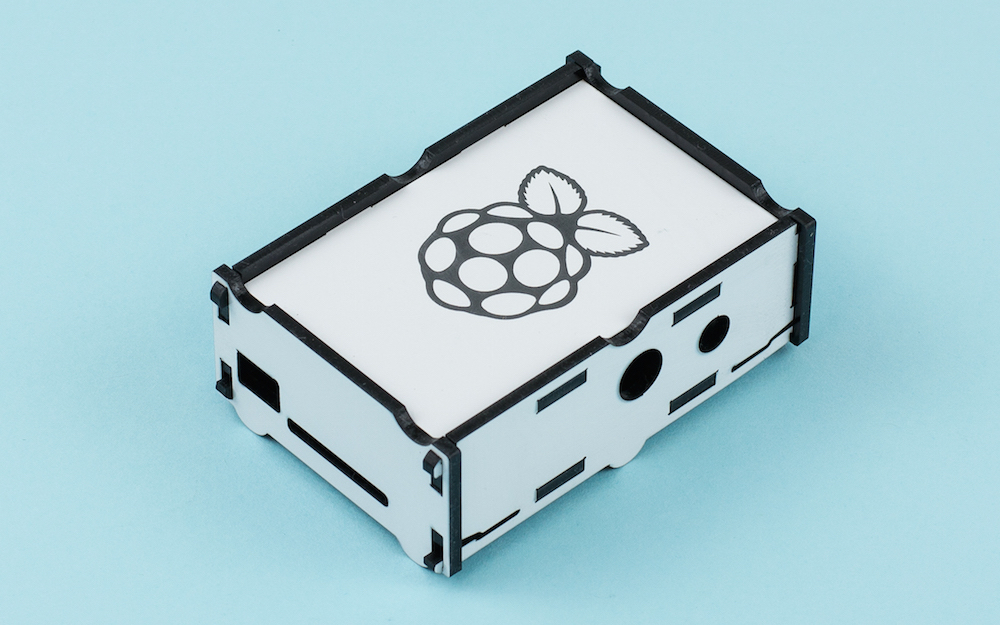
JTAGulator
The JTAGulator is not just a project that helps engineers with extracting firmware from JTAG devices, but can also be a great candidate for those looking to create an enclosure for an electronics project. The project featured on our site perfectly shows how acrylic can be used to create enclosures for such projects, and also demonstrates the ability for acrylic to be used not just in prototyping, but in mass production as well.
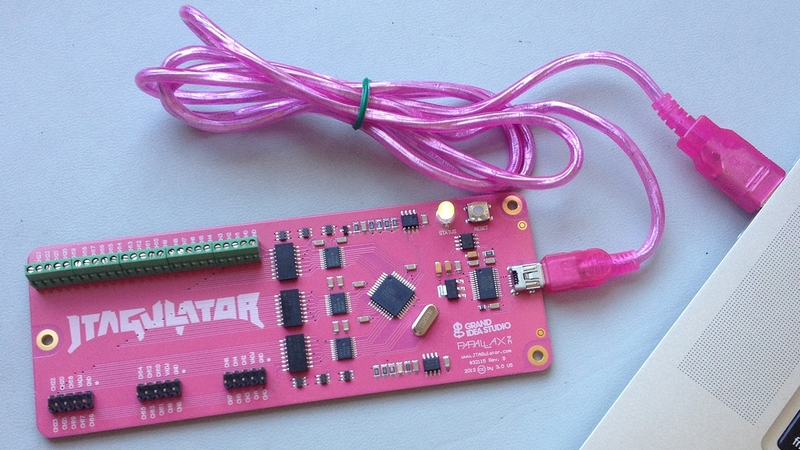
Jewellery Stand
Engineering is a big part of laser cutting, but that doesn’t mean that only engineers can use our services. One project that we have featured on our site is a jewellery stand, made entirely from 2D parts cut using our online laser cutting service. This project not only shows how almost any application can take advantage of laser cutting, but how even unique and niche industries such as fashion, arts, and graphics can also utilise this fast manufacturing technique.
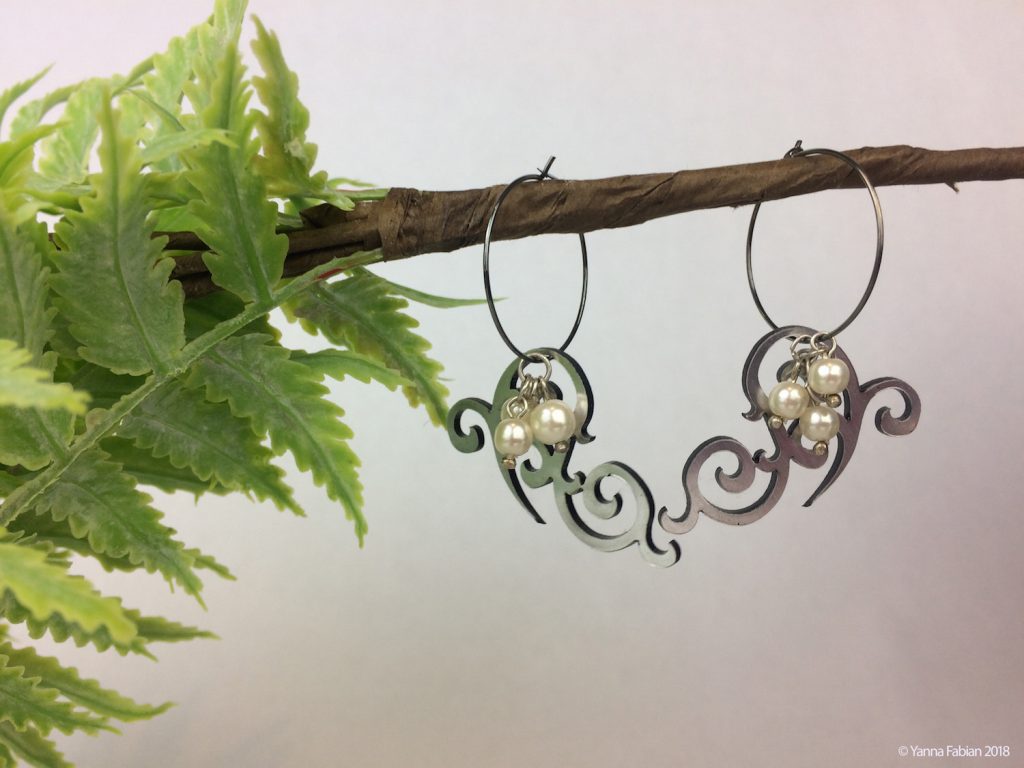
LED Shop Signs
As previously mentioned, clear acrylic signs that are engraved can be used with LED lights to create extremely impressive signage. This makes them extremely useful in shop signage, whether it is inside or outside of a shop. But what makes acrylic shop signs even more advantageous is that compared to the classic neon signs, as they use LEDs, their low voltage nature makes them safer to install and operate (that and there is no fragile glass).
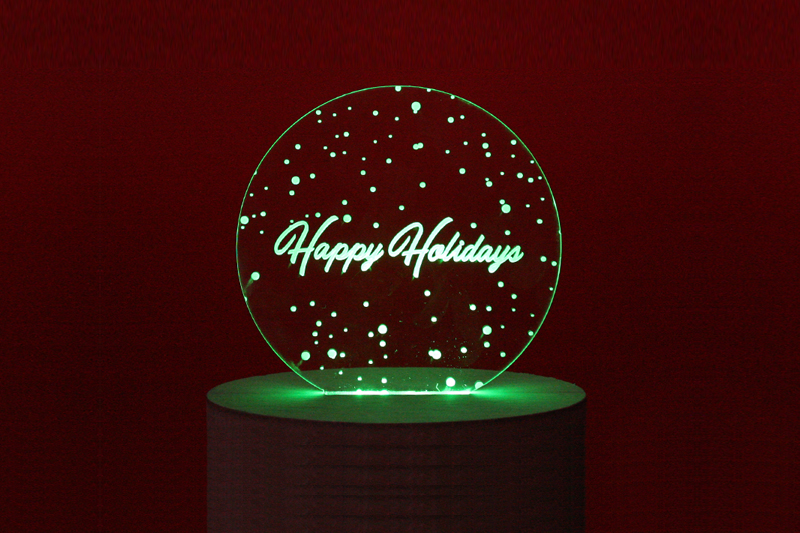
Acrylic FAQ
How thick can laser cut acrylic parts be?
Ponoko offers a wide selection of acrylic materials in various thicknesses to meet any project needs. The thickest acrylic material available in our inventory is 9mm (approximately 0.35 inches), but it is important to note that as the thickness of the acrylic material increases, the laser kerf (the width of the cut made by the laser), also becomes larger. This means that the precision of the cut may be slightly affected with thicker materials, so it’s something to keep in mind when planning your project.
What applications can laser-cut acrylic be used in?
Acrylic is a versatile material suitable for a wide range of applications. It is commonly used in engineering projects that require faceplates due to its durability and ease of customization through laser cutting. Clear acrylic serves as effective light guides, enhancing illumination in various products, and acrylic is also ideal for signage and notices, offering clarity and durability for indoor and outdoor use. Its decorative versatility makes it a popular choice for artistic and design purposes, and the plastic nature of acrylic makes it suitable for applications involving hygiene, as it can be easily cleaned with alcohol and disinfectants, ensuring cleanliness and safety.
What disadvantages does acrylic have?
Acrylic, although widely used, possesses several drawbacks. Firstly, it has a low melting point, rendering it susceptible to deformation when exposed to high temperatures. Secondly, acrylic is brittle and can shatter under significant force or pressure, requiring cautious handling, particularly when fastening with bolts. Moreover, acrylic is prone to degradation when exposed to ultraviolet (UV) radiation, leading to discolouration and weakening over time. Additionally, acrylic surfaces are easily scratched, necessitating careful maintenance to preserve their clarity and appearance.
Can acrylic be engraved?
Acrylic is highly suitable for engraving purposes. Whether clear or opaque, acrylic offers excellent engraving capabilities. Clear acrylic, in particular, is well-suited for engraving as it allows for the use of side LEDs for illumination, enhancing the visibility of the engraved designs. However, it’s worth noting that engraving on opaque acrylic may result in less visibility of the engraved markings compared to clear acrylic. Overall, acrylic presents a versatile and effective material for engraving applications.
Is acrylic suitable for mass production?
Acrylic is indeed an excellent choice for mass production. Whether in high volumes or low, laser cutting remains the optimal method for machining acrylic. With no need for additional machining such as tabs, the process is streamlined, ensuring efficiency and consistency. Additionally, the surface finish of laser-cut acrylic surpasses that of traditional machining methods, contributing to a high-quality final product.
What environmental factors should be considered with acrylic?
Acrylic should not be exposed to direct sunlight, as it can lead to degradation. Large temperature swings can cause acrylic to crack, especially when under pressure. For outdoor applications, impact-modified acrylic is recommended for its durability. Acrylic is water-resistant and an effective electrical insulator, making it suitable for electrical enclosures. However, acrylic is combustible and should not be used in critical applications requiring flame retardants, such as aerospace components.